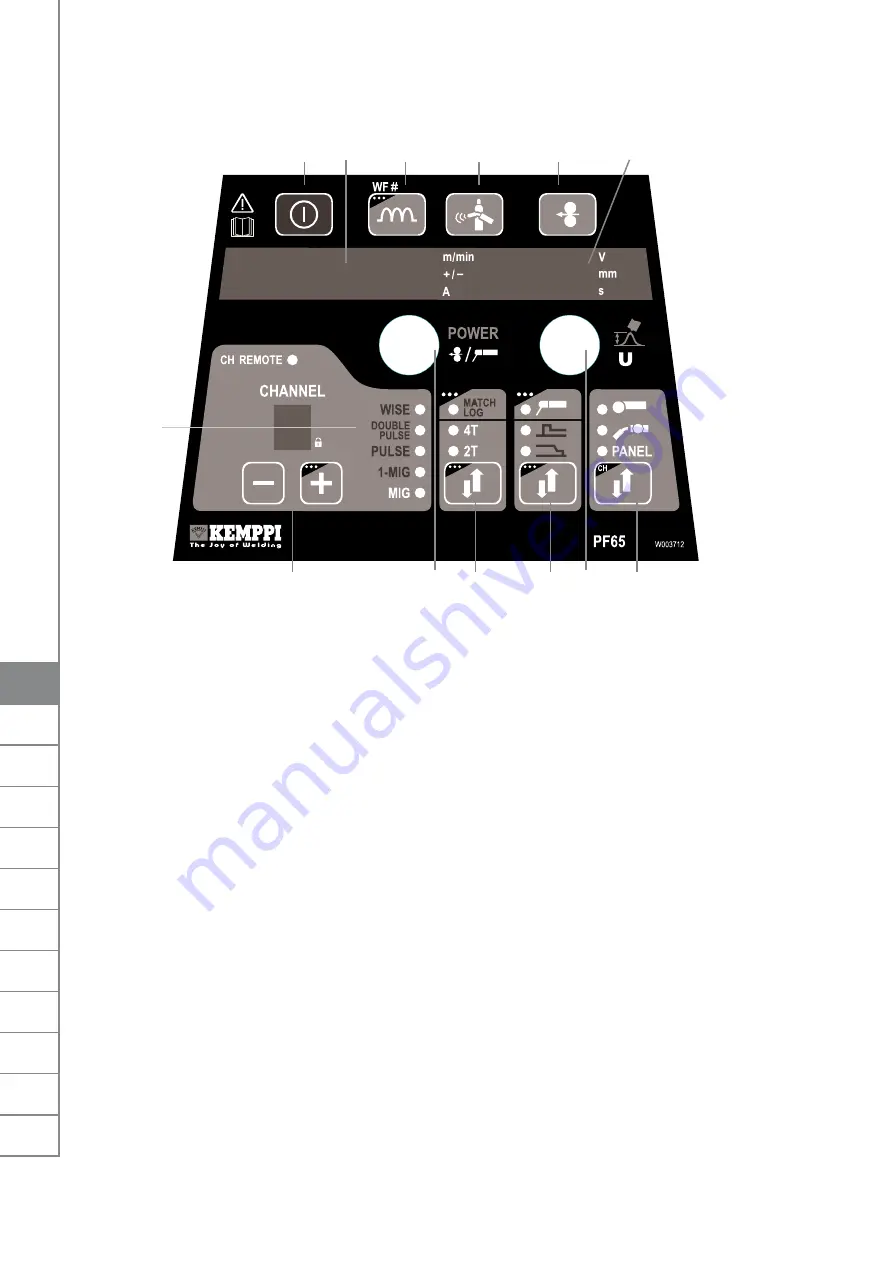
EN
pF65 panel OvervieW
5.12
9.
13.
10.
11.
12.
7.
8.
1.
4.
3.
5.
2.
6.
Main switch (long press)
1.
a) Wire feed speed/welding current display
2.
b) Display of selected adjustable parameter
a) Activation of MIG welding dynamics / Arc Force adjustment
3.
b) Selection of Wire Feeder (= paralleled wire feeders)
Gas purge
4.
Wire inch
5.
a) Display of welding voltage /plate thickness /timer settings
6.
b) Display of selected adjustable parameter
Selection of MIG gun trigger function: 2T/4T/MATCHLOG long press *)
7.
Display of welding process: MIG, 1-MIG, PULSE, DOUBLE PULSE, WISE *)
8.
a) Selection of additional MIG functions
9.
b) Activation of MMA welding process (long press*)
a) Adjustment of wire feed speed
10.
b) Adjustment of welding power (Synergic 1-MIG and PULSE)
c) Adjustment of electrode welding (MMA) current *)
d) Adjustment of additional parameters when selected (ie Wire inch, Gas Test)
Memory channels 0-9, programming through P65 panel on the power source, panel lock
11.
(long press on +)
a) Adjustment of welding voltage
12.
b) Adjustment of length of welding arc (Synergic 1-MIG and PULSE)
c) Adjustment of additional parameters when selected (ie MIG Dynamics)
Panel control/remote control unit selection, channel remote control (long press)
13.
*) Not included on standard delivery, see chapter 6: Ordering numbers
automatic Weld data display:
Last recorded welding values are displayed post welding. See power source panel P65.Select
MENU and then Weld Data.
20
FastM
ig MXF65, 67 / © Kemppi O
y / 0920
I
Summary of Contents for MXF 65
Page 2: ......
Page 3: ...EN Operating manual English FastMig MXF65 67 Kemppi Oy 0920 ...
Page 31: ......