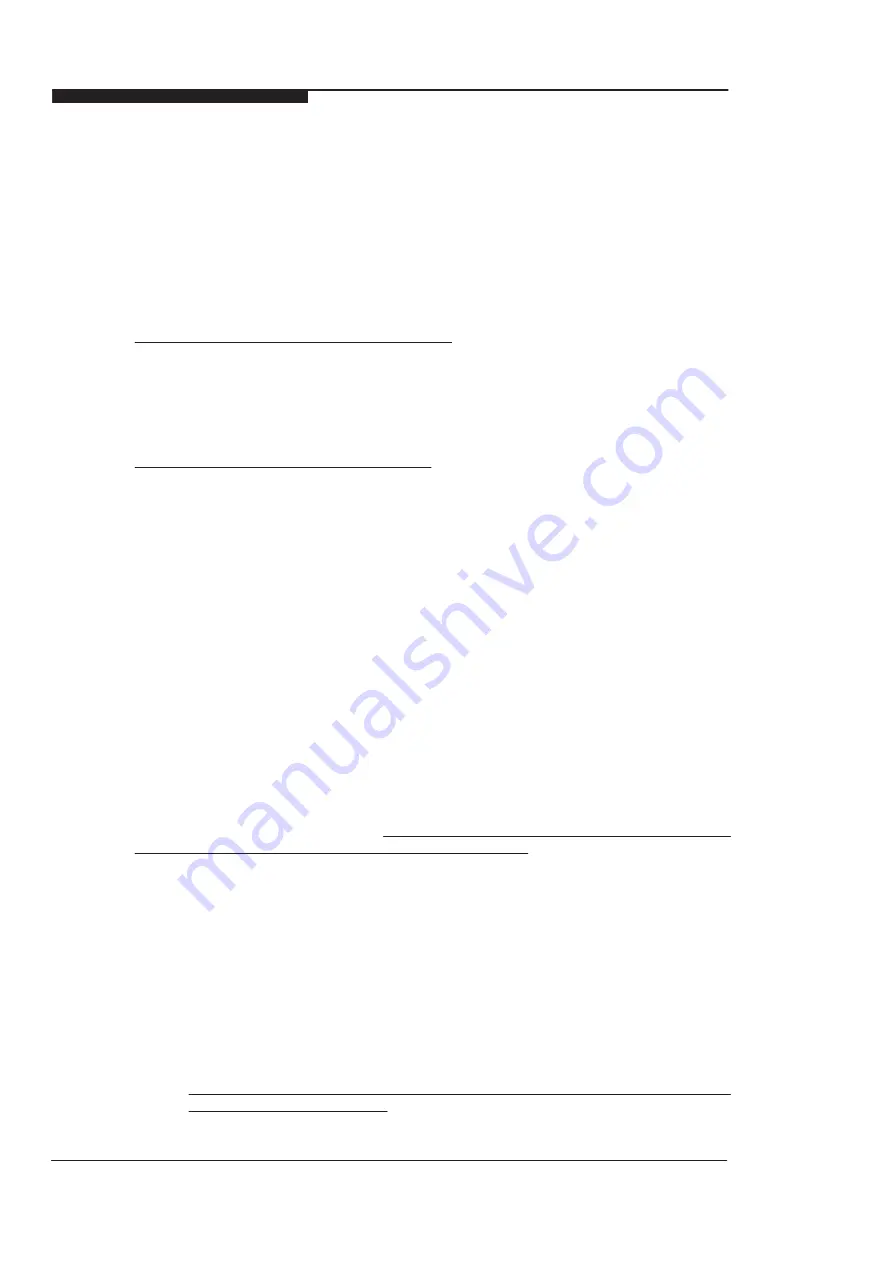
iii)
replace the nut from the frame bottom
Connect the condensate drainage system to the boiler. It is advisable to use a detachable
fitting at connection to the boiler to enable easy removal for servicing.
Fill the condensate trap by pouring water into the boiler flue until water is seen to flow
freely from the condensate drainage system. Make the final connection of flue pipe to the
boiler.
Details are provided in Chapter 3 - Section 3.11 Condensate Drainage
Connection :
22 mm plastic pipe.
4.6
WATER SYSTEM
Installation Without Optional Pre-Installation Jig:
Connect the flow and return HEATING CIRCUIT system pipework to the boiler. Details of
system requirements are given in Chapter 3 - Section 3.7 Water Systems.
Connections
: 0.75 BSPM
Connect the flow and return DOMESTIC WATER pipework to the boiler. Details of system
requirements are given in Chapter 3 - Section 3.7 Water Systems.
Connections
: 0.5 BSPM
Installation With Optional Pre-Installation Jig:
Connect the flow and return HEATING CIRCUIT system pipework to the boiler jig valves.
Details of system requirements are given in Chapter 3 - Section 3.7 Water Systems.
Connections
: 22mm compression
Connect the flow and return DOMESTIC WATER pipework to the boiler jig valves. Details
of system
requirements are given in Chapter 3 - Section 3.7 Water Systems.
Connections
: 15mm compression
For optimum performance after installation, this boiler and its associated central heating
system must be flushed in accordance with the guidelines given in BS7592:1992,
"Treatment of water in domestic hot water central heating systems".
This must involve the use of a proprietary cleaner, such as Fernox Superfloc, or
BetzDearborn's Sentinel X300 or X400. Full instructions are supplied with the products,
but for immediate information, please contact Fernox on 01799 550811 or BetzDearborn
on 0151 420 9563.
For long term protection against corrosion and scale, after flushing, it is recommended
that an inhibitor such a Fernox MB1 or BetzDearborn's Sentinel X100 is dosed in
accordance with the guidelines given in BS7593:1992.
4.7
GAS SUPPLY
Connect the gas supply to the appliance. Details of gas supply requirements are given in
Chapter 3 - Section 3.6 Gas Supply. Supply of adequate gas pressure
(with the boiler
running)
is critical to ensure reliable operation of the boiler.
Connections
: 15mm compression
4.8
ELECTRICAL SUPPLY
The entry point(s) for the electrical supply cable(s) is in the base of the appliance (see
Section 3.2 Service Connections fig. 3.1.2) via a cordgrip bush. Feed the cable through
the bush and route inside the cabinet to the connection strip located to the front bottom
right area of the cabinet.
1.
The electrical supply must be as specified in Chapter 3 - Section 3.4 Electrical
Supply.
WARNING :
THIS APPLIANCE MUST BE EARTHED.
2.
All external controls and wiring must be suitable for mains voltage. Supply wiring
should be in PVC insulated cable not less than 0.75mm
2
(8.0mm dia) to BS 6500
Table 16 (material code H05VV-F).
3.
The permanent live supply connection may be via a 3 amp fused double pole
switch, serving only the boiler. (Refer to Chapter 3 - Section 3.4 Electrical Supply).
The system controls for the boiler must also be supplied via this isolator.
WD388/0/2004
Chapter 4 : Installation
The Keston C36 Combi & C36P Combi Boilers
Installation & Servicing Instructions
Page : 22