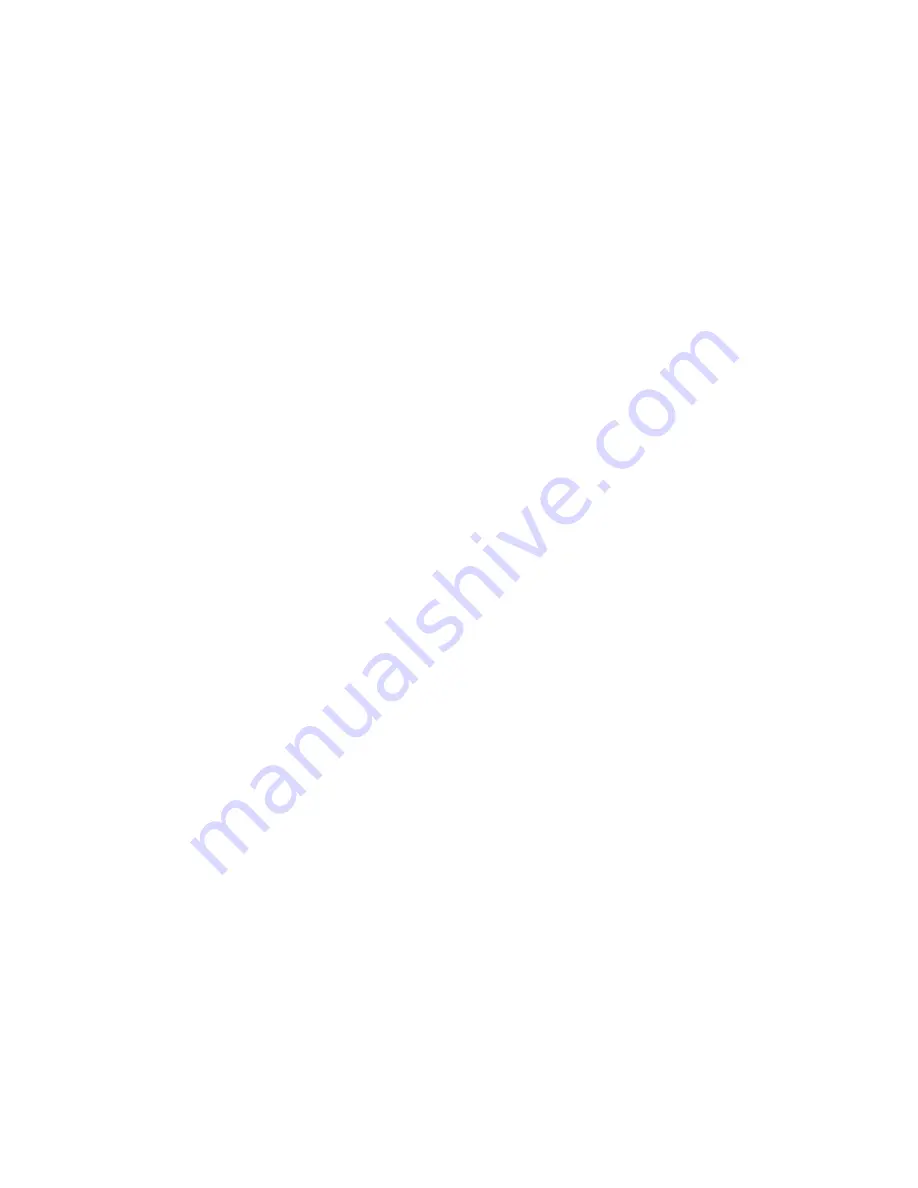
K4C COMPACT-MULTI – INSTALLATION/OPERATION MANUAL
K4C Compact-multi
Feb
-06
15
Using too much oil
Oil leak in line or tank
Check fittings for tightness. Inspect tank and replace
if necessary.
Draft regulator set high
Adjust regulator for -0.04” wc draft pressure at
breech.
Nozzle too large
Replace nozzle to lower input.
Burner reset cuts out
No oil
Call oil supplier.
Frozen oil line
Call technician or oil supplier.
Dirty oil filter
Replace filter.
Dirty nozzle, smoky fire
Replace nozzle, adjust burner air.
Faulty oil pump
Have pump replaced, adjust burner air.
Faulty or dirty electrodes
Have technician clean or replace.
Warm air register blowing cold air
Basement cooling ducts
Insulate and seal ductwork to maintain duct
temperature.
Ducts running through
Change or insulate ductwork.
unheated spaces
Low speed switch is on
Switch off blower low speed.
“FAN OFF” set low
Fan control – Set “FAN OFF” higher.
Motor speed set too high
Reset motor speed to slow blower.
Warm air registers blowing too hot
Blower running slow
Speed blower up.
Return air restricted
Open up return air ductwork to ensure adequate air
flow.
Nozzle too large
Lower nozzle size to suit ductwork.
All rooms at different temperatures
Supply air not regulated
Adjust warm air regulators to suit each room.
Return air not regulated
Check for sufficient return air.
Noisy operation
Loose blower wheel
Tighten wheel set screw or replace.
Blower wheel hitting housing
Center wheel in housing.
Damaged motor bearings
Replace blower motor.
Faulty oil pump
Repair or replace oil pump. Reset to correct
pressure.
Air leak in oil line
Tighten all connections.
Vacuum too high on pump
Check pump vacuum. Check filters and pump
screen.