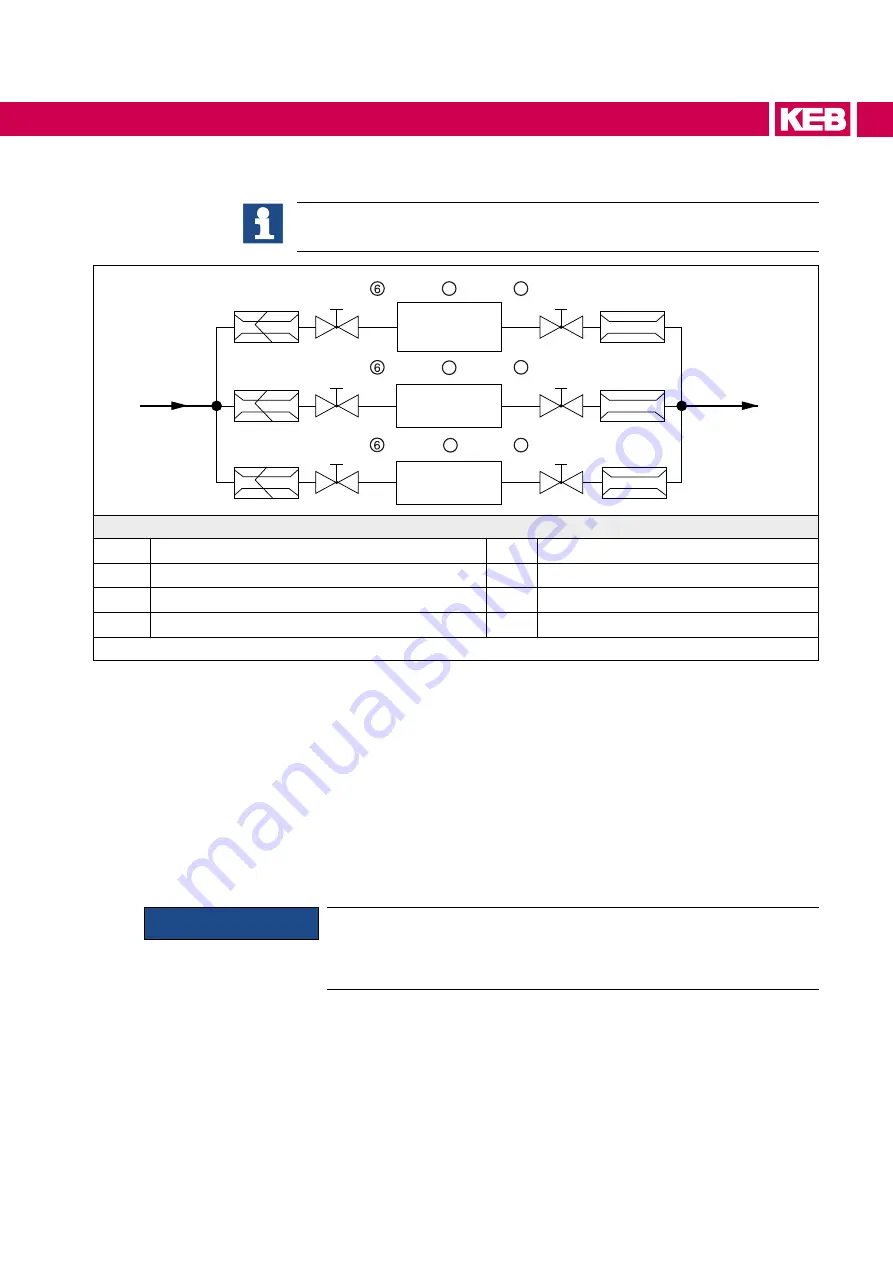
10.1.5.4 Connection scheme for a cooling circuit (parallel connection)
This connection scheme is only an installation proposal and does not replace
professional planning and execution!
①
➃
➄
②
③
②
①
②
③
②
①
②
②
Master
Slave
Slave
③
7
7
7
8
8
8
1/2“
1/2“
1/2“
1/2“
1/2“
1/2“
3/4“
3/4“
Legend
①
Flow limiter 10...40 l/min
⑤
Return flow entire system
②
Ball valve/stop valve
⑥
Precharging drive converter
③
Flow switch (e.g. Sika VH / VK)
⑦
Return flow drive converter
④
Pre-run entire system
⑧
Drive converter
Figure 30: Connection scheme for a cooling circuit
The connection of the coolant circuit to the drive converter system as a parallel execu-
tion is also possible in the rated operation and mandatory for special applications.
It should be noted that the use of flow controller and a temperature monitoring is manda
-
tory required. The cooling flow must always be started before starting the COMBIVERT.
Other elements in the cooling circuit such as pumps, shut-off valves, ventilation etc.
must be attached according to the cooling system and the local conditions.
The total volume flow depends on the specified heat power dissipation of the drive
converter system (see technical data). The data apply for rated operation. Special ap-
plications on request. The relationships between heat power dissipation, flow and tem
-
perature difference are shown in the diagram
„Volume flow in dependence of the heat
power dissipation and temperature difference“
NOTICE
The maximum temperature difference (ΔT) between pre-run and return
flow may not exceed 7K. If the volume flow (above 30 l/min per mod
-
ule) is selected too large, increases the risk of erosion in the liquid
cooler.
10.1.6 Decommissioning
The cooling circuit must be completely empty if a unit shall be switched off for a longer
period. The cooling circuit must be blown out additionally with compressed air at tem-
peratures below 0°C.
69
COOLING SySTEM
Summary of Contents for COMBIVERT F5 Series
Page 2: ......