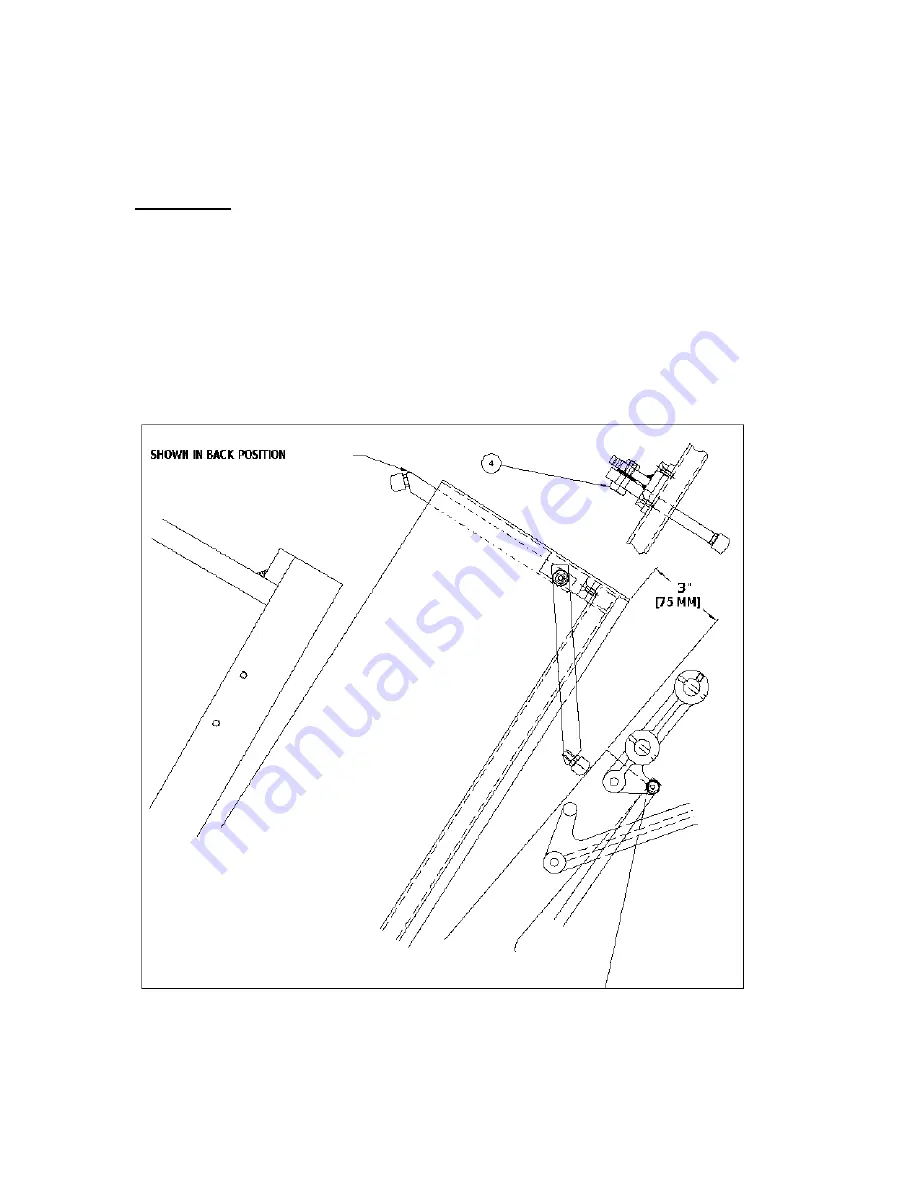
Page
16. Develop a sense of personal safety awareness. Observe all safety regulations. Be on the lookout for hazardous conditions
and discuss control of them with your supervisor.
17. Always follow all operating procedures outlined in ANSI B65.5-1996
Safety Test Trip
The auxiliary safety test trip is a device to measure the acceptable distance between the platen and the die mounting
surface after the wrap around safety device is actuated. The test trip is installed by slipping the trip over the bolts, shown in the
assembly drawing. When the platen is cycled, the test trip contacts the top surface of the platen, causing the tripped wrap around
safety device to stop the press. To run the test, the press should be operating at its highest speed, to ensure that the requirement
for the minimum remaining distance is met at
all
operating speeds. After the platen strikes the removable test trip, the remaining
distance should be no less than 100mm between the platen and the die-mounting surface.
The 1996 safety standard states that
operators MUST run this test before regular operation every day to guarantee the proper working condition of the safety
device and braking system.
Return the safety test trip to back position after successful completion of the test for normal
operation of the machine. Below is a diagram of the proper test procedure.
Instruction Manual - 19" x 25"
Summary of Contents for VALUE LINE
Page 23: ...Page Instruction Manual 19 x 25 ...
Page 25: ... 25 25 Instruction Manual 19 x 25 ...
Page 27: ... 27 27 Instruction Manual 19 x 25 ...
Page 29: ... 29 29 Instruction Manual 19 x 25 ...
Page 31: ... 31 31 Instruction Manual 19 x 25 ...
Page 33: ...Page Instruction Manual 19 x 25 ...
Page 35: ... 35 35 Instruction Manual 19 x 25 ...
Page 37: ... 37 37 Instruction Manual 19 x 25 ...
Page 39: ...Page Instruction Manual 19 x 25 ...
Page 41: ...Page Instruction Manual 19 x 25 ...
Page 43: ... 43 43 Instruction Manual 19 x 25 ...