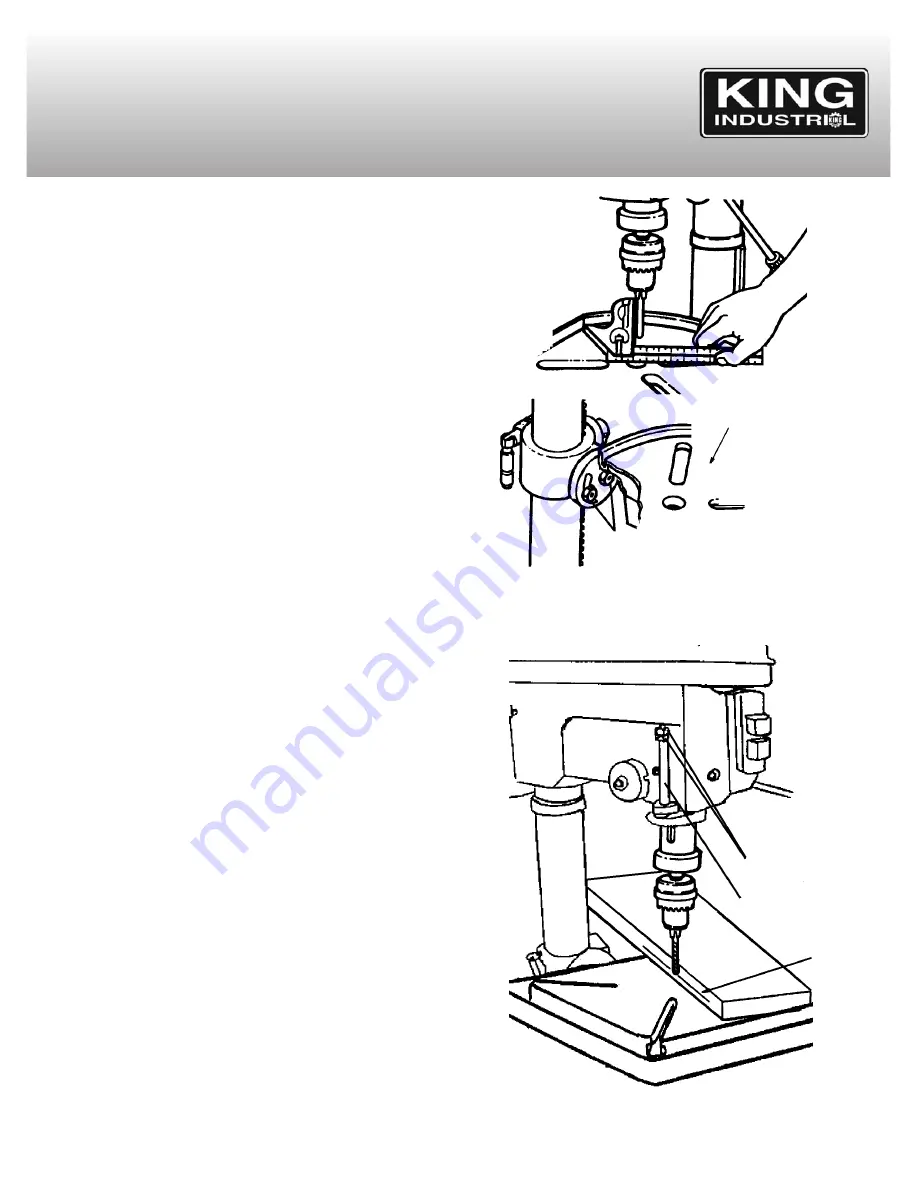
ADJUSTMENTS
ADJUSTING THE TABLE SQUARE TO THE HEAD
NOTE
: The combination square must be “true”.
1. Insert precision round steel rod or straight drill bit approximately 3”
long into the chuck and tighten.
2. With the table raised to work height and locked to the column, place the
combination square flat on the table beside the rod or drill bit.(Fig.19).
3. If an adjustment is necessary, loosen bevel lock nuts under the work
table.
4. Align the table square to the rod or drill bit by pivoting the table until
they are in line.
5. Retighten table bevel lock nuts.
BEVEL SCALE
NOTE
: The bevel scale has been included to provide a quick method for
beveling the table to approximate angles. If precise accuracy is necessary,
a square, or other precision measuring tool should be used to position the
table.
1. To use the bevel scale do the following: a) Loosen the table bevel lock
nuts (See step 3 above for reference). b) Move table so that desired angle
on the bevel scale is straight across from the zero line on the table. c)
Retighten table bevel lock nuts.
DRILLING TO A SPECIFIC DEPTH (Fig.20)
To drill a blind hole (not all the way through) to a given depth, proceed as
follows.
1. Mark the depth of the hole on the workpiece.
2. With the switch OFF, bring the drill bit down until the tip of the lips of
the drill bit are even with the mark.
3. Take note of the depth mesurement on the depth scale.
4. Bring both adjustement nuts down to the noted and desired depth.
5. The drill bit will stop at this depth until the adjustment nuts
are re-adjusted.
FIGURE 19
Table
Table bevel
lock nuts
FIGURE 20
Depth scale
Mark
Adjusting Nuts