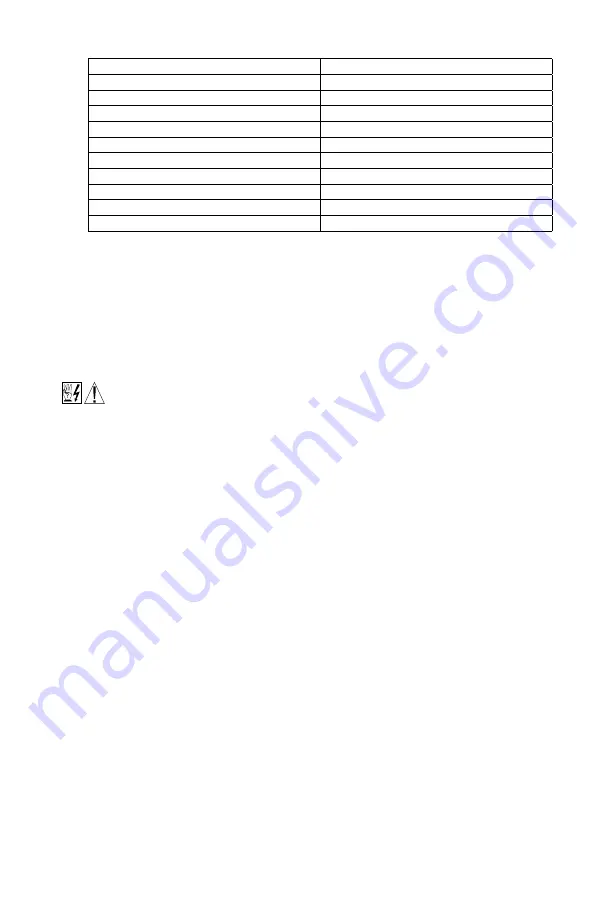
29
Table 7 – Drive Operating Condition and Status LED Indicator
Drive Operating Condition
Flash Rate
1
and LED Color
Normal Operation
Slow Flash Green
Overload (120% – 160% Full Load)
Steady Red
2
I
2
t (Drive Timed Out)
Quick Flash Red
2
Short Circuit
Slow Flash Red
Undervoltage
Quick Flash Red / Yellow
3
Overvoltage
Slow Flash Red / Yellow
3
Stop
Steady Yellow
Stand-By
4
Slow Flash Yellow
Input Phase Loss
5
Rapid Flash Yellow
Overtemperature Trip
6
Slow / Quick Flash Red
1
Notes: 1.
Slow Flash = 1 second on and 1 second off. Quick Flash = 0.25 second on and 0.25 second off.
2.
When the Overload is removed, before
the I
2
t times out and trips the drive, the “ST” LED will flash green.
3.
When the Undervoltage or Overvoltage condition is corrected, the “ST” LED
will flash Red / Yellow / Green.
4.
Only if the Forward-Stop-Reverse Switch is installed.
5.
Model KBAC-29, with three-Phase AC Line input, and
Models KBAC-45, 48. Rapid Flash = 4 mSec on and 6 mSec off.
6.
KBAC-217 Series and KBAC-416 Series only.
13 TRIMPOT ADJUSTMENTS
The drive contains trimpots which are factory set for most applications. See Figure 2 on page 10 for the
location of the trimpots and their approximate factory calibrated positions. Some applications may
require readjustment of the trimpots in order to tailor the drive for a specific requirement. The trimpots
may be readjusted as described below.
WARNING! If possible, do not adjust trimpots with the main power applied. If adjust-
ments are made with the main power applied, an insulated adjustment tool must be
used and safety glasses must be worn. High voltage exists in this drive. Fire and/or electrocution
can result if caution is not exercised. The Safety Warning on page 5 must be read and understood
before proceeding.
13.1 Minimum Speed (MIN) – Sets the minimum speed of the motor. The MIN Trimpot is factory set to
0% of frequency setting. For a higher minimum speed setting, rotate the MIN Trimpot clockwise.
See Figure 34 on page 30.
13.2 Maximum Speed (MAX) – Sets the maximum speed of the motor. The MAX Trimpot is factory set
to 100% of frequency setting. For a lower maximum speed setting, rotate the MAX Trimpot counter-
clockwise. For a higher maximum speed setting, rotate the MAX Trimpot clockwise. See Figure 35
on page 30.
13.3 Acceleration (ACCEL) – Sets the amount of time for the motor to accelerate from zero speed to full
speed. The ACCEL Trimpot is factory set to 1.5 seconds. For a longer acceleration time, rotate the
ACCEL Trimpot clockwise. For more rapid acceleration, rotate the ACCEL Trimpot counterclockwise.
See Figure 36 on page 30.
Note:
Rapid acceleration settings may cause the current limit circuit to activate, which will extend the
acceleration time.
13.4 Deceleration (DEC/I) – Sets the amount of time for the motor to decelerate from full speed to zero
speed. The DEC/I Trimpot is factory set to 1.5 seconds. For longer deceleration time, rotate the DEC/I
Trimpot clockwise. For more rapid deceleration, rotate the DEC/I Trimpot counterclockwise. See
Figure 37 on page 30.
Application Note – On applications with high inertial loads, the deceleration time may automati-
cally increase. This will slow down the decrease speed to prevent the bus voltage from rising
to the Overvoltage Trip point. This function is called Regeneration Protection. It is recommended
that for very high inertial loads that both the ACCEL and DEC/I Trimpots be set to greater
than 10 seconds.
13.5 DC Injection Brake (DEC/I) – The drive is factory set for Regenerative Braking (Jumper J7 set to the
“RG” position). When the drive is set for DC Injection Brake (Jumper J7 set to the “INJ” position), the
DEC/I Trimpot is used to set the DC Injection Brake voltage and time. See Figure 38 on page 30. Also
see Section 6.6 on page 25.
Summary of Contents for KBAC Series
Page 34: ...34 Notes...
Page 35: ...35 Notes...