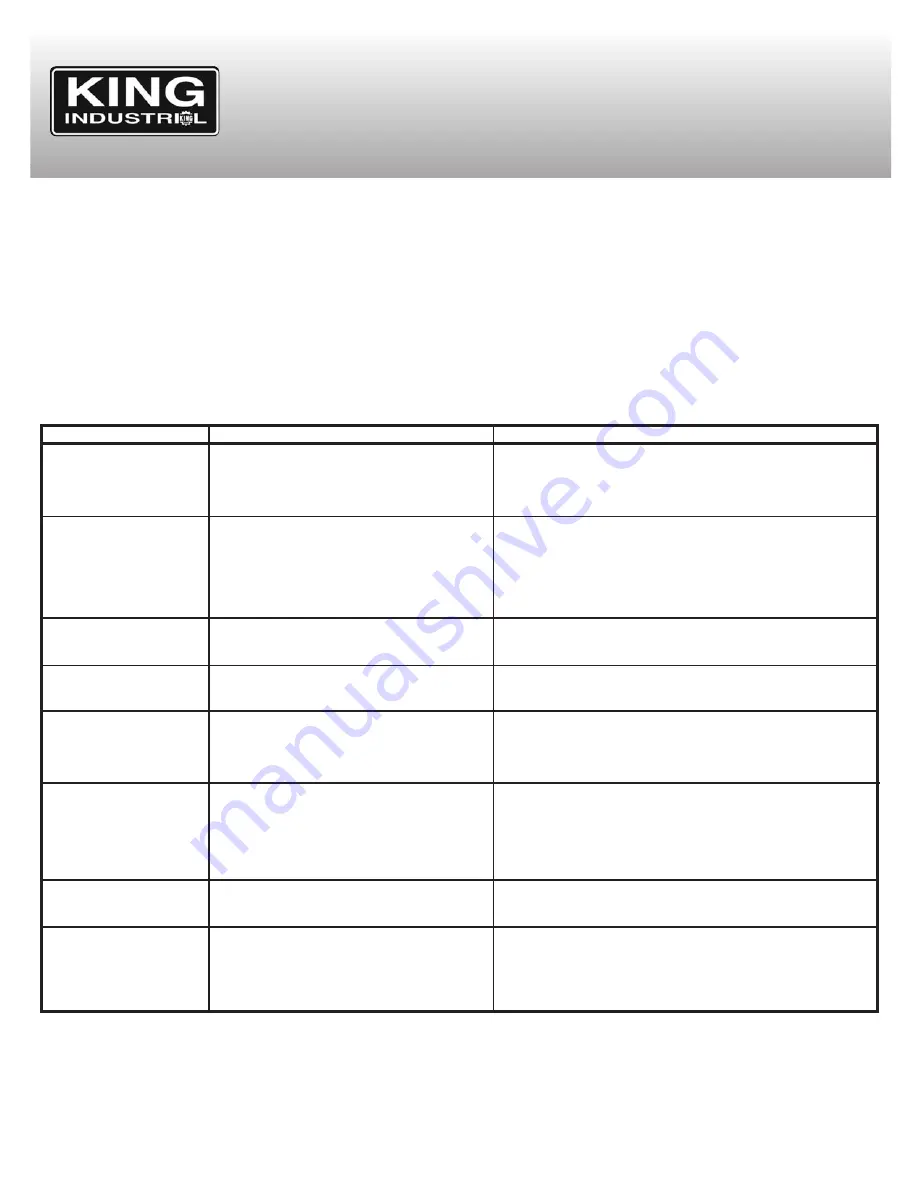
MAINTENANCE / TROUBLESHOOTING
LUBRICATION
All of the ball bearings are packed with grease at the factory. They require no further lubrication. Periodically lubricate the splines
(Grooves) in the spindle and the rack (Teeth of the quill).
WARNING!
For your own safety, turn the switch “OFF” and remove the plug from the power source before maintaining or lubricating
your drill press.
Frequently blow out any dust that may accumulate inside the motor. After operation, remove chips or dirt on the machine and apply a
coat of furniture-type paste wax to the table and the column, this will help keep the surfaces clean and free of rust.
PROBLEM
Noisy operation.
Drill bit burns.
Wood splinters on
underside of workpiece.
Workpiece torn loose
from hand.
Drill bit binds in work-
piece.
Excessive drill bit
wobbling.
Quill returns too fast or
too slow.
Chuck will not stay
attached to the spindle.
It falls off when trying
to install it.
PROBABLE CAUSE
1. Incorrect belt tension.
2. Dry spindle.
3. Loose spindle pulley.
4. Loose motor pulley.
1. Incorrect speed.
2. Chips not coming out of hole.
3. Dull drill bit.
4. Feeding too slow.
5. Not lubricated.
1. No “Back-up material” under the
workpiece.
1. Not supported or clamped properly.
1. Workpiece is pinching the drill bit or
there is an excessive feeding pressure.
2. Improper belt tension.
1. Bent drill bit.
2. Worn spindle bearings.
3. Drill bit is not properly installed in the
chuck.
4. Chuck not properly installed.
1. Spring has improper tension.
1. Dirt, grease or oil on the tapered inside
surface of the chuck or on the spindle
tapered surface.
SOLUTION
1. Adjust the tension.
2. Lubricate the spindle.
3. Tighten the retaining nut on the pulley as needed.
4. Tighten the set screws which hold the pulleys in place.
1. Change the speed.
2. Retract the drill bit frequently to clear the chips.
3. Resharpen the drill bit.
4. Feeding too fast...allow the drill bit to cut.
5. Lubricate the drill bit with cutting or motor oil.
1. Support the workpiece or clamp it.
1. Support the workpiece or clamp it.
1. Support the workpiece or clamp it.
2. Adjust the tension of the belt.
1. Use a straight drill bit.
2. Replace the bearings.
3. Install drill bit properly.
4. Install chuck properly.
1. Adjust the spring tension.
1. Using a household detergent, clean the tapered
surfaces of the chuck and the spindle to remove the
dirt, grease and oil.
PARTS DIAGRAM & PARTS LISTS
Refer to the Parts section of the King Canada web site for the most updated parts diagram and parts list.