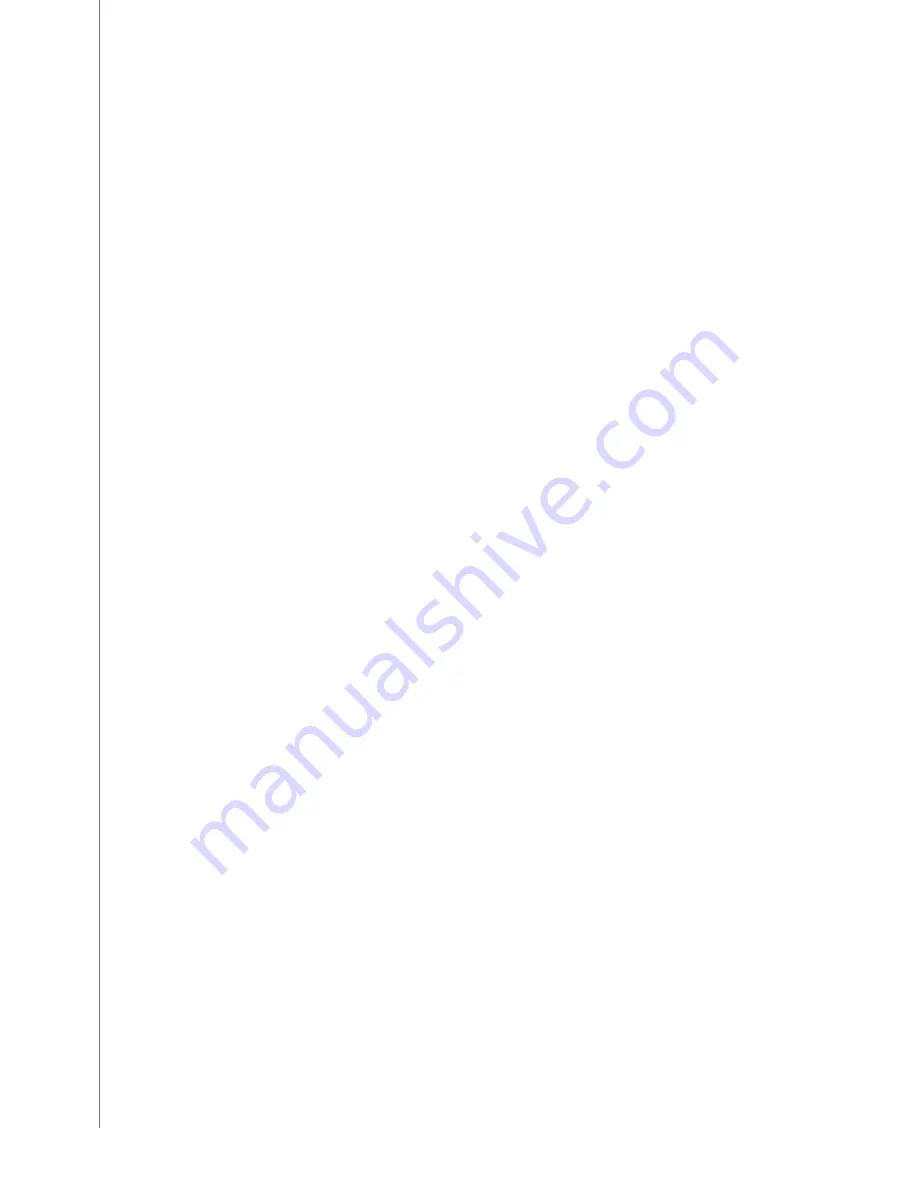
EN
5.
MAINTENANCE
The amount of use and the working environment should be taken into consideration
when planning the frequency of maintenance of the machine. Careful use and preventive
maintenance will help to ensure trouble-free operation.
5.1
CABLES
Check the condition of welding and connection cables daily. Do not use damaged cables.
Make sure that the mains cables in use are safe and according to laid down regulations.
The repair and mounting of a mains connection cable should be carried out only by an
authorised electrician.
5.2
POWER SOURCE
NOTE!
Disconnect the plug of the machine from the mains socket and wait approx. 2 minutes
(capacitor charge) before removing the cover plate.
Check at least every half year:
•
Electric connectors of the machine – clean the oxidised parts and tighten the loosened
ones.
NOTE!
You must know correction tension torques before starting the reparation of the joints.
•
Clean the inner parts of the machine from dust and dirt e.g. with a soft brush and
vacuum cleaner. Also clean the ventilation net behind the front grate.
•
Do not use compressed air, there is a risk that dirt is packed even more tightly into gaps
of cooling profiles.
•
Do not use pressure washing device.
•
Only authorised electrician shall carry out repairs to the machines.
5.3
REGULAR MAINTENANCE
Kemppi Service Workshops make regular maintenance according to agreement.
The major points in the maintenance procedure are listed as follows:
•
Cleaning of the machine
•
Checking and maintenance of the welding tools
•
Checking of connectors, switches and potentiometers
•
Checking of electric connections
•
Checking of mains cable and plug
•
Damaged parts or parts in bad connection are replaced by new ones
•
Maintenance testing. Operation and performance values of the machine are checked,
and adjusted when necessary by means of test equipment.
6.
OPERATION DISTURBANCES
In the event of a failure of the machine, contact an authorised Kemppi service agent or your
local Kemppi dealer.
Check the maintenance objects before the machine is sent to the Service Workshop.
6.1
OPERATION OF THE OVERLOAD PROTECTION
Yellow pilot lamp H12 of thermal protection is lit when thermostat has operated due to
overheating of machine.
The thermostat of machine will operate, if machine is continuously loaded over rated values or
cooling air circulation is blocked.
Cooling fan cools down the machine and when the pilot lamp is not lit the machine is
automatically ready for welding.
8
FastM
ig KMS 300, 400, 500 / © Kemppi O
y / 1110