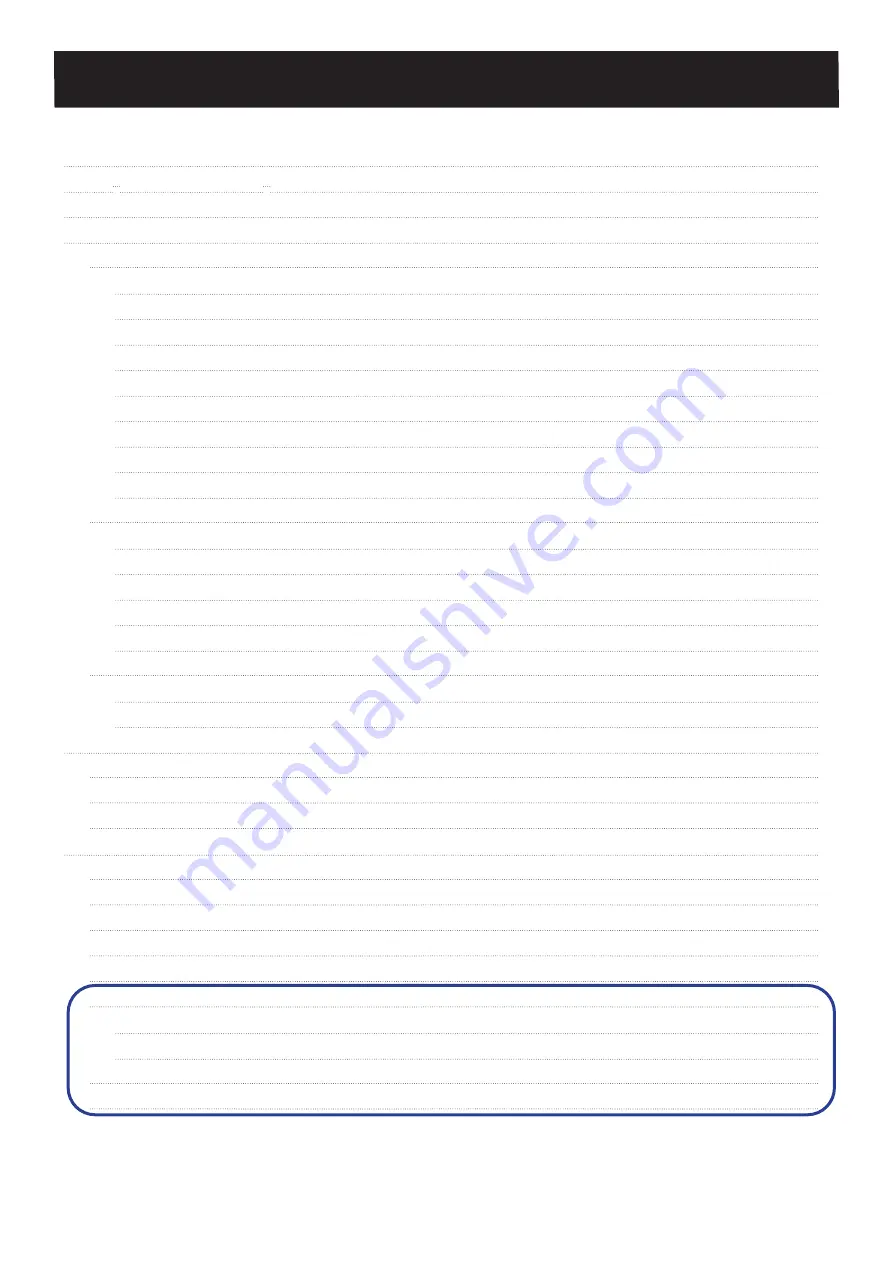
i
DOC06340 Rev.
OWNER / OPERATOR MANUAL
RUNNING FLOOR II
®
DX-i
Table of Contents
Introduction iii
KEITH
®
RUNNING FLOOR
®
DX-i Unloading System Limited Warranty
iv
Warranty Registration Card
vi
1.0 Safety
1
1.1 General Safety
1
1.1.1 Intended Function and Expected Use
1
1.1.2 Improper Use
1
1.1.3 Training
1
1.1.4 Personal Protective Equipment
2
1.1.5 Airborne Noise Emission
2
1.1.6 Temperature
2
1.1.7 Lighting
2
1.1.8 Movement Around the System
2
1.1.9 Hydraulic Oil Safety
2
1.2 Design / Installation Safety
3
1.2.1 Kit Components
3
1.2.2 Installation
3
1.2.3 Danger Zones
3
1.2.4 Hydraulics
3
1.2.5 Controls
3
1.3 Marking of Machinery
4
1.3.1 Safety Decals
4
1.3.2 Serial Plate
6
2.0 Specifications
7
2.1 Hydraulic Drive Unit
7
2.2 General Wet Kit Specifications
8
2.3 Floor to Wet Kit Diagram
9
3.0 Operation
10
3.1 How It Works
10
3.2 Oil Flow Diagram
11
3.3 Component Location Guides
13
3.4 Component Descriptions
15
3.5 Component Identification
16
3.6 Start Up
17
3.6.1 Before Initial Start-Up
17
3.6.2 After initial 6 working hours (first week of operation)
17
3.7 Pre-Trip Checklist
17
3.8 Standard Operating Procedure (Manual Controls)
18
Operating
Instructions