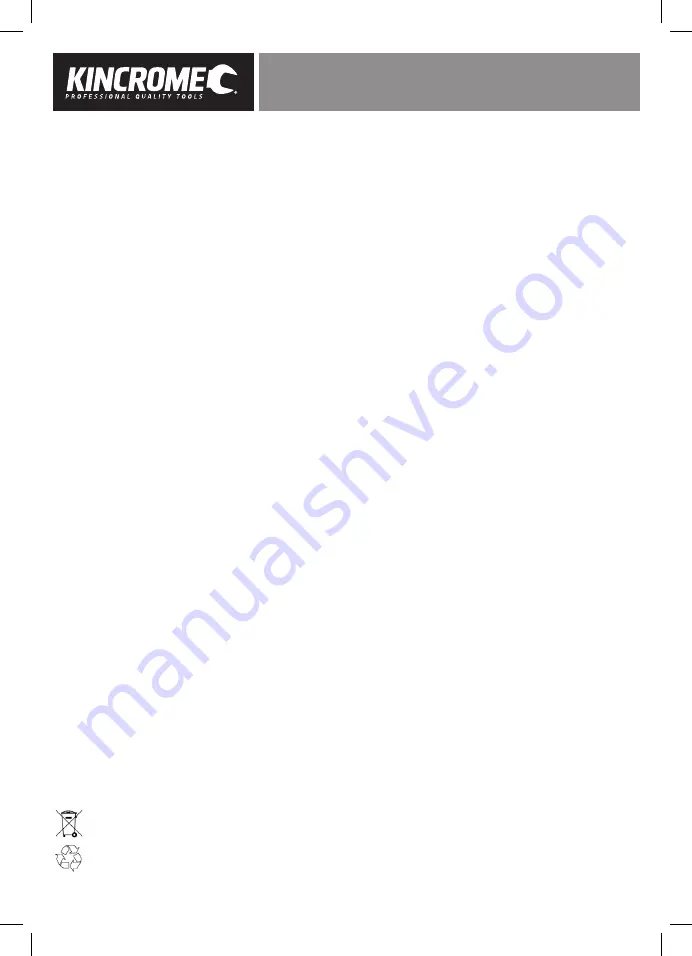
8
HYDRAULIC GARAGE JACKS
Working on Vehicle
Any vehicle being supported by a jack or jack stands creates a potentially hazardous working environment.
Do not move or roll a jack that is supporting a vehicle. Never place any part of your body beneath a vehicle supported by a jack. Be careful
of forces applied to vehicle such as torque on a nut or bolt. These forces could cause vehicle to become unstable on jack stands if they are
not properly placed. Do not turn on the vehicle’s ignition or attempt to start any vehicle supported by a jack or jack stands.
Lowering the Lifting Arm
Caution!:
Make certain that all personnel are clear of the vehicle before lowering. Control the rate of descent of the vehicle at all
times. The more you open the release valve, the faster the vechile descends.
1. Raise vehicle high enough to clear the jack stands, then carefully remove jack stands.
2. Slowly twist the handle assembly counter-clockwise (fig.5) until the jack just begins to lower.
3. Carefully control speed of descending vehicle. Lowering a vehicle too fast can cause property damage or serious injury.
4. After removing the jack from under the vehicle, push down on the lifting arm (7) (fig.8) to reduce the pump ram exposure to rust and contamination.
5. If the vehicle fails to lower:
a) Use another jack to raise the vehicle high enough to reinstall jack stands.
b) Remove the affected jack. Repeat steps 1-4.
Maintenance and Storage
Lubricating
Moving parts on a jack should be lubricated occasionally with a light machine oil to maintain efficient operation. Apply oil to joints on Lift
Arm (7) hinges, push rods, Handle Base (4), Rear Castors (5), Front Rollers (6) (and adding grease via the grease nipple on the Lifting
Arm (fig. 11). Wipe away excess oil and grease with soft cloth.
Maintaining Oil Level
Important Note:
When adding or replacing oil, always use a good grade hydraulic jack fluid. Avoid mixing types of oil. DO NOT use brake fluid, alcohol,
glycerine, detergent, motor oil or dirty oil, Improper fluid can cause serious internal damage to a jack.
Adding Oil:
With Head Cap (1) fully lowered & the Jack on level ground, remove the 4 screws and lift the pump cover (fig 9.)
Remove air vent valve (fig 10). Hydraulic fluid level should be visible at the air vent valve hole approx 12mm below air vent valve hole,
do not overfill. If low, add fluid as needed then close air vent valve.
Replacing Oil:
For better performance & longevity, replace oil supply once a year. To drain oil, open air vent valve and loosen the
release valve by twisting handle assembly counter-clockwise. BE VERY CAREFUL not to permit dirt or foreign matter
to get into the system. Invert the jack over suitable container and allow oil to drain. Close release valve by twisting handle assembly
clockwise, fill with good grade hydraulic jack oil close air vent valve wipe away any spilt fluid. Test the jack before lifting a vehicle.
Cleaning
The jack should be wiped clean with soft cloth only. Do not use gasoline, kerosene, or other such solvents or any abrasive
cleanser as cleaning agents and solvents will cause deterioration of the hydraulic seals.
Storage
Before storage, twist handle assembly 1-1/2 twists counter-clockwise to release pressure in hydraulic cylinder.
Leave handle in this position. Store the jack level, in a clean environment preferably indoors, in a dry area to protect
the jack from moisture.
Repairing the Jack
There are no user serviceable parts except as outlined in the exploded views. Only trained, licensed and certified repair personnel
should attempt any repairs or replacing of parts. Any modifications to this jack, except those performed by the manufacturer, or their
design, will void all warranties both written and implied.
Caring for the environment
When a jack is no longer usable it should not be disposed of with household waste, but in an environmentally friendly way.
Please recycle where facilities exist. Check with your local council authority for recycling advice.
Recycling packaging reduces the need for landfill and raw materials. Reuse of recycled material
decreases pollution in the environment. Please recycle packaging where facilities exist. Check with your local council
authority for recycling advice.