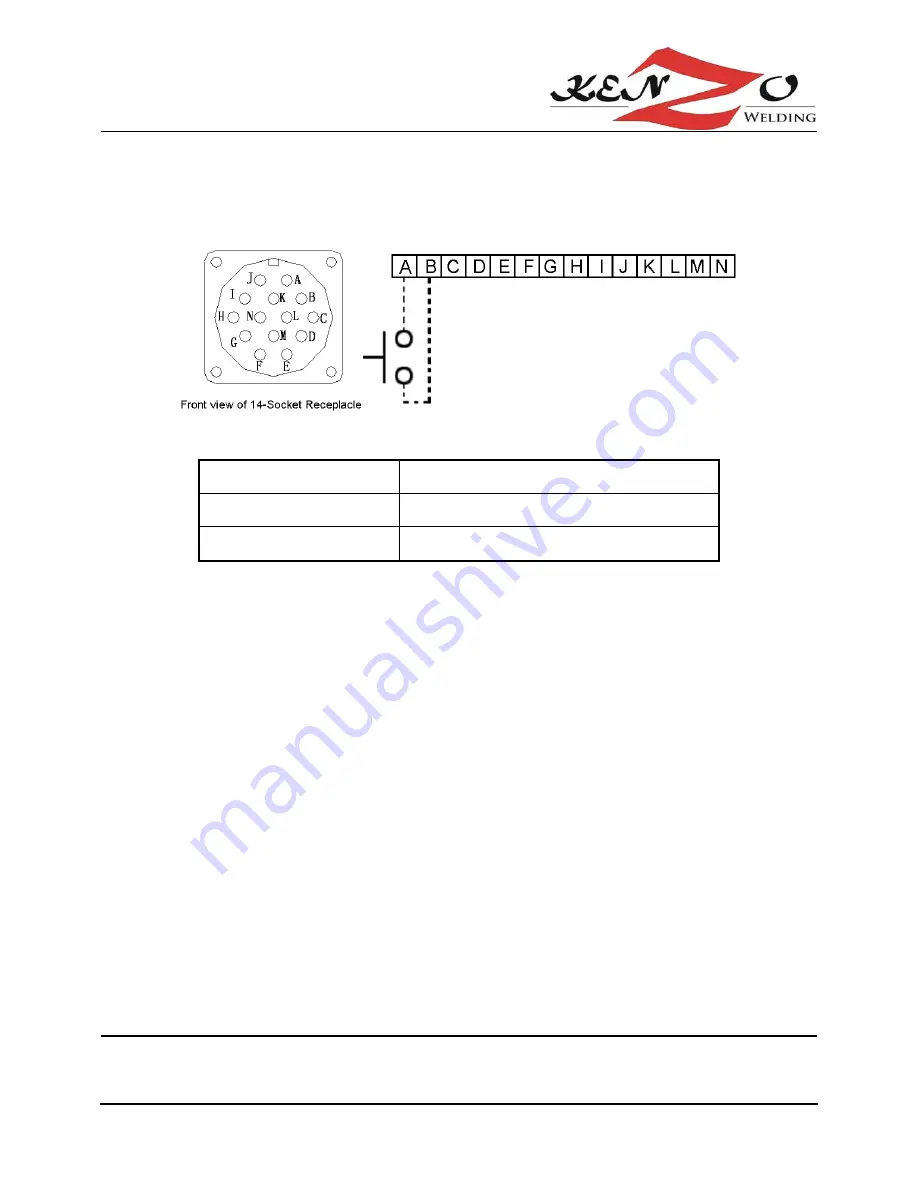
- 12 -
PLASMA 100 Operating Manual
17. Input Gas Fitting
18. Ground Screw
19. Input Power Cable Port
20. Fuse
Figure 3
Pin Function
A
Cutting torch switch
B
Cutting torch switch
Table 4
WARNING
When the cutter is connected to the primary supply voltage, the internal electrical components
maybe at primary potential with respect to earth.