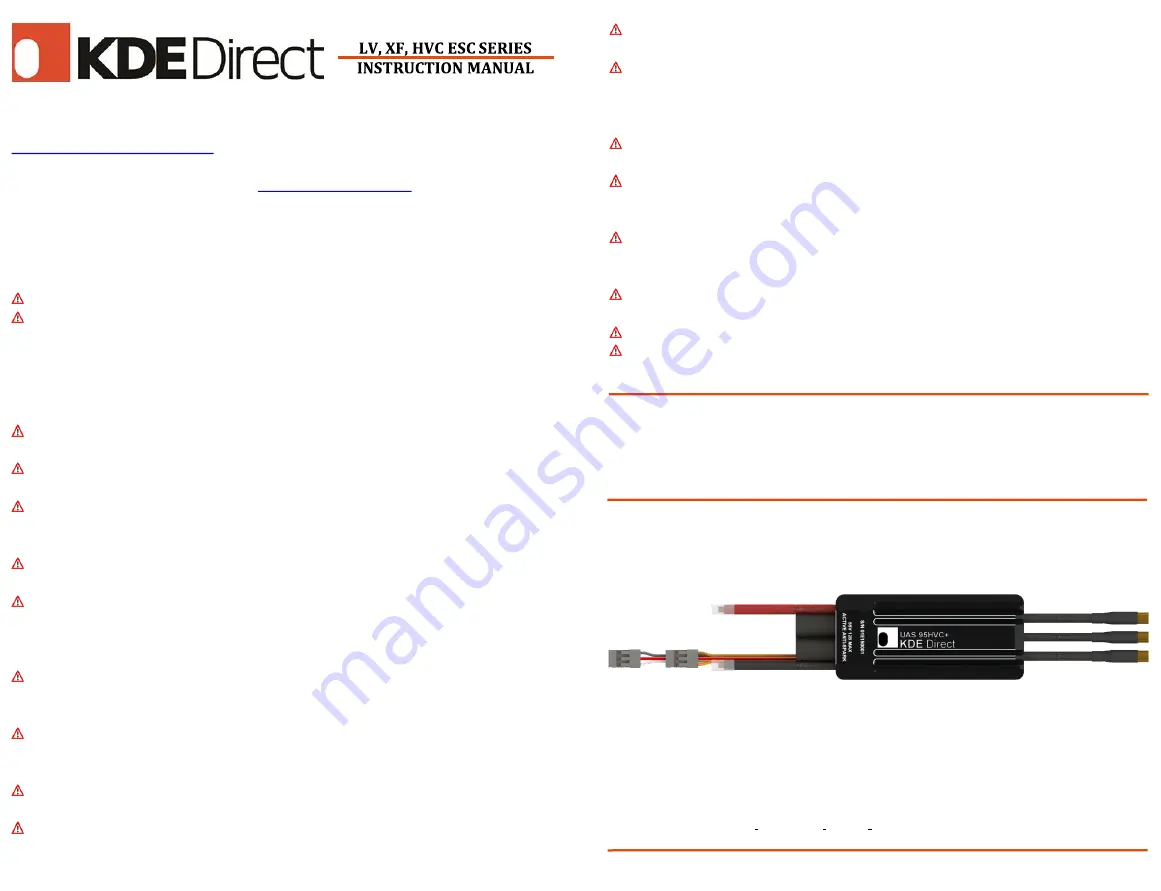
IMPORTANT: To reduce the risk of fire, bodily injury, and damage to the
equipment, read through Instruction Manual before operating ESC and
always follow all instructions.
KEEP OUT OF THE REACH OF CHILDREN.
Pay attention to the maximum voltage allowed:
KDE-UAS LV Series
7
.4V (2S LiPo)
–
26.1V (6S LiHV)
26.5V Max.
KDE-UAS XF Series
7.4V (2S LiPo)
–
34.8V (8S LiHV)
35V Max.
KDE-UAS HVC Series
11.1V (3S LiPo)
–
52.2V (12S LiHV) 55V Max.
If model is not listed, maximum voltage is stated in specifications.
Operating outside of the listed voltage voids warranty.
All KDE Direct ESCs are opto-isolated and do not provide BEC power output for
the peripheral equipment and requires 3 to 12V applied to the control lead.
Never operate the ESC beyond the specifications stated on hardware. Serious
injury or property damage can result from misuse.
Ensure the polarity is correct with the power supply to the ESC power source
leads. Reverse polarity may cause fire and serious injury and will immediately
damage the ESC beyond warranty coverage.
Ensure the ESC is installed in a safe location and protected to prevent any
exposed connections and solder-locations from contacting conductive areas.
Always use electronics-grade solder and make sure to use proper soldering
techniques and equipment. Poor soldering technique is a common cause of in-
flight failure and ESC damage. Ensure all connectors are protected with
insulation and heat-shrink to prevent unwanted conduction and shorts.
Check all connectors for secure connection before flight. Disconnection due to
vibration and flight-conditions can result in a dangerous loss of control and
potential damage and serious injury.
Do not disassemble or open the ESC or DMA. Opening of the case or removal of
shrink-wrap may cause damage to the internal components, void all warranty
claims, and yield unsafe operation.
Install the ESC in a location with adequate airflow to maintain cool
temperatures and achieve the maximum performance rating.
An electric motor that is connected to the ESC can start unexpectedly and can
cause serious injuries. Always remove the propeller and disengage all gearing
when working on the system with power applied.
Do not allow full submersion of the ESC in water. Water can damage the ESC
and cause malfunction and failure of the electrical components.
KDE Direct is not responsible for the use of this Product(s) or for any
damages or injuries caused or sustained by its usage. Always observe all
laws and instructions regarding the use of this Product(s), and operation of
devices using this Product(s).
This is a high-power, electromechanical device with the potential to be very
dangerous
–
always handle with caution and be aware of proper operation.
This product may contain chemicals known to the State of California to cause
cancer and/or birth defects or other reproductive harm. Do not ingest or
attempt to ingest this product.
Disconnect brushless motor from ESC motor leads before programming ESC.
An electric motor that is connected to the ESC can start unexpectedly and
cause serious injuries or damage.
Before flight, ensure that all ESCs are operating on the same settings and
firmware.
Extending the ESC power leads is at your own risk and voids the warranty.
At low load we recommend you turn off Synchronous Rectification, low load
may result in discontinuity with the motor RPM.
REVISION PR012
For the latest instruction manual revisions, software updates, liability
policy, and warranty information, visit the KDE Direct website at:
All technical inquiries, review the
Pay close attention to proper wiring as shown in the diagram above. Ensure the
polarity is correct and proper soldering techniques are used when connecting
the power source and brushless motor to prevent damaging the ESC.
ESC INSTALLATION AND WIRING
(-) TO POWER SOURCE
(BLACK POWER LEAD)
TO FLIGHT CONTROLLER
(W-R-BLK CONTROL LEAD)
TO BRUSHLESS MOTOR
(BLACK MOTOR LEADS)
(+) TO POWER SOURCE
(RED POWER LEAD)
TO DEVICE MANAGER ADAPTER
(O-R-BRN PROGRAMMING LEAD)
1
2
The KDE Direct UAS ESC (Electronic Speed Controller) Series is specifically
designed for multi-rotor applications, and utilizes a proprietary algorithm
for up to 600Hz refresh rate communication and high-speed response for
optimal flight performance.