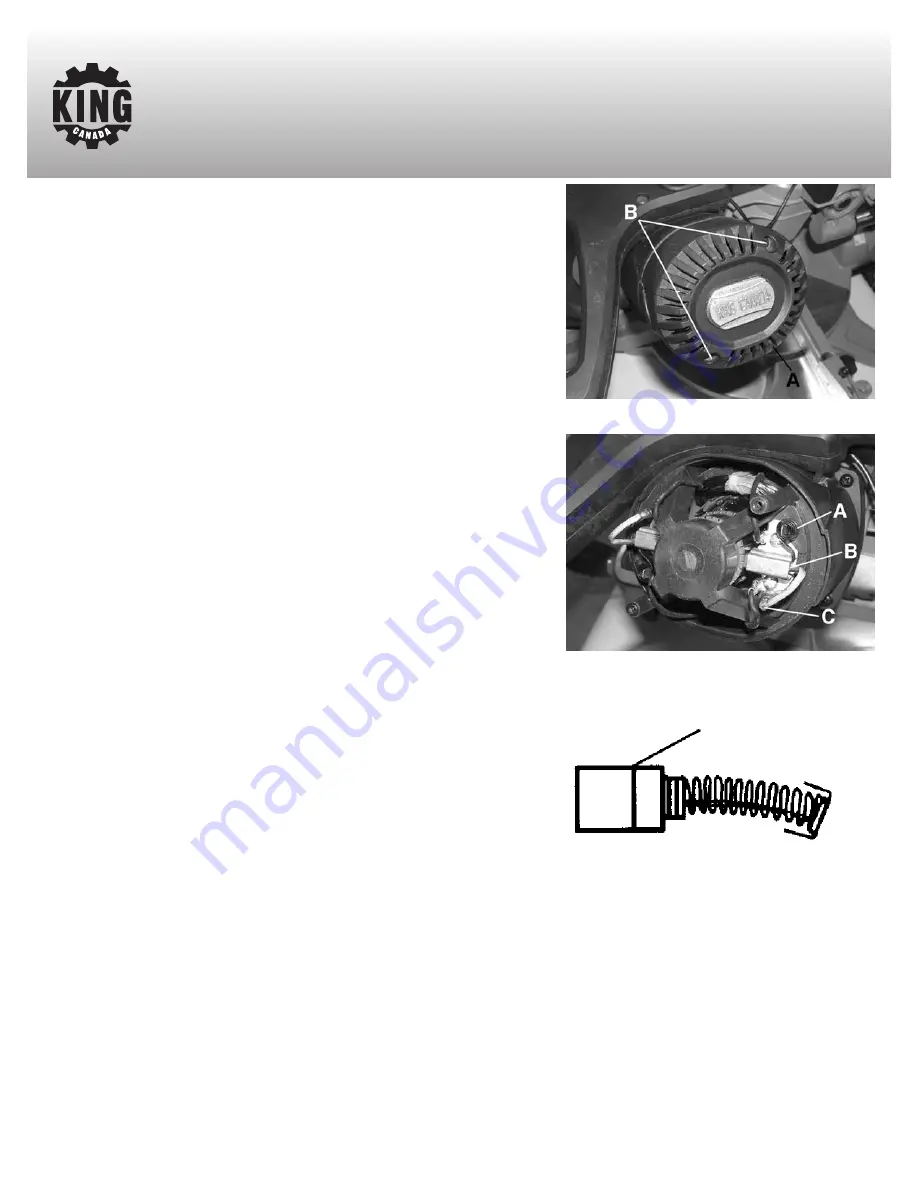
MAINTENANCE
All the ball bearings are sealed and lubricated for life and will require no
maintenance.
Cleaning
• After use, wipe off chips and dust adhering to the tool with cloth or the like.
Keep the blade guards and covers clean . Lubricate the sliding portions with
machine oil to prevent rust.
To maintain product SAFETY and RELIABILITY, repairs, any other
maintenance or adjustment should be performed by your nearest authorized
service center.
REPLACING CARBON BRUSHES
Remove and check the carbon brushes regularly (normally after 50 hours of
use). The carbon brushes are installed inside the motor housing. Using a
screwdriver, remove the 2 pan head screws (B) Fig.21 that hold the motor
housing cap (A) in place.
Once the motor housing cap is removed, to release the carbon brush (B) Fig.22
from the holder, lower the retaining spring (A). Disconnect the carbon brush
wire (C) from the terminal, remove the carbon brush from the motor housing
and inspect it. Repeat this step for the second carbon brush. Carbon brushes
need to be replaced once they wear down to the limit mark, see Fig.23. Keep
the carbon brushes clean and free to slip in the holders.
If they have worn down to the limit mark, purchase a set of identical
replacement carbon brushes (both carbon brushes should be replaced at the
same time). Insert new carbon brushes into the holders, connect them to the
terminals, reposition the retaining spring and reinstall the motor housing cap
using the 2 pan head screws.
Figure 21
Figure 23
Carbon brush limit mark
Figure 22
MAINTENANCE