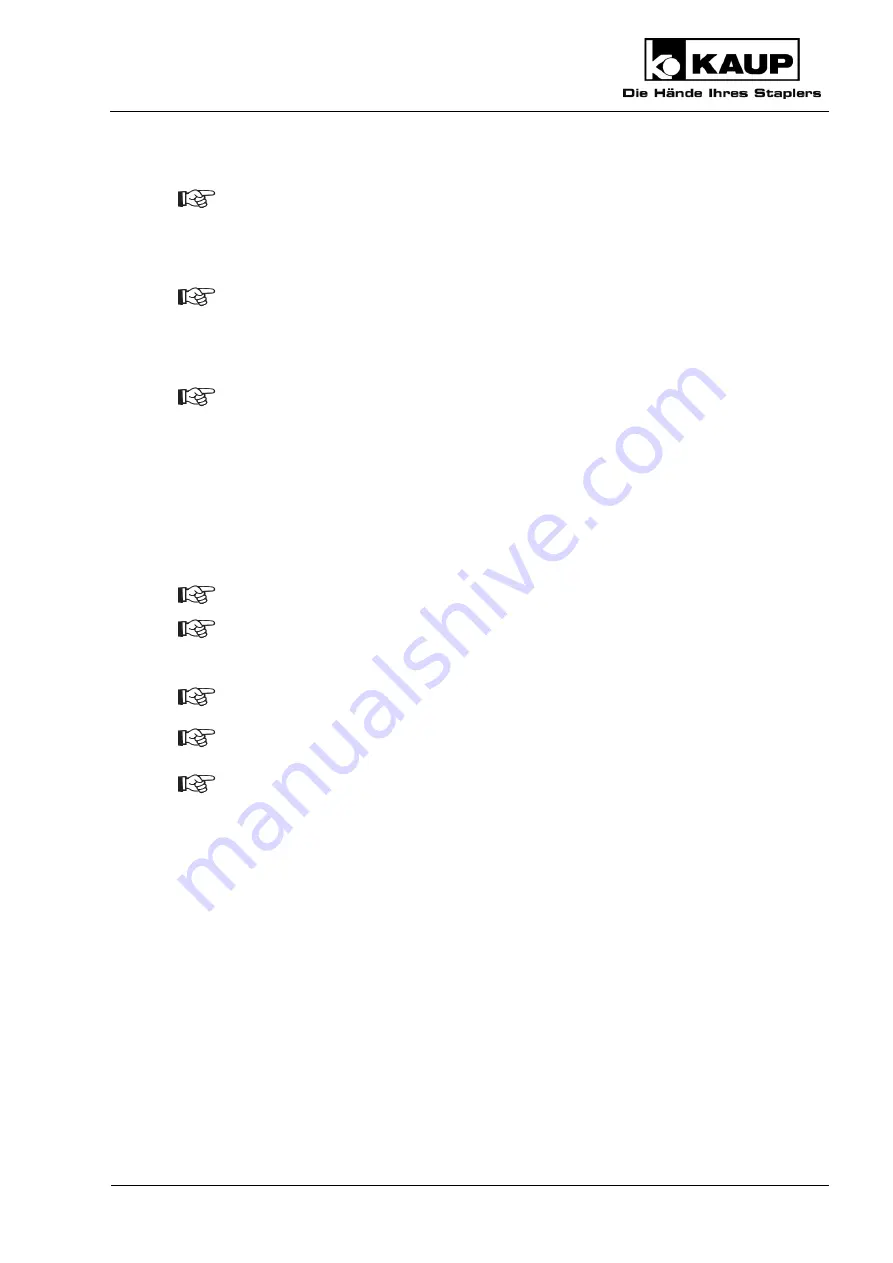
Operating Manual
Original Operating Manual
19
Renew defective cylinders (12) by removing the screws (13) at the fork carriage
(9). Take the entire fork adjusting unit from the fork carriage (9). Remove the nuts
(14) and replace the defective cylinder (12). Insert the entire fork adjusting unit
into the fork carriage (9) and attach it with the screws (13).
Each time a cylinder (10 / 12) is mounted or removed, check the play between the
cylinder retainer (15) and the cylinder nut (10 / 12). The cylinders are installed
with a clearance of from 1.5 to 2 mm.
Replace defective or worn plain bearings (17) in the slide (15) by removing the
screws (13) and the entire fork adjusting unit from the fork carriage (9). Remove
the nuts (14) and the shaft (18). Pull the slide (15) out to the side and replace any
defective or worn plain bearings (17). Push the slide (15) back onto the shaft (18)
and the cylinder (12). Put the nuts (14) on. Insert the entire fork adjusting unit into
the fork carriage (9) and attach it with the screws (13).
6.3.3 Forks
Annually
Inspect the heel of the fork for wear and cracks.
Remove forks from service when wear exceeds 10 % of the thickness of the fork.
As necessary
Bent forks are not safe to operate and their continued use should be prevented.
Straightening of forks may only be performed by the manufacturer of the fork or by
one of his authorised workshops.
You can increase the service life of forks by using forks especially protected
against wear.