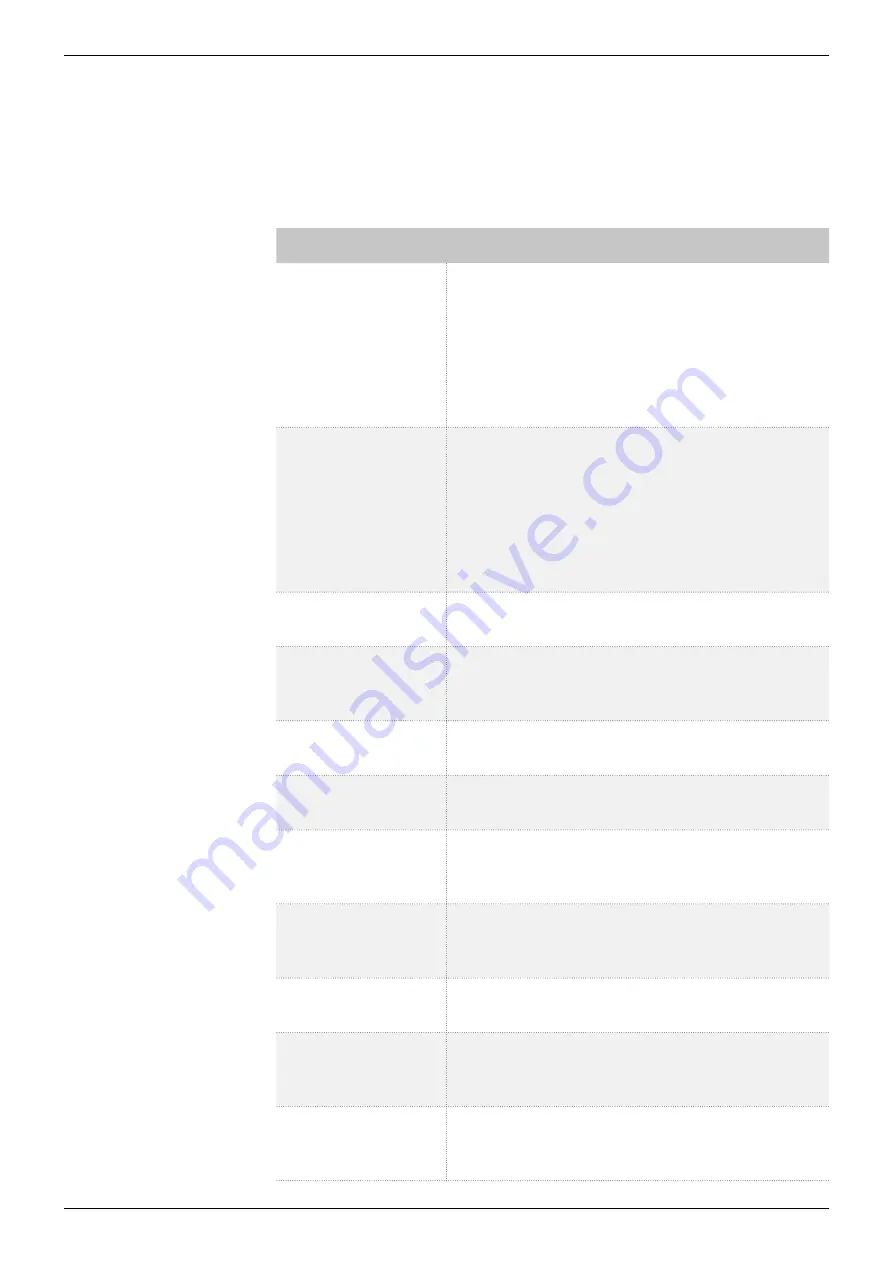
43
Troubleshooting
BlueShadow Pump 40P Instructions V7613
7.3 System messages
If other system messages are displayed on the display besides those
listed below, please turn the device off and then on. Inform the technical
support in case the system message repeats.
The system messages are in alphabetical order:
System message
A
Auto pump head
type: head data
uninitialized!
Switch the device off and on
Check whether a pump head with RFID
recogni tion has been installed
Repeat the automatic configuration step in
the chromatography software
Remove pump head, clean it and install it
again
Auto pump head
type: no head
detected!
Switch the device off and on
Repeat automatic configuration in the
chroma tography software
Remove pump head, clean it and install it
again
Check whether a pump head with RFID
recogni tion has been installed
C
Cannot delete
active program/link
Pause active program as well as Link and the
delete the link.
Cannot edit
program from the
running link
First pause the link, then edit the data on the de-
vice display or in the chromatography software.
Cannot initialize
LAN
Check the cables and connections in the local
area network.
Cannot operate
with an empty link
The link is empty. First create a link.
Cannot read data
from FRAM
Switch the device off and on. If the system mes-
sage appears again, notify the manufacturer for
technical support.
Cannot read RTC
Switch the device off and on. If the system mes-
sage appears again, notify the manufacturer for
technical support.
Cannot start time
table
Edit the data on the device display or in the
chro matography software.
Cannot use
non-existing
compo nent!
Change the setup settings or change the gra-
dient in the program or in setup.
Cannot write data
on FRAM
Switch the device off and on. If the system mes-
sage appears again, notify the manufacturer for
technical support.