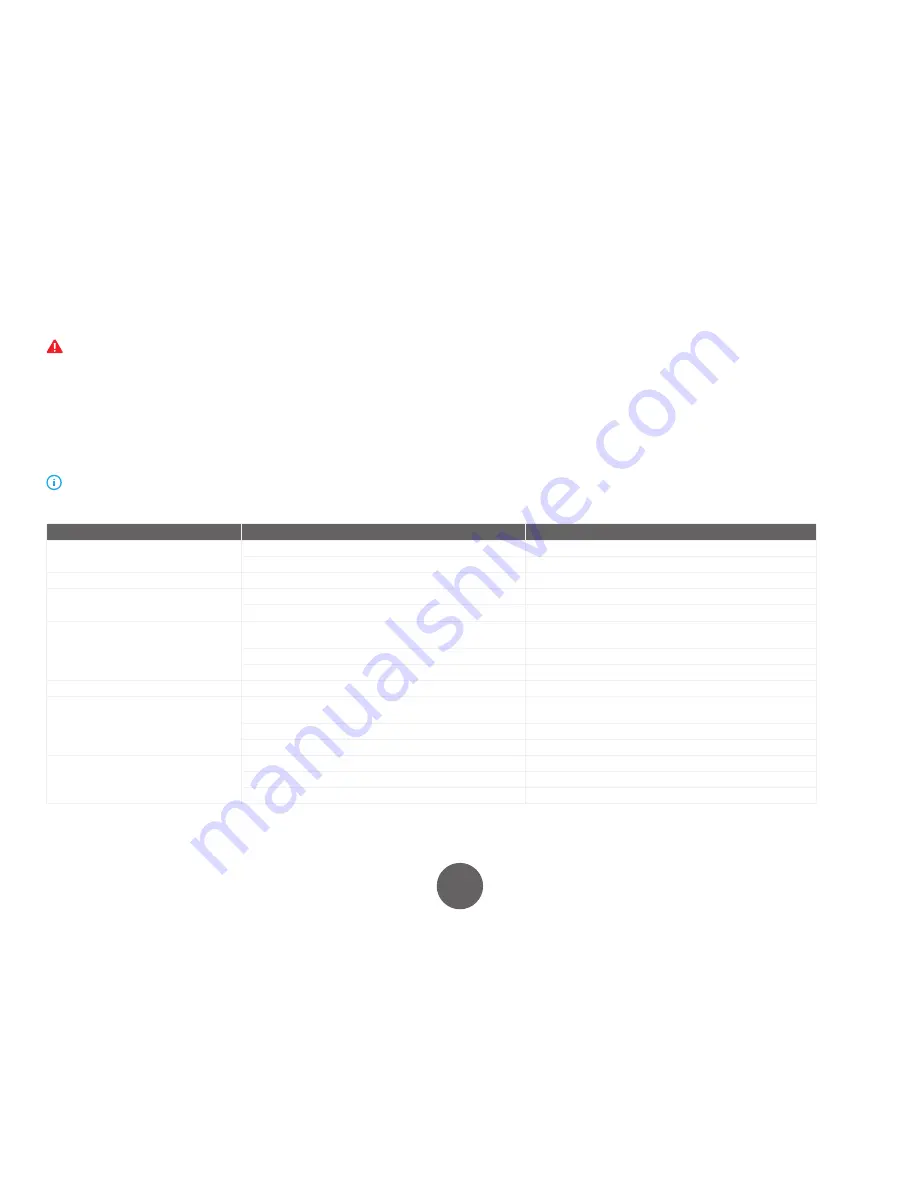
16
A7 MIG Gun 500-g
© Kemppi Oy 2016
1616
OPERA
TING M
ANU
AL
13. TROUBLESHOOTING
Risk of injury due to unexpected start-up
For the entire duration of maintenance, servicing, unmounting, and repair work, the
following instructions must be adhered to:
• Switch off the power supply.
• Cut off the compressed air supply.
• Pull the power plug.
In the event of any doubts or problems, please contact your retailer or the
manufacturer.
Please also consult the operating instructions for the other welding components,
such as the power supply and air pressure line.
Problem
Cause
Solution
Gun neck gets hot
Contact tip not tightened
Check and tighten
Contact tip loose on the neck side.
Check and tighten, and direct toward the work piece
No push-button function
Control line interrupted or defective
Check/repair
Wire burned solid in the contact tip
Wrong parameters set
Check or correct the setting(s)
Contact tip worn out
Replace
Irregular wire feed
Guide spiral liner / PA liner clogged
Clean in both directions with compressed air, or replace the liner if
necessary
Contact tip and wire diameter not correctly matched
Replace contact tip
Wrong contact pressure set at the wire feed unit
Correct as specified by manufacturer
Arc between gas nozzle and work piece
Spatter bridge between contact tip and gas nozzle
Clean and spray gas nozzle interior
Unstable arc
Contact tip not matched to the wire diameter, or increase in contact
tip diameter
Check contact tip
Wrong welding parameters set
Correct welding parameters
Wire guide unit worn out
Replace wire guide unit
Pore formation
Strong spattering in the gas nozzle
Clean gas nozzle
Insufficient or missing gas cover
Check gas cylinder contents and pressure setting
Air currents blow shielding gas away
Shield welding area with partitions