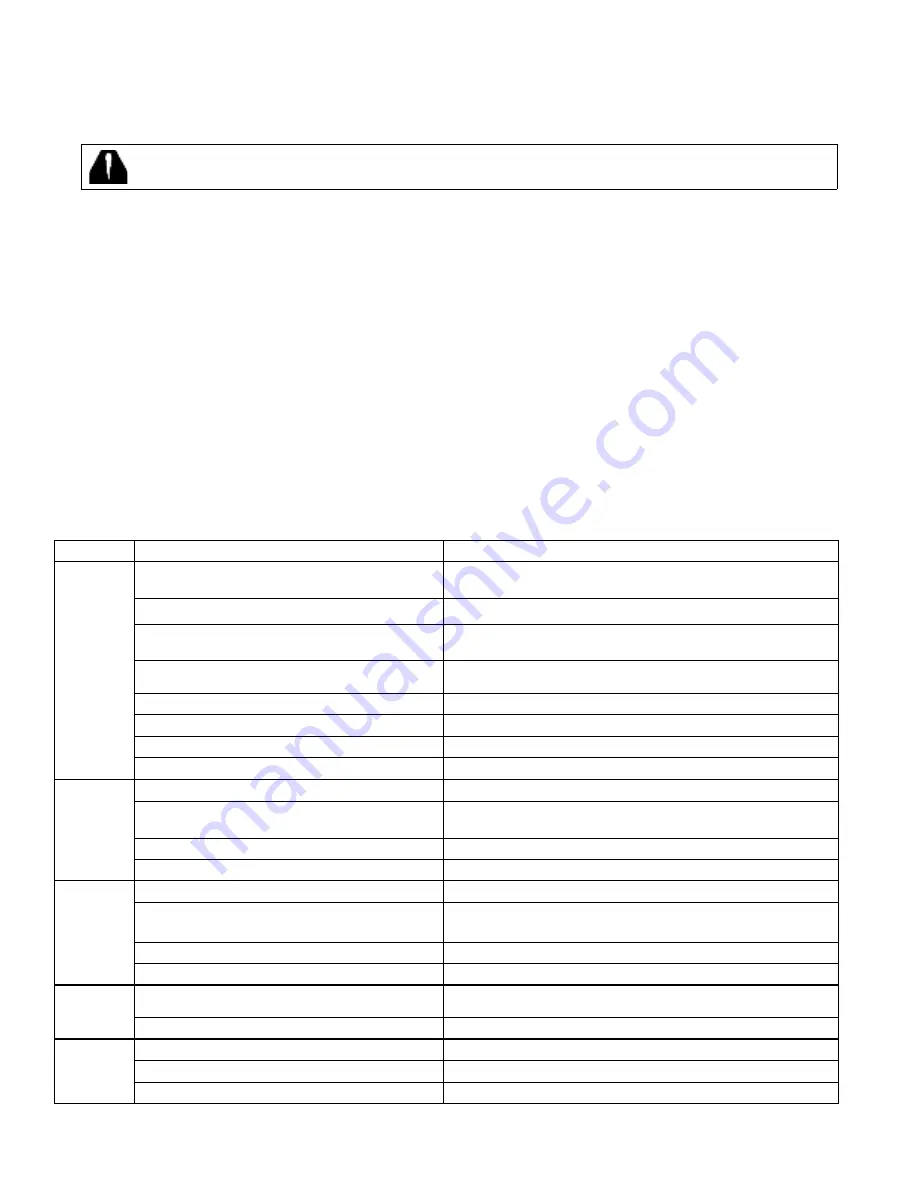
14
8. Place the closed head slide-pin on the piston slide with the flat edge toward the piston. With the inlet ports facing down, insert
the piston and pin into the cylinder.
9. Press the sleeve, bearing into the closed head. Apply a thin coat of Loctite 515 or equal, sealing compound to the sealing
surfaces of the head and cylinder. Insert the two dowel pins into the cylinder and install the closed head. Tighten cap screws
evenly.
CAUTION: Sealing compound must be used sparingly to prevent squeezing it into the pump when tightening
heads. Allow compound to become tacky before installing heads.
10. Place the cam keys in the shaft grooves and tap the outer cam onto the shaft with the threaded holes of the cam outward.
11. Place the open head slide-pin on the piston slide with the flat edge toward the piston and insert the piston and pin into the
cylinder with the inlet ports of the piston facing down.
12. Install the open head the same as the closed head.
13. Slip the backup ring on the shaft and install the rotating part of the shaft seal.
14. Press the stationary part of the shaft seal in the bearing housing and install the bearing housing. Install the bearing on the
shaft and into the housing and replace the lock nut on the shaft.
15. Install discharge valves. Replace the valve deck cover and air/oil baffle assembly.
16. Install the separator housing and gasket.
17. Replace the oil sight gauge and replace the separator housing cover and gasket.
18. Replace the housing and oil circulating pump. Replace all oil lines and components.
19. Replace the motor and sheaves.
20. Replace and tension the V-belts and install the belt guard.
21. Reach through the suction port and pour 4 quarts (2 litres) of oil on the slide-pins and finish filling the pump with oil
22. Connect the electrical, water and manifolding connections to the pump.
23. Run the pump and test that the pump can obtain satisfactory ultimate pressure.
TROUBLESHOOTING
SYMPTOM
POSSIBLE CAUSE
REMEDY
System
ultimate
pressure
excessively
high
Process equipment contaminated by high vapor
pressure material
(a) Clean equipment with acetone,alcohol or ether
(b) Pump down with vacuum pump overnight
Process equipment or pump leaks.
Leak check process equipment, repair leaks as necessary
Oil flow restricted, oil level should change with pump
pressure
Correct oil flow. Remove restrictions.
Vacuum pump oil contaminated
Change pump oil. See CHANGING PUMP OIL, and OIL
CONTAMINATION
Discharge valve malfunctioning
Check valves per DISCHARGE VALVES
Vacuum pump shaft seal malfunctioning
Check shaft seal per SHAFT SEAL
Vacuum pump internal parts worn or damaged
Dismantle pump and inspect internal parts. See DISASSEMBLY
Hydraulic noise of pump discharge
Open gas ballast valve
Pump stalls
Electric power loss
Check power at motor
Belts slipping. Pump malfunctioning.Pump oil
contaminated or pump is not sufficiently lubricated.
See INSTALLATION, V-BELT DRIVE,and CHANGING THE OIL.
Foreign material or coating build up inthe pump
Clean the pump
Pump discharge line is blocked
Clear pump discharge line. Check oil mist eliminator for blockage.
Pump will
not start
Electrical Failure
Check for power at motor, Check motor start controls and motor.
Pump flooded with oil
Clear oil from pump by turning pump over by hand, or disassembling
pump. Verify that vent and discharge valves are fuctioning properly
Pump too cold
See OPERATION, GENERAL
Foreign particles in pump
Disassemble and clean pump.
Pump
vibrates
Inlet or outlet connections not flexible
Use Tuthill Vacuum & Blower Systems connectors or more flexible
connectors
Vibration mounts incorrect or not positioned properly
Check to ensure that vibration mounts are correctly installed
Oil in pump
inlet piping
Piping at incorrect level
Add inlet elbow
Gas ballast valve left open when stopping the pump
Add manual or automatic valve
No isolation valve and vent valve
Add vent valve