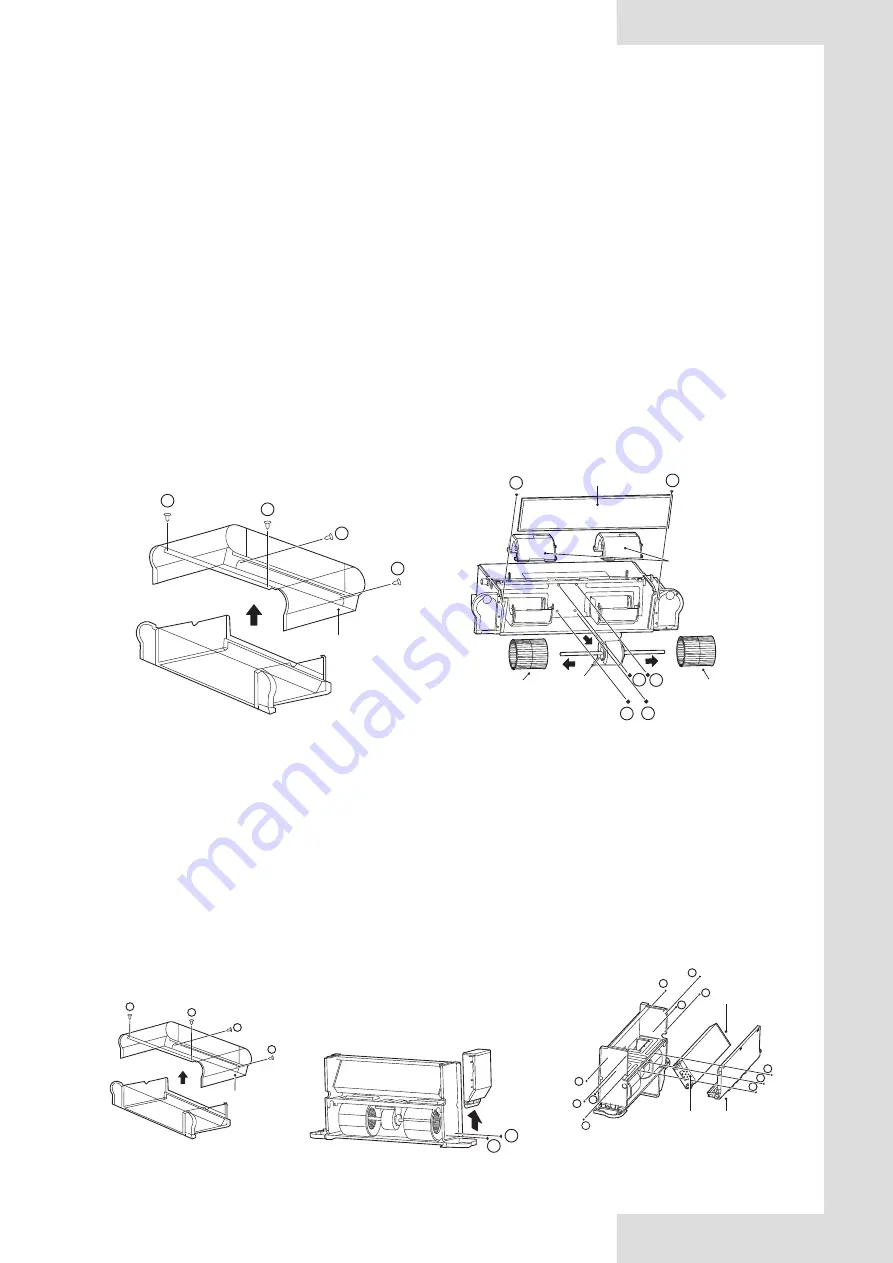
2
2
1
1
Casing
assembly
2 2
2 2
1
1
Fan
Fan
Upper propeller
housing
Filter
Motor
2
2
2
2
1
1
1
1
1
1
1
Heat
exchanger
Temperature
sensor plug
Drain pan
2
2
1
1
Casing
assembly
Electric
control
box
1
1
07
4) If necessary, you should:
a) Remove any foreign matters that may impede air flow.
b) Remove the dust with compressed air or clean water and avoid damage to the heat exchanger.
c) Dry with compressed air.
d) Check for any impurities in the drain pipe that may impede water flow.
e) Check whether the system has air.
●
Start and let the system run for several minutes.
●
Stop the system.
●
Open air discharge valve to remove air.
●
Repeat this operation until the air is exhausted.
5) Maintain the circuits.
Check whether the power cord, electrical contacts, terminals etc. are loose or damaged.
6) If the motor needs to be replaced, follow the steps below:
a) Unplug the unit.
b) As shown in Figure 4-4, remove screws
①
*2 and
②
*2 and then the casing.
c) As shown in Figure 4-5, remove screws
①
*2 to take the filter out. Then, remove the upper volute.
After that, remove four screws (
②
) that fix the motor, to disconnect the motor cable and the main board. Then, take out the fan
and the motor.
Disassemble the fan to get the motor.
Install back the motor in reverse order.
Figure 4-4 Removal of casing
Figure 4-5 Removal of filter, upper volute and motor screws
7) If the heat exchanger needs to be replaced, follow the steps below:
a) Unplug the unit.
b) Shut off the water supply.
c) As shown in Figure 4-6, remove screws
①
*2 and
②
*2 and then the casing.
d) Drain the coil.
e) Disassemble the inlet and outlet pipes.
f)As shown in Figure 4-7, remove screws
①
*2 to remove the electric control box.
g) As shown in Figure 4-8, remove screws
①
*7 to take the drain pan out. Then, remove screws
②
*4 to take the heat
exchanger out.
h) Pull out the temperature sensor plug.
Install back the heat exchanger in reverse order.
Figure 4-6 Removal of casing
Figure 4-7 Removing the electric control box
Figure 4-8 Removal of drain pan and heat exchanger
Summary of Contents for KFC-S2-2T-250D
Page 22: ......