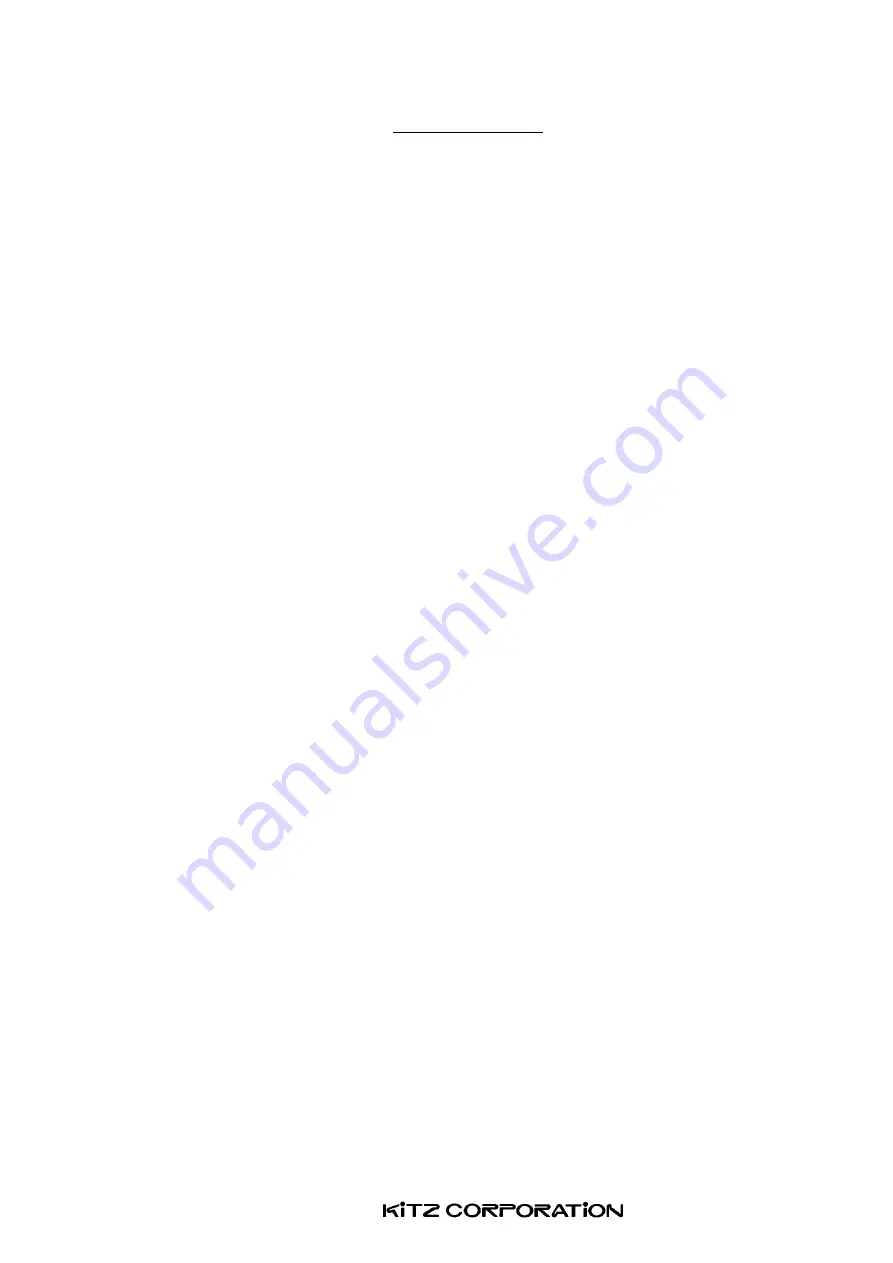
Document No.: KE-2015-00 23/34
Ⅵ. Periodic Inspection
1. Periodic Inspections
1.1 Perform periodic inspections on dampers in the as-installed condition at least once a year.
1.2 Check if dampers are operated smoothly and safely.
1.3 Inspection items and methods are the same as those for daily inspections. See Chapter V, 3.
Daily Inspection of this manual for details.
1.4 Perform periodic inspections on dampers that are not inspected or not operated on a daily basis.
(Periodic inspections shall be performed on all the dampers.)
1.5 Thorough checks are required for the dampers if:
a) Operational failure of the damper could result in a shutdown of the entire plant unit.
b) Fluids are highly viscous and may get stuck to and built up.
c) Corrosion and/or wear by the fluids are likely to occur.
Remove the damper from the pipeline for inspection if needed.
Summary of Contents for KE-2015-00
Page 4: ...Document No KE 2015 00 1 34 Ⅰ Construction and Design Features ...
Page 11: ...Document No KE 2015 00 8 34 Ⅱ Operating Device ...
Page 14: ...Document No KE 2015 00 11 34 Ⅲ Transportation and Storage ...
Page 17: ...Document No KE 2015 00 14 34 Ⅳ Installation ...
Page 21: ...Document No KE 2015 00 18 34 Ⅴ Operation ...
Page 25: ...Document No KE 2015 00 22 34 Ⅵ Periodic Inspection ...
Page 29: ...Document No KE 2015 00 26 34 Ⅶ Disassembly and Reassembly ...