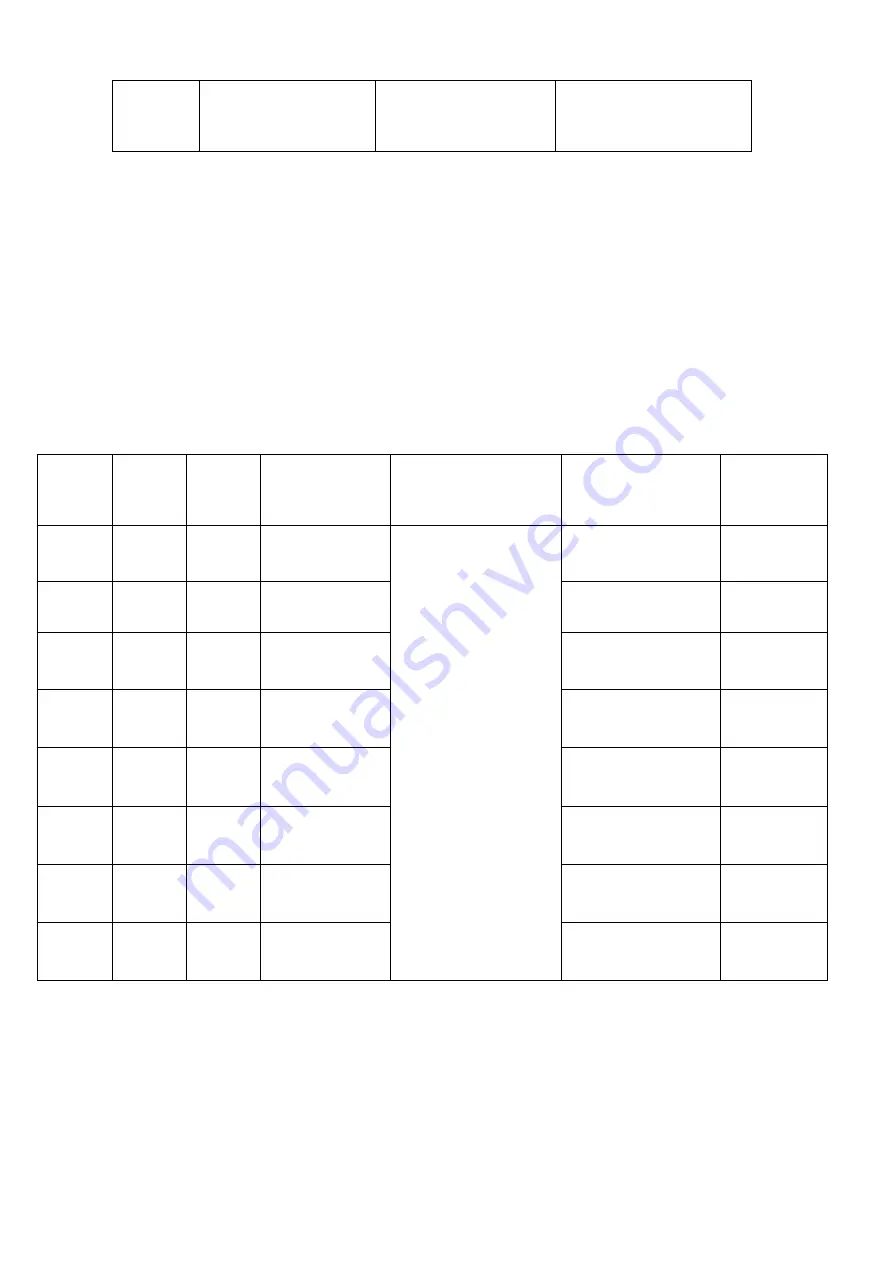
72
10:
Initializing
all
parameters
for
the
control loop
7.4 Internal Multi-
position Control Modes (“1” Mode)
In Internal
Multi-position
control mode, we can activate internal set target position though an external signal to
control motors. The activation has two preconditions:
1,
Multi-position
control mode can only be activated in Mode 1, it can’t be activated in other modes.
2,
At least one of the external input signal is defined as ―Internal position control 0‖, ―Internal position control 1
― or ―Internal position control 2 ―, which means at least one address of digital tubes-d3.01 ~ d3.07 is set to
―040.0‖’, ―080.0‖ or ―800.2.
―Internal position control 0‖ , ―Internal position control 1‖ and ―Internal position control 2 ―, these three
signals will be combined into binary co
des used to select a target position between ―Position 0~7‖.
Table 7-20 Internal Multi-position Control Mode Parameter Table
Note: In this control mode, ―position section X‖ can be positive or negative, it can be flexibly set; while the
corresponding speed must be positive. Other parameters such as acceleration, deceleration, etc, can use the
default value; also can be changed through digital tube.
Internal
position
0
Internal
position
1
Internal
position
2
Corresponding
position
P
osition section
numberic display
Corresponding
speed
Numberic
display
0
0
0
Din_Pos0
d3.40select position
section
sequence
number
d3.41select position
section high bit
d3.42select position
section low bit
Din_Speed0_RPM
d3.18
0
0
1
Din_Pos1
Din_Speed1_RPM
d3.19
0
1
0
Din_Pos2
Din_Speed2_RPM
d3.20
0
1
1
Din_Pos3
Din_Speed3_RPM
d3.21
1
0
0
Din_Pos4
Din_Speed4_RPM
d3.44
1
0
1
Din_Pos5
Din_Speed5_RPM
d3.45
1
1
0
Din_Pos6
Din_Speed6_RPM
d3.46
1
1
1
Din_Pos7
Din_Speed7_RPM
d3.47
Summary of Contents for CD2S Series
Page 7: ...7...
Page 8: ...8 1 3 3 Power Brake and Encoder cable of Motors...
Page 12: ...12 Fig 2 3 Installation direction...
Page 15: ...15 3 1 2 Wiring Diagram Fig 3 1 Wiring diagram of CD2S driver...
Page 23: ...23 Fig 4 3 Separate regulation of bits...
Page 82: ...82...
Page 96: ...96 8 4 Debugging example 8 4 1 Oscilloscope 1 Enter oscilloscope 2 Parameters for Oscilloscope...
Page 98: ...98 In Auto Reverse mode Kvp 110...
Page 100: ...100 The oscilloscope is as following max following error is 69 inc Fig 2 Kpp 30 Vff 100...
Page 101: ...101 The oscilloscope is as following max following error is 53 inc Fig 3 Kpp 30 Vff 50...
Page 102: ...102 The oscilloscope is as following max following error is 230 inc...