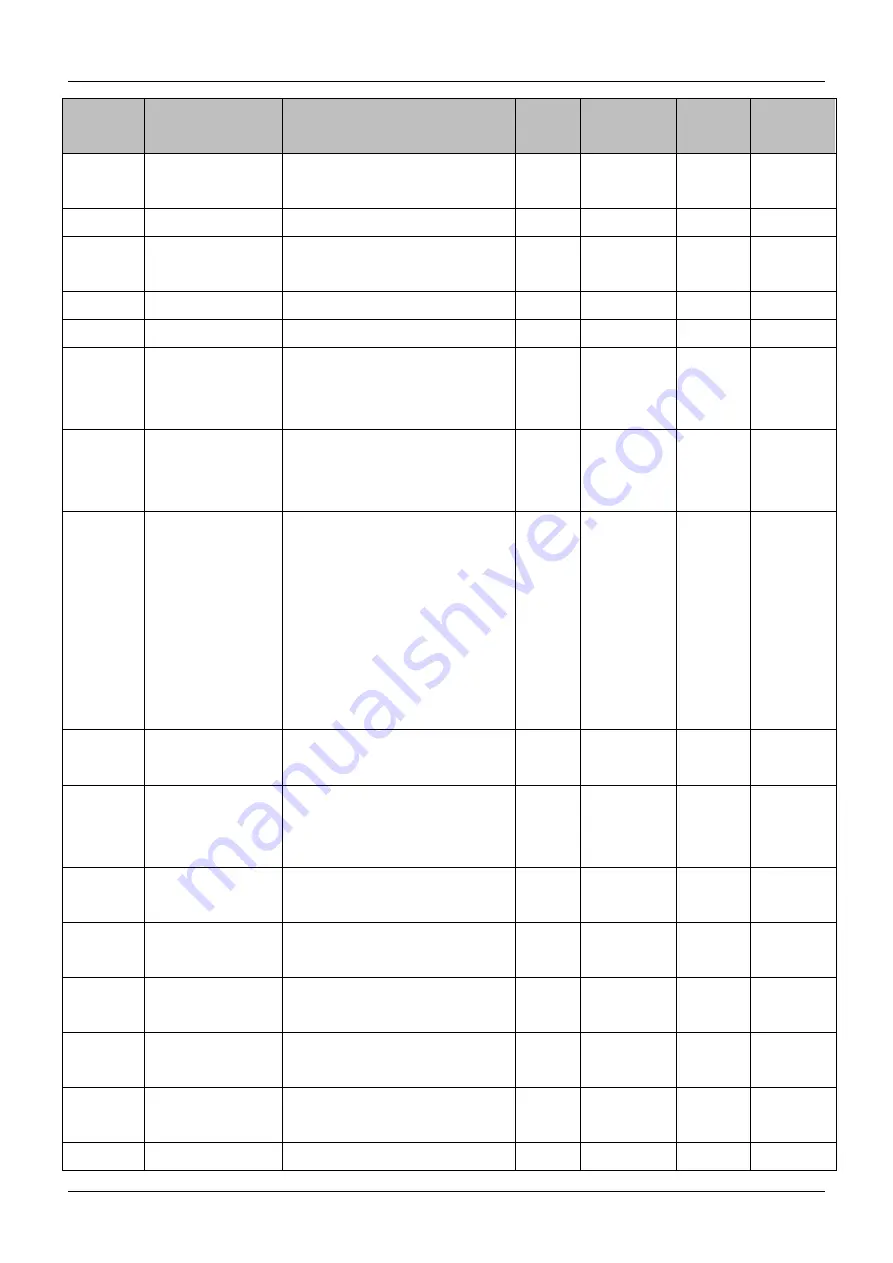
93
Function
code
Name
Descriptions
Unit
Factory
setting
Modif.
Setting
range
C1.09
Proportional gain
KP
0.000~10.000
0.001
2.000
○
0~10000
C1.10
Integral gain Ki
0.000~10.000
0.001
0.100
○
0~10000
C1.11
Differential
gain
Kd
0.000~10.000
0.001
0.100
○
0~10000
C1.12
Sampling cycle T
0.01~50.00s
0.01s
0.50s
○
1~5000
C1.13
Output filter
0.01~10.00s
0.01s
0.05
○
1~1000
C1.14
Error limit
0.0~20.0%
(Corresponding
to
close-loop
reference)
0.1%
2.0%
○
0~200
C1.15
Close-loop
regulation
characteristic
0
:
Positive
1
:
Negative
1
0
×
0~1
C1.16
Integral regulation
selection
0: Stop integral regulation when
the frequency reaches the upper
and lower limits
1:
Continue
the
integral
regulation when the frequency
reaches the upper and lower
limits
1
0
×
0~1
C1.17
Preset close-loop
frequency
0.00~300.00Hz
0.01Hz
0.00Hz
○
0~30000
C1.18
Holding time of
preset close-loop
frequency
0.0~3600.0S
0.1S
0.0S
×
0~36000
C1.19
Preset close-loop
reference 1
-10.00V ~10.00V
0.01V
0.00V
○
0~2000
C1.20
Preset close-loop
reference 2
-10.00V ~10.00V
0.01V
0.00V
○
0~2000
C1.21
Preset close-loop
reference 3
-10.00V ~10.00V
0.01V
0.00V
○
0~2000
C1.22
Preset close-loop
reference 4
-10.00V ~10.00V
0.01V
0.00V
○
0~2000
C1.23
Preset close-loop
reference 5
-10.00V ~10.00V
0.01V
0.00V
○
0~2000
C1.24
Preset close-loop
-10.00V ~10.00V
0.01V
0.00V
○
0~2000