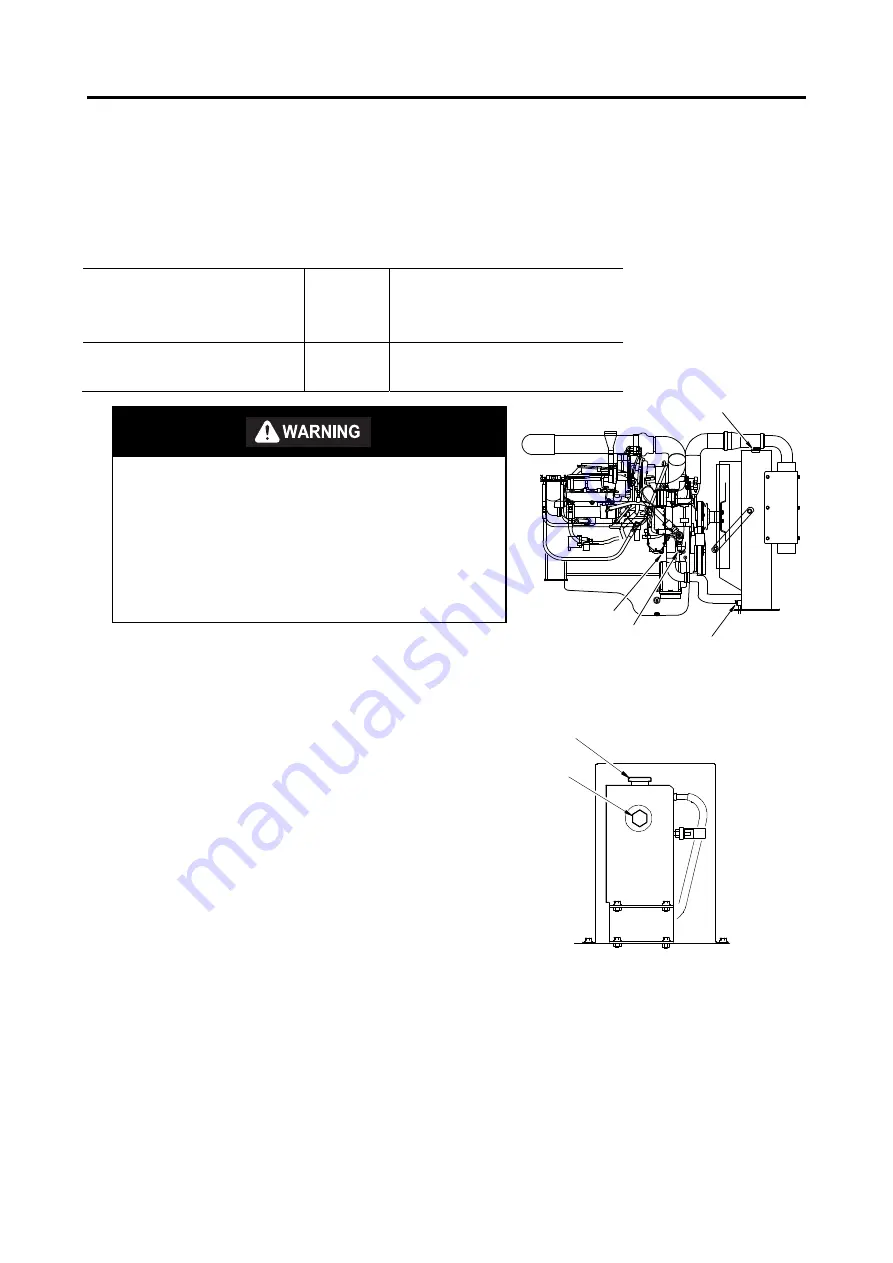
MAINTENANCE
IC120-2 ENG
4-24
IC120-2-C401160
1
2
3
5
IC120-2-C401170
4
6
Change the Coolant
Replace coolant every 2000 years or once every two years.
Use solution of 50% water and 50% ethylene glycol long life coolant (LLC) and DCA solution as
coolant. Never use water only as coolant.
Pouring quantity when replacing coolant
Total coolant quantity
36.5 L
Engine body: 12.8 L
Radiator, etc.: 13.6 L
Coolant tank: 10.2 L
Mixture of LLC and water
34.6 L
LLC = 17.3 L
Water = 17.3 L
Immediately after the engine stops, coolant is
hot. If coolant is discharged immediately, you
may get burnt. Change coolant after the engine
cools down.
Do not remove the cap when the radiator
coolant is hot. Hot water may spout out.
Rotate the cap slowly to relief the pressure after
the coolant temperature lowers.
1. Slowly turn the pressure cap (4) on the coolant tank to
remove it.
2. Loosen the drain cock (2) in the lower part of the
radiator and discharge water into a vessel.
3. Loosen the drain cock (3) of the cylinder block of the
engine and discharge water into the vessel.
4. Loosen the drain cock (5) of the coolant tank and
discharge water into the vessel.
5. Turn the radiator cap (1) slowly to remove it.
6. Clean the coolant tank.
7. Close the drain cocks (2), (3) and (5) after discharging
water.
8. Pour fresh LLC mixture and DCA solution through the
radiator cap. Keep the pressure cap of the coolant
tank removed at this time. Make sure that the tank
becomes full, and close the radiator cap.
9. Pour fresh LLC mixture into the coolant tank. Check
the level through the sight glass (6) of the coolant tank
and close the pressure cap then.
10. Run the engine five minutes and stop it then. Wait
until the temperature of coolant lowers, and check the
coolant level. Refill the tank with coolant if coolant is
insufficient.
Coolant tank