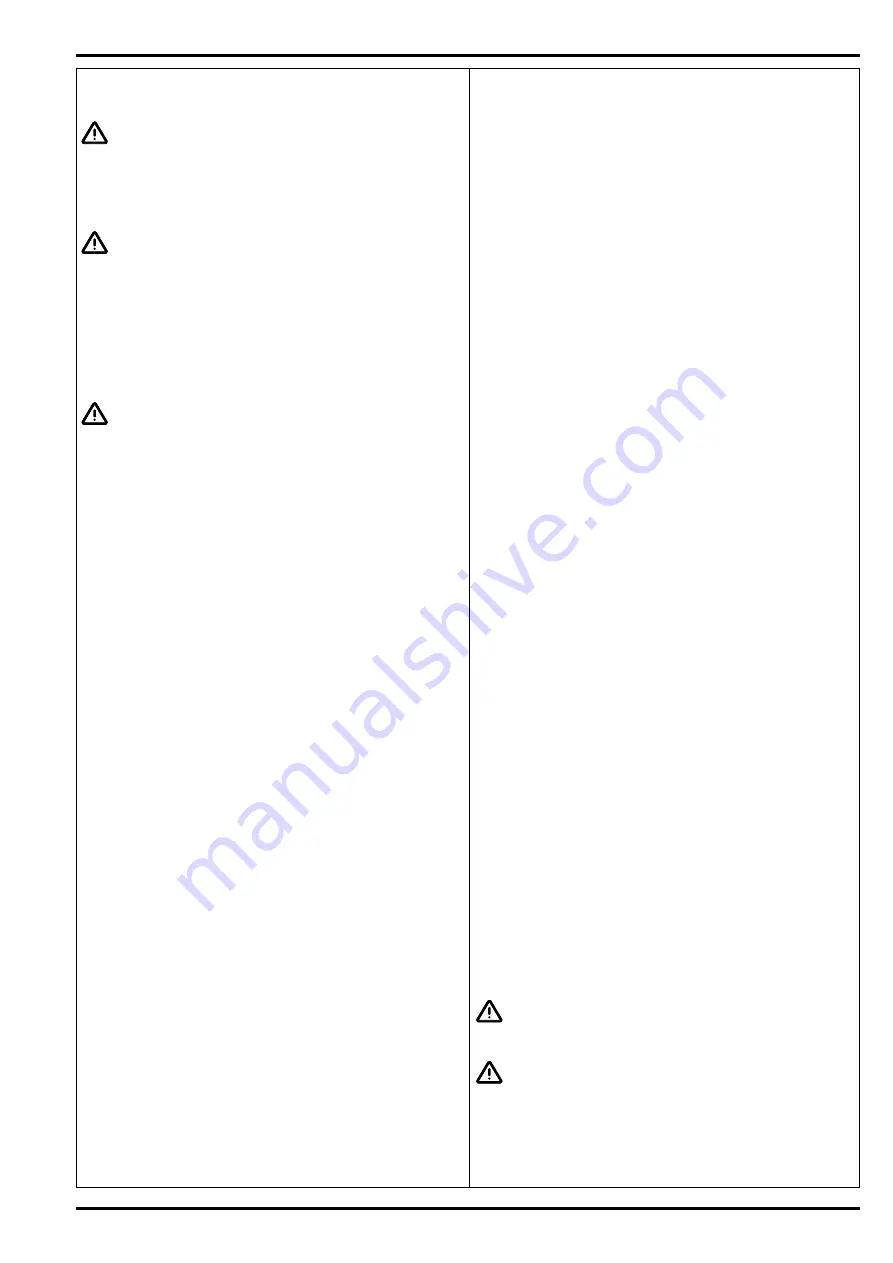
FORM NO. 56041536 - SelectGloss
™
21PH, 21PK, 27PK, 27PO, 27PR - 7
77
77
MAINTENANCE
MAINTENANCE
MAINTENANCE
MAINTENANCE
MAINTENANCE
W
W
W
W
WARNING!
ARNING!
ARNING!
ARNING!
ARNING!
Before attempting any maintenance procedures on ma-
chine, stop on level surface, shut off machine and turn off
LPG valve at tank.
A
A
A
A
ATTENTION!
TTENTION!
TTENTION!
TTENTION!
TTENTION!
Repairs and adjustments must be performed by authorized
and trained personnel.
To keep machine in good working condition, simply follow the daily,
weekly, and monthly maintenance procedures.
NOTE:
NOTE:
NOTE:
NOTE:
NOTE: Always record maintenance and service.
A
A
A
A
ATTENTION!
TTENTION!
TTENTION!
TTENTION!
TTENTION!
Always keep machine free from dust and lint; the engine is
air cooled and for proper air flow to cool the engine, the
recoil filter must remain clean.
DAILY MAINTENANCE (Every 4 Hours of Operation)
DAILY MAINTENANCE (Every 4 Hours of Operation)
DAILY MAINTENANCE (Every 4 Hours of Operation)
DAILY MAINTENANCE (Every 4 Hours of Operation)
DAILY MAINTENANCE (Every 4 Hours of Operation)
1
Check oil level (Use 10W30 oil only).
2
Clean recoil filter .
3
Check belt tension by pinching belt together. Belt should only
depress 1/2" (13mm).
4
Clean all air filters by blowing out dust and dirt and/or washing
the foam filters (recoil and carburetor pre- filter) with warm,
sudsy water and rinsing clean.
(Be careful not to wet the paper
carburetor filters.) Be sure filters are clean and dry before use.
Do not oil foam or filter .
5
Make sure all components are secure and tight.
6
Check pad daily (clean or replace).
7
Clean machine.
8
For Dust Control models, clean dust collection bag.
WEEKLY MAINTENANCE (Every 20 Hours of Operation)
WEEKLY MAINTENANCE (Every 20 Hours of Operation)
WEEKLY MAINTENANCE (Every 20 Hours of Operation)
WEEKLY MAINTENANCE (Every 20 Hours of Operation)
WEEKLY MAINTENANCE (Every 20 Hours of Operation)
1
Check oil level. Change oil and filters at 50 hours of operation. Use
10W30 Motor Oil or other no ash motor oils designed for use in
propane engines. Use of non-recommended oil may void the
engine warranty.
See Engine Owners Manual for complete servicing details
2
Inspect carburetor air filter by removing wing nut and over on top
of carburetor. Replace if dry or deposits are present.
3
Check belt for tension. Tighten if loose. If worn, replace with
proper belt.
(See “ADJUSTING BELT TENSION”). Refer to parts
schematic for size of belt required.
4
Inspect and tighten nuts and bolts on engine and frame.
5
Examine all propane hoses and connections for leaks or wear.
Replace if necessary.
6
Grease wheels. Use white lithium grease only and use no more
than 1 pump of grease. More grease than recommended will
push seal and dust cover out, allowing dust and other foreign
materials into the bearings, shortening the life of the wheel
significantly.
MONTHLY MAINTENANCE (Every 80 hours of Operation)
MONTHLY MAINTENANCE (Every 80 hours of Operation)
MONTHLY MAINTENANCE (Every 80 hours of Operation)
MONTHLY MAINTENANCE (Every 80 hours of Operation)
MONTHLY MAINTENANCE (Every 80 hours of Operation)
1
Perform all daily and weekly services.
2
Torque the head bolts when engine is cold in a crisscross
pattern as per engine manufacturers specifications
(See En-
gine Owners Manual).
3
Check valve clearance with cold engine as per engine manufac-
turers specifications
(See Engine Owners Manual).
4
Torque valve cover as per engine manufacturers specifications
(See Engine Owners Manual).
5
Inspect spark plug. Replace if necessary.
6
Change oil and oil filter.
7
Inspect fuel hoses for leak (repair as needed).
8
Wash undercarriage of machine to remove all dust and debris.
9
To ensure proper ventilation, remove engine cover and clean
engine.
10
Replace air filter element and foam filter.
QUARTERLY MAINTENANCE (Every 250 Hours of Operation)
QUARTERLY MAINTENANCE (Every 250 Hours of Operation)
QUARTERLY MAINTENANCE (Every 250 Hours of Operation)
QUARTERLY MAINTENANCE (Every 250 Hours of Operation)
QUARTERLY MAINTENANCE (Every 250 Hours of Operation)
1
Perform all of the above maintenance procedures and have
engine checked by an Authorized Service Center.
2
Check air gap in electronic ignition coil.
3
Check valves with engine cold.
NOTE:
NOTE:
NOTE:
NOTE:
NOTE: Consult Engine Manual for complete servicing and adjustments
information.
LIFE OF MACHINE
LIFE OF MACHINE
LIFE OF MACHINE
LIFE OF MACHINE
LIFE OF MACHINE
1
Change oil regularly.
2
Clean recoil filter regularly.
3
Clean carburetor filter regularly.
4
Keep machine clean from dust and debris.
FUELSYSTEM
FUELSYSTEM
FUELSYSTEM
FUELSYSTEM
FUELSYSTEM
Adjustments for the air/fuel mixture must be made only by an Authorized
Service Center. Improper adjustments can cause high levels of carbon
monoxide emissions which may cause carbon monoxide poisoning or
it can lead to engine damage.
•
Idle speed is adjusting by turning adjustment screw on regula-
tor.
•
Fuel flow is adjusted by adjustment screw on carburetor spud-
in.
CHANGING THE OIL
CHANGING THE OIL
CHANGING THE OIL
CHANGING THE OIL
CHANGING THE OIL
The manufacturer recommendations 10W30 oil.
1
Run engine for five minutes to warm oil.
2
Make sure machine is on level surface. Locate oil drain plug on
rear of engine beside oil cap and remove by turning counter-
clockwise with wrench.
3
Allow oil to run into pan under machine. Allow to completely
drain.
4
Install drain plug and tighten drain plug by turning clockwise
with wrench.
5
Slowly add one quart (946.3 mi) of 10W30 Motor Oil. Then check
oil level with dip stick in oil fill cap. Add additional oil if neces-
sary.
6
Replace oil-fill cap assembly. Hand tighten only.
A
A
A
A
ATTENTION!
TTENTION!
TTENTION!
TTENTION!
TTENTION!
Do not overfill and never run engine low on oil.
A
A
A
A
ATTENTION!
TTENTION!
TTENTION!
TTENTION!
TTENTION!
When checking oil, be sure cap is fully screwed out and
free. Do not check oil by screwing cap in and then out again,
this will give you a false reading.
Summary of Contents for SelectGloss 21PH
Page 32: ......