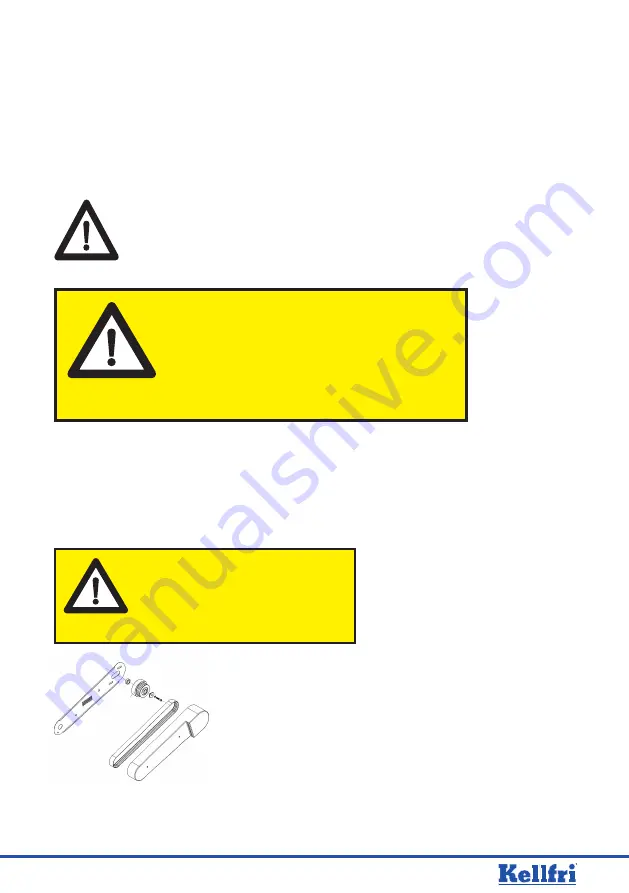
9
USE / OPERATION
Only people who understand the safety information and instructions in this manual may op-
erated the equipment. Be alert and careful when working with the machine and only use the
tool or product in the manner described in this manual. When working with equipment that
has moving parts, there is always the risk of injury. Be careful when working with equipment
equipped with hydraulic hoses ,oil under pressure can penetrate the skin. Seek medical at-
tention immediately if this occurs. Always work alone with the tools that are defined as single
porpose tools. Respect the equipment’s danger zone.
Overexposure to vibration may lead to circulatory or nerve damage, particularly
in people who have impaired circulation. Contact your doctor if you experience
symptoms that could have been caused by overexposure to vibration. Examples
of common symptoms include numbness, pain, muscle weakness, change of skin
color or an uncomfortable feeling of tingling. These symptoms appear most fre-
quently in the fingers, hands or wrists.
Important!
Always use approved protective clothing and approved protective
equipment when using the machine. Protective clothing and protective
equipment cannot eliminate the risk of accident, but wearing proper
clothing and the correct equipment will reduce the degree of injury
should an accident occur. Ask your dealer about approved protective
clothing and approved protective equipment recommended
.
FUELING
Read the safety instructions before fueling. Keep the fuel and fuel tank clean. Avoid filling the
machine with dirty fuel. Make sure the fuel cap is properly tightened and the gasket is not
damaged, particularly before washing the machine. SAE10W-30 is recommended for general
use. If the engine “bolts” at normal load it can be damaged. Change the fuel. If this does not
help, contact an authorized service workshop. Do not fill the tank completely; leave space for
the fuel to expand as it warms up.
Warning!
Gasoline is highly flammable. Observe caution
and fill the tank outdoors. (See the safety in-
structions).
CENTRIFUGAL
CLUT
CH
Centrifugal clutch
The engine is equipped with a centrifugal clutch that is con-
nected to the crankshaft. When the engine speed increases, the
drive for cutting wheel engages automatically. The centrifugal
clutch is maintenance-face; it is not possible for the user to make
adjustments..
Summary of Contents for 27-SF20
Page 22: ...22...
Page 24: ...24 HANDLE ASSY...