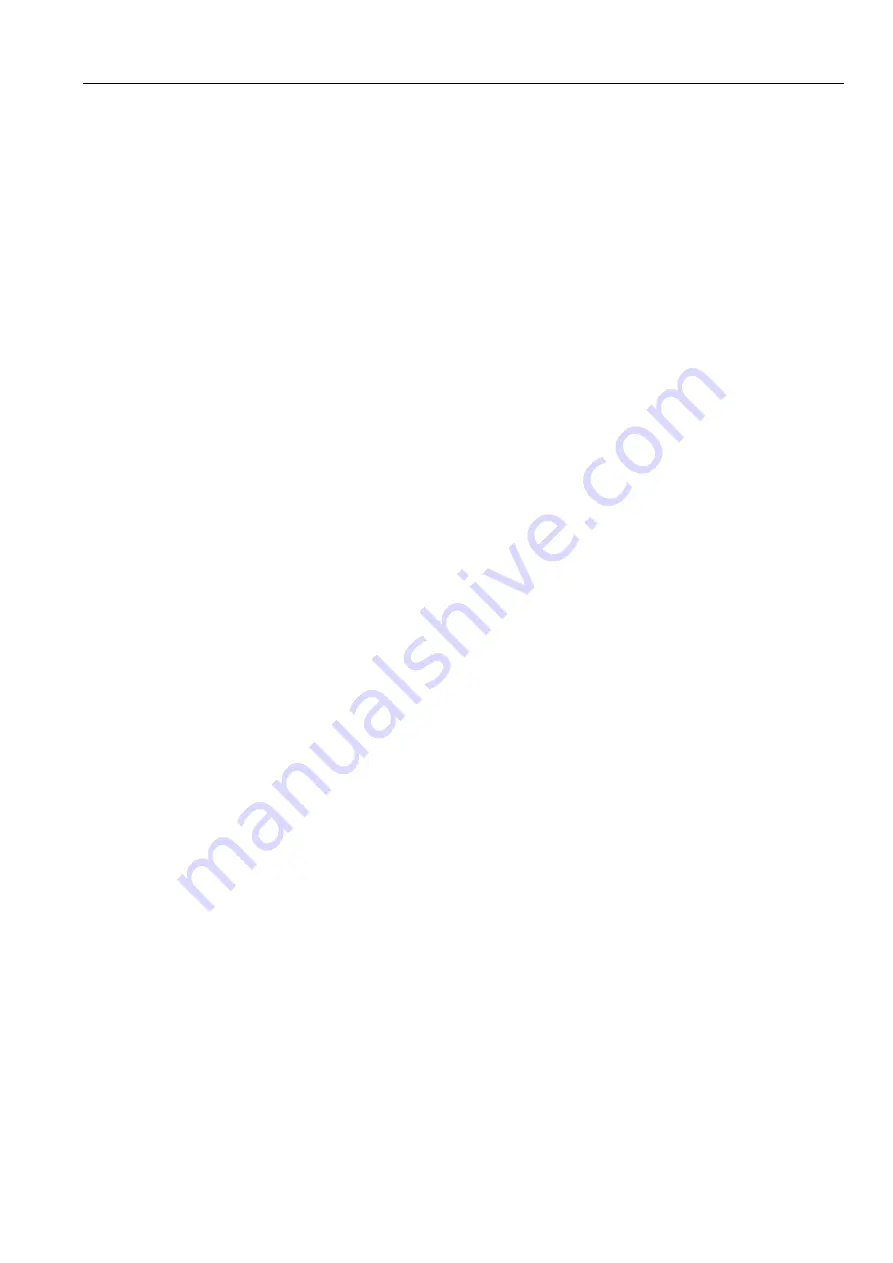
Kelly KHS High Voltage Sine Wave Brushless DC Motor Controller User
’s Manual
V 1.10
1
Contents
................................................................................. 2
Chapter 2 Features and Specifications
........................................................ 3
Chapter 3 Wiring and Installation ................................................................ 6
Chapter 4 Programmable Parameters
....................................................... 16
4.4 How to use Identification angle operation for KHS-I controller............................. 24
4.5 How to use Identification angle operation for KHS-IPS controller ........................ 29
............................................................................. 36
............................................................................ 38