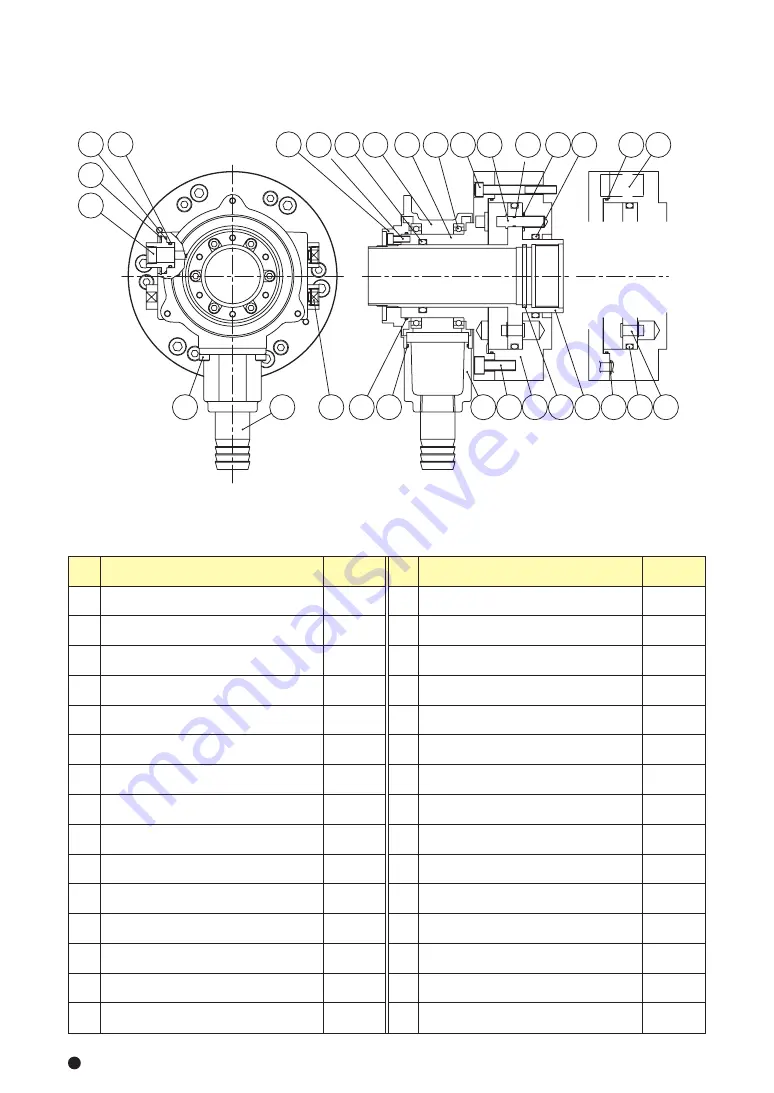
5
6
Important safety precautions are summarized below. Please read this section before first
starting to use this product.
Fig. 3
Table 1
No.
1
2
3
4
5
6
7
8
9
10
11
12
13
14
15
No.
16
17
18
19
20
21
22
23
24
25
26
27
28
29
30
Quantity
2
2
1
1
1
1
2
1
1
2
1
4
2
6
6
Part name
Part name
Lock valve
Relief valve
Cylinder
Rotary valve
Sleeve
Piston
Guide pin
Stopper
Under body
Hose nipple
Bearing
Joint
Plug
Socket head cap screw
Socket head cap screw
Socket head cap screw
Socket head cap screw
Retaining ring S
Retaining ring H
O-ring
O-ring
O-ring
O-ring
O-ring
O-ring
O-ring
O-ring
O-ring
O-ring
O-ring
Quantity
6or10or12
6
2
4
5
1
1
1
1
2
1
1
1
4
4
Turn off main power supply before attaching, inspecting or replacing cylinder,
and before adding oil.
For All Users
・The cylinder may start rotation suddenly,
and a part of the body or clothing may be
caught.
Close door before rotating spindle.
For All Users
・If the door is not closed, you may touch
the rotating chuck or the work may fly out,
which is very dangerous. (In general, the
safety interlock function which allows
rotation only when the door is the manual
mode or the test mode)
During spindle rotation, do not turn off hydraulic pump power supply and
do not operate switching valve.
For All Users
・Cutting off hydraulic pressure
causes a drop in the gripping
force which could result in the
work being released and flying
out.
・Operating the manual switching
valve or solenoid valve will lead to
a drop of hydraulic pressure.
2 . Important Safety Precautions
Failure to follow the safety precautions below will result in
serious injury or death.
DANGER
Main power supply
Lathe
OFF
OFF
ON
Lathe
Close
Work
Manual switching valve
Solenoid valve
Jaw closed
Jaw open
NO
1−4 Parts list
ON
OFF
16
24
29
26
25
15
11
30
21
18
1
20
17
2
28
8
10
19
5
4
6
23
13
14
12
27
3
22
7
9
Summary of Contents for SR1146
Page 31: ......