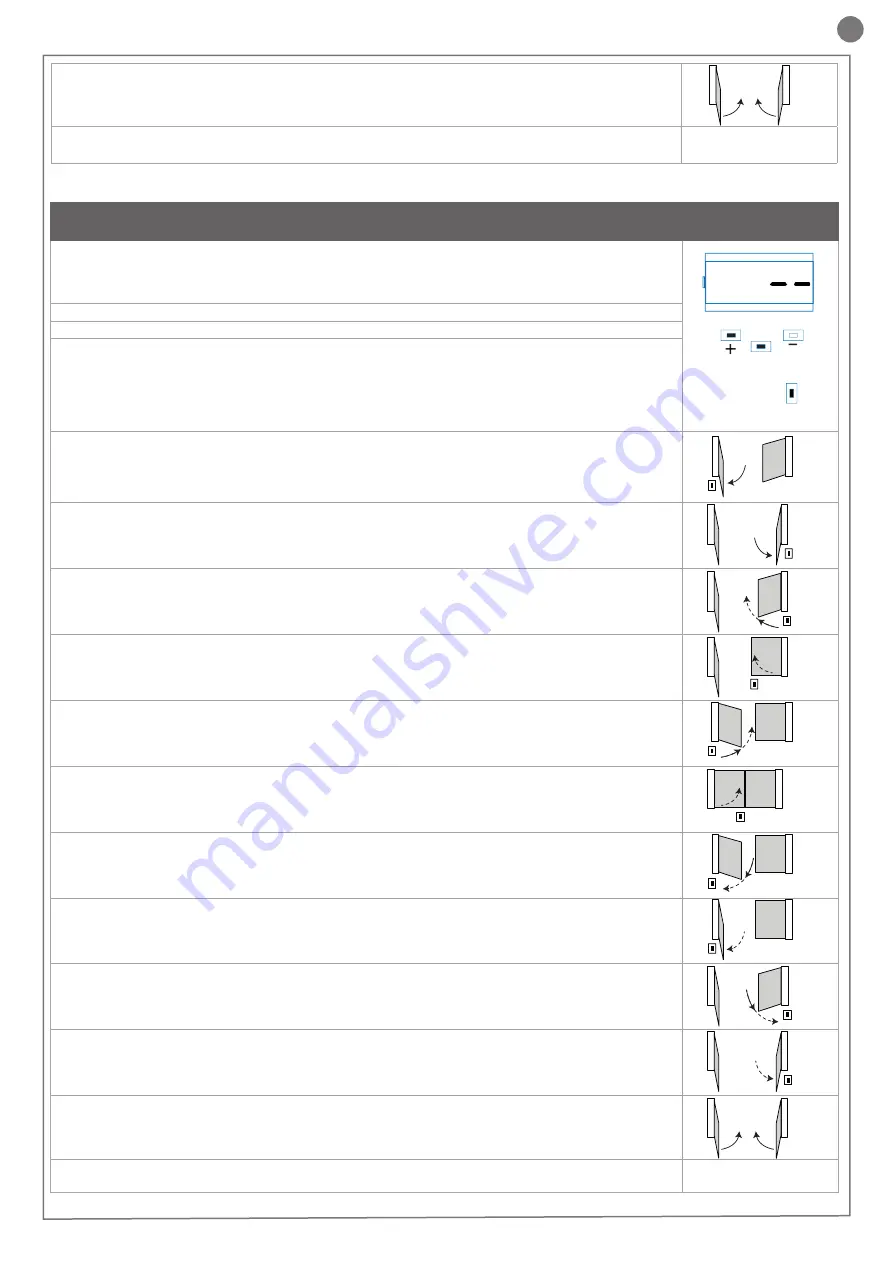
21
EN
UP
SS
DOWN
MENU
AUTOLEARNING OF THE TRAVEL STROKE AND MAIN PARAMETERS, WITH
CUSTOMISED DECELERATIONS
Deceleration intervals can be personalised by the user, according to the procedure below.
1.
CAUTION! check that mechanical end stops (compulsory) are present and secure. The motors must
always reach the mechanical end stop
2. Move the gate manually to mid-travel.
3.
CAUTION: enter the main menu to set the parameter
LSI
=
p
as per the table in paragraph 4.4
4. Press the pushbuttons UP + and MENU at the same time for at least 5 seconds until
LOP
is displayed, then
(if necessary) press DOWN (see figure).
Ensure that motor M1 opens first; otherwise, press DOWN -, turn the power off and invert connections M1 and
M2. Repeat the procedure from step 4.
If the first manoeuvre is NOT opening, press DOWN - to stop the self-learning process. Then press SS to
restart acquisition: the leaf resumes movement in the correct direction.
5. Motor M1 opens at low speed until it reaches the mechanical opening end stop.
At precisely the time of reaching the mechanical opening end stop, press the SS command.
Motor M2 starts automatically in opening mode. If motor M2 moves in closing, stop by pressing DOWN - and
resume movement using SS (the leaf resumes movement in the correct direction)
6. Motor M2 opens at low speed.
At precisely the time of reaching the mechanical opening end stop
.
After a couple of seconds, motor M2 starts automatically in closing at full speed.
7.
On reaching the point where motor M2 closing deceleration is required, press SS
. M2 motor move-
ment continues at low speed.
8.
Precisely when motor M2 reaches the closed position, press the SS command
. Motor M2 stops and
motor M1 starts in closing.
9.
On reaching the point where motor M1 closing deceleration is required, press SS
. M1 motor move-
ment continues at low speed.
10.
Precisely when motor M1 reaches the closed position, press the SS command
. Motor M1 stops and
restarts in opening.
11.
On reaching the point where motor M1 opening deceleration is required, press SS
. M1 motor move-
ment continues at low speed.
12.
Precisely when motor M1 reaches the open position, press the SS command
. Motor M1 stops and
motor M2 starts in opening.
13.
On reaching the point where motor M2 opening deceleration is required, press SS
. M2 motor move-
ment continues at low speed.
14.
Precisely when motor M2 reaches the open position, press the SS command
. Motor M2 stops.
15. M1 and M2 resume closing according to the offset parameter entered in the menu, i.e. the gate closes
automatically according to the set travel.
16. Run a number of opening, closing and stop manoeuvres, to check that the system is stable and there are
no assembly defects.
All main parameters are configured as default by the control unit. To personalise installation, go to the next step in paragraph 4.4.
10. Motors M1 and M2 resume closing according to the leaf offset values set in the menu, i.e. the gate closes
automatically according to the set travel.
11. Run a number of opening, closing and stop manoeuvres, to check that the system is stable and there are
no assembly defects.
All main parameters are configured as default by the control unit. To
personalise installation, go to the next step in paragraph 4.4. If torque
is not sufficient to move the leaf, delete the deceleration intervals from
the menu [
LSI
=0].
10
M1
M2
15
M1
M2
5
M1
M2
SS
6
M1
M2
SS
7
M1
M2
SS
8
M1
M2
SS
9
M1
M2
SS
10
M2
SS
M1
11
M1
M2
SS
12
M1
M2
SS
13
M1
M2
SS
14
M1
M2
SS