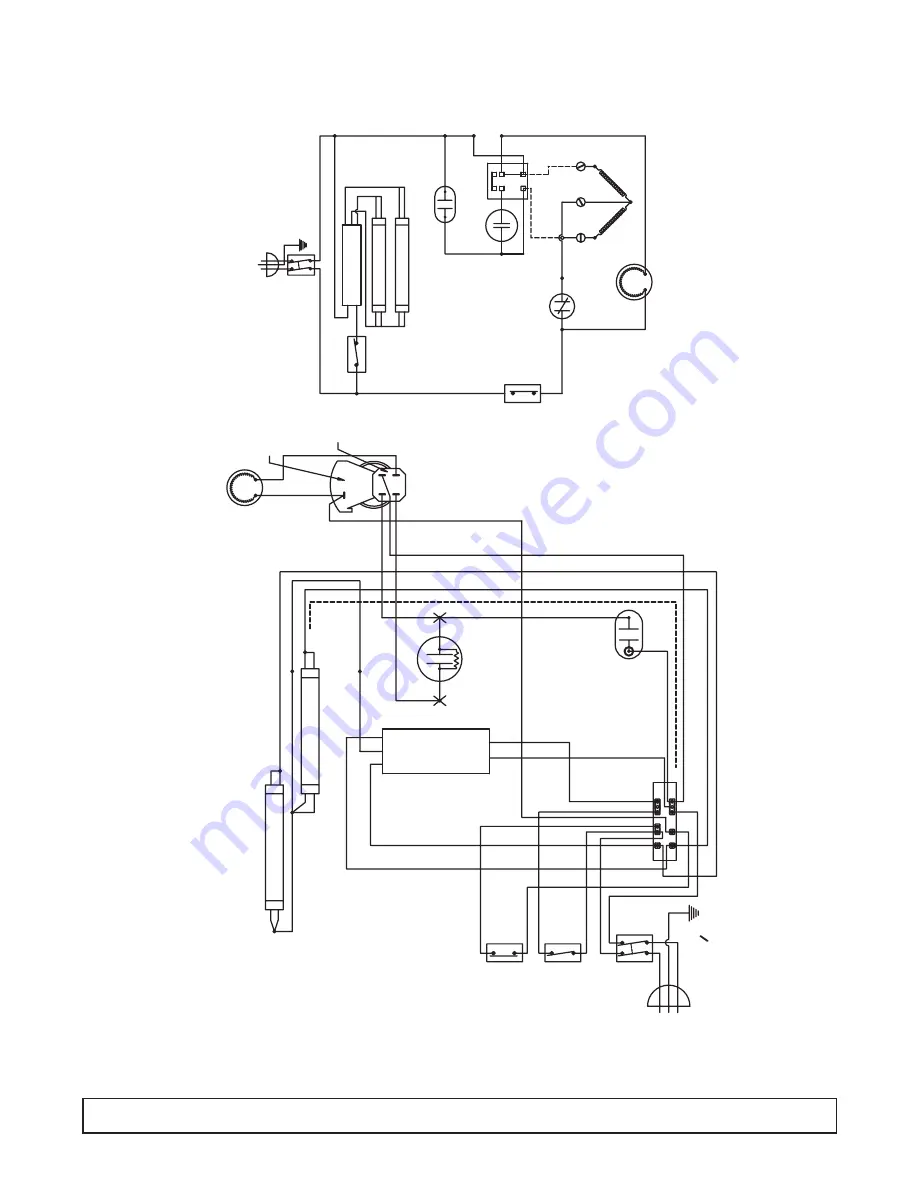
PRINCIPLES OF OPERATION
25
WIRING DIAGRAM - 8HC, 12HC, 16HC WITH 3500K LIGHTS
WIRE DIAGRAM
CKDC-47. 67 & 87 (3500K LIGHTS)
00-C-3020-00A
BLUE
BLUE
BLUE
BLUE
BLACK
BLACK
BLACK
BLACK
BLACK
WHITE
BLACK
WHITE
BLACK
RED
BLUE
BLUE
BLACK
WHITE
YELLOW
WHITE (EXTRA)
WHITE
BLACK
RED
BLACK
BLUE
BLACK
BLACK
6
5
4
3
2
1
LAMP
RUN CAP.
START CAP.
TERMINAL
115 VAC. 60 Hz.-10
SUPPLY
LIGHT
TEMP.
LAMP
BALLAST
BOARD
SWITCH
SWITCH
CONTROL
POWER SUPPLY
LAMP
BALLAST
CONTROL
SWITCH
TEMP.
LIGHT
PROTECTOR
MOTOR
FAN MOTOR
S
C
R
COMPRESSOR
SWITCH
SUPPLY
BLACK
WHITE
L1
N
(BROWN)
(BLUE)
(L2)
LAMP
COMPRESSOR
TERMINAL BOX
(PTCR)
4
1
3
2
FAN MOTOR
MOTOR PROTECTOR
(PTCR)
START CAP.
RUN CAP.
4
3
1
2
Dipping Cabinet 1298.02 2/3/03 1:14 PM Page 27
Summary of Contents for R-404A
Page 3: ...Introduction...
Page 13: ...SECTION II Principles of Operation...
Page 14: ......
Page 28: ......
Page 29: ...SECTION III Maintenance Repair...
Page 55: ...PARTS LISTING With Illustration Identification...
Page 56: ...CABINET PARTS EXPLODED VIEW 54 CABINET PARTS EXPLODED VIEW 2 1 3 4 7 9 8 6 10 11 5...
Page 60: ...CONDENSING UNIT EXPLODED VIEW 58 CONDENSING UNIT EXPLODED VIEW...
Page 62: ...ELECTRICAL PARTS EXPLODED VIEW 60 ELECTRICAL PARTS EXPLODED VIEW...
Page 64: ...1 6 7 2 4 3 5 LID EXPLODED VIEW 62 LID EXPLODED VIEW...
Page 66: ......
Page 67: ...ACCESSORIES...
Page 68: ......
Page 73: ...ADJUSTABLE LEG KIT 52 1831 01 ACCESSORIES 71...
Page 74: ...CASTER KIT 52 1830 01 72 ACCESSORIES...
Page 76: ...CAN CLAMP INSTALLATION 74 ACCESSORIES...
Page 79: ......
Page 80: ...by National Refrigeration Products 563 Corbin Road Honea Path South Carolina 800 486 8369...