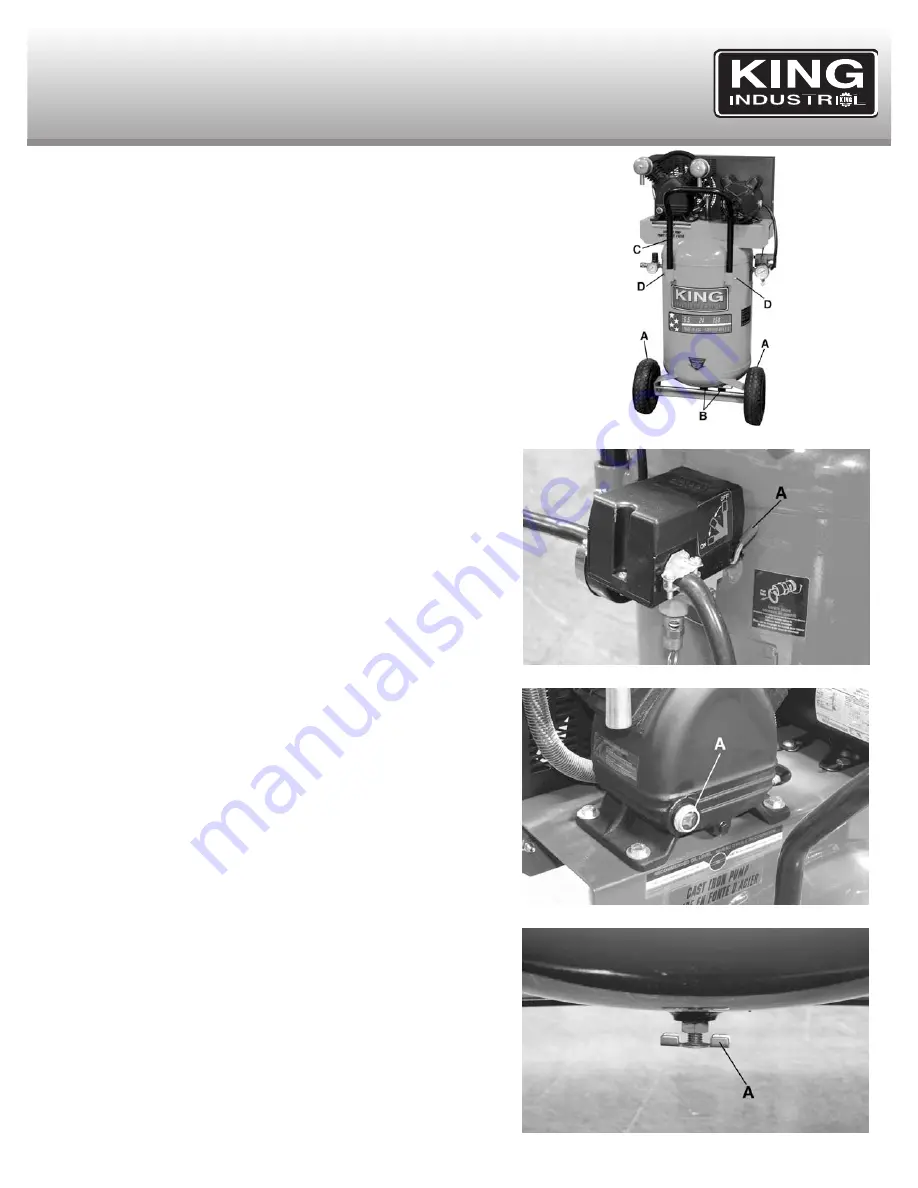
ASSEMBLY &
BREAK-IN PROCEDURES
ASSEMBLY AND LOCATION OF THE AIR COMPRESSOR
Your compressor requires some minor assembly. Install both 9-1/2” wheels
(A) Fig.3 using wheel shaft and cotter pins supplied. Then install the rubber
feet (B) using pan head screws and flange head hex. nuts. Install handle (C)
to the tank and secure handle using 2 hex. bolts (D).
Operate the air compressor in a dry, clean, cool, well ventilated area. The air
compressor pump and case are designed to allow for proper cooling. Clean
or blow off dust or dirt that collects on the air compressor. A clean air
compressor runs cooler and provides longer service. The ventilation
openings on your air compressor are necessary to maintain proper
operating temperature. Do not place rags or other containers on or near
these openings.
*IMPORTANT BREAK-IN PROCEDURES*
NOTE: SERIOUS DAMAGE MAY RESULT IF THE FOLLOWING BREAK-
IN INSTRUCTIONS ARE NOT CLOSELY
FOLLOWED. THESE
PROCEDURES ARE REQUIRED BEFORE THE AIR COMPRESSOR CAN
BE PUT INTO SERVICE, AFTER REPLACING THE CHECK VALVE, AND
WHEN A PISTON OR A CYLINDER SLEEVE ARE REPLACED.
1) Make sure the pressure switch On/Off lever (A) Fig.4 is in the “OFF”
position as shown.
2) Plug the power cord into a grounded 120V branch circuit receptacle.
3) Make sure the oil level in the crankcase reaches the centre dot of the oil
sight glass (A) Fig.5, refer to maintenance section for instructions on
filling the crankcase with oil.
4) Open the drain valve (A) Fig.6, turn it clockwise as shown, this will
prevent air pressure build-up in the tank.
5) Move the pressure switch On/Off lever (A) Fig.4 down to “ON/AUTO”
position. The compressor will start.
6) Run the compressor for 15 minutes. Make sure the drain valve is open
and there is no tank pressure build-up (tank pressure gauge at zero).
7) After 15 minutes, close the drain valve by turning it counterclockwise. The
air receiver will fill tank to cut-out pressure and the motor then will stop.
The air compressor is now ready for use.
FIGURE 3
FIGURE 4
FIGURE 5
FIGURE 6