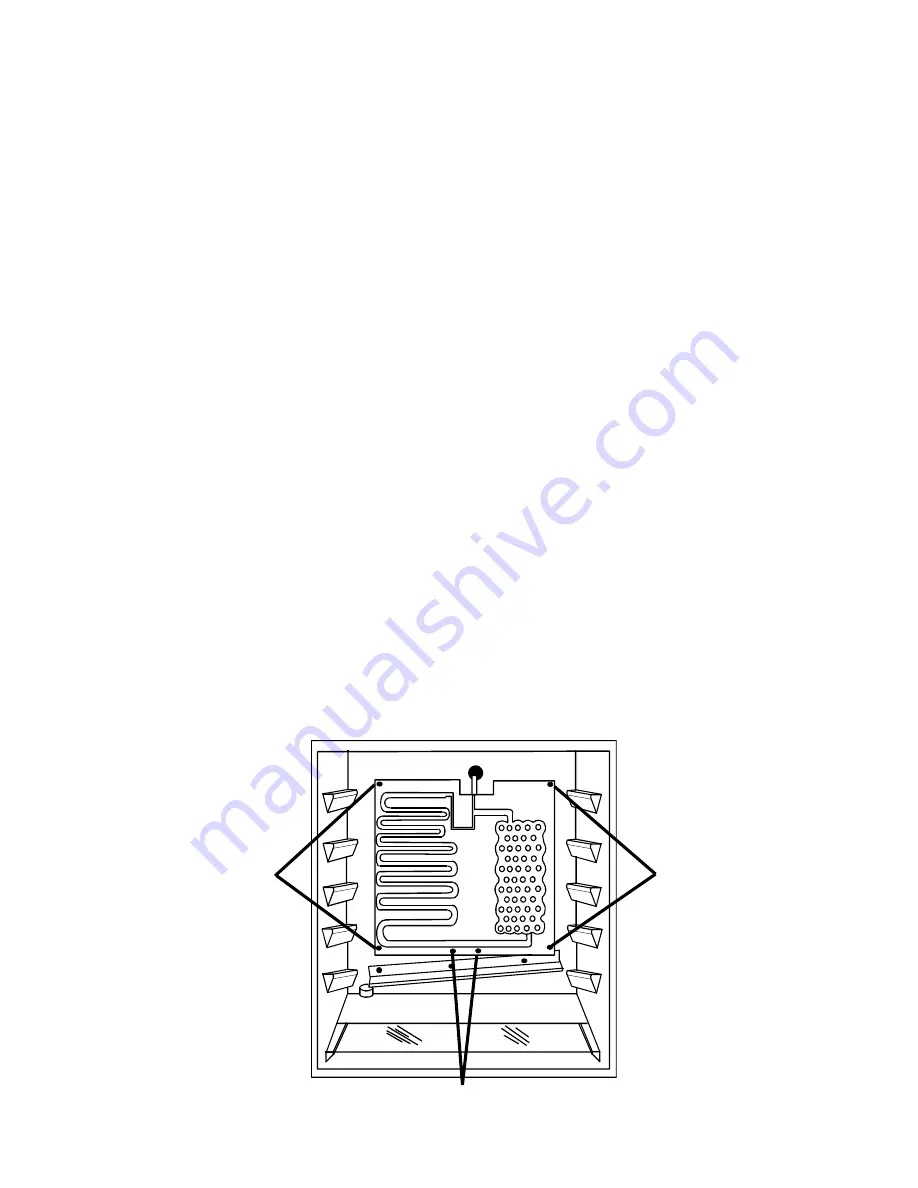
6
EVAPORATOR ASSEMBLY
The evaporator and heat exchanger is one assembly. The capillary tube and suction tube are cap-
tured inside a metal "sandwich". Refrigerant circulates through a cavity that is molded into the evapo-
rator assembly.
The evaporator is secured to the back wall of the inner cabinet liner with screws and can be removed
if replacement is necessary.
The capillary tube is routed inside the suction line. The entire heat exchanger assembly is accessible
by removing the back panel of the wine cellar.
Removing the Evaporator
To remove the evaporator, first follow the steps to remove the back panel of the wine cellar on page 5
and follow the procedure for purging the sealed system found in the Job Aid,
Sweep Charge Proce-
dures for the 90's
, Part No. LIT4321717.
1. Disconnect the electric power from the appliance.
2. Score and snap off the capillary tube at the inlet to the filter-dryer.
3. Unbraze the suction line from the compressor inlet.
4. Remove the two (2) screws securing each of the bottle racks to the sides of the cabinet liner
and remove all of the bottle racks.
5. Loosen the two (2) philips-head thermostat sensor retainer screws at the bottom of the evapo-
rator.
6. Remove the four (4) philips-head screws securing the evaporator to the back wall of the
cabinet liner.
7. Carefully pull the evaporator from the unit making sure the heat exchanger passes through
the access hole in the back of the cabinet without snagging or damaging the foam insulation
on the outside back of the unit.
REMOVE THESE
SCREWS
REMOVE THESE
SCREWS
LOOSEN THESE SCREWS