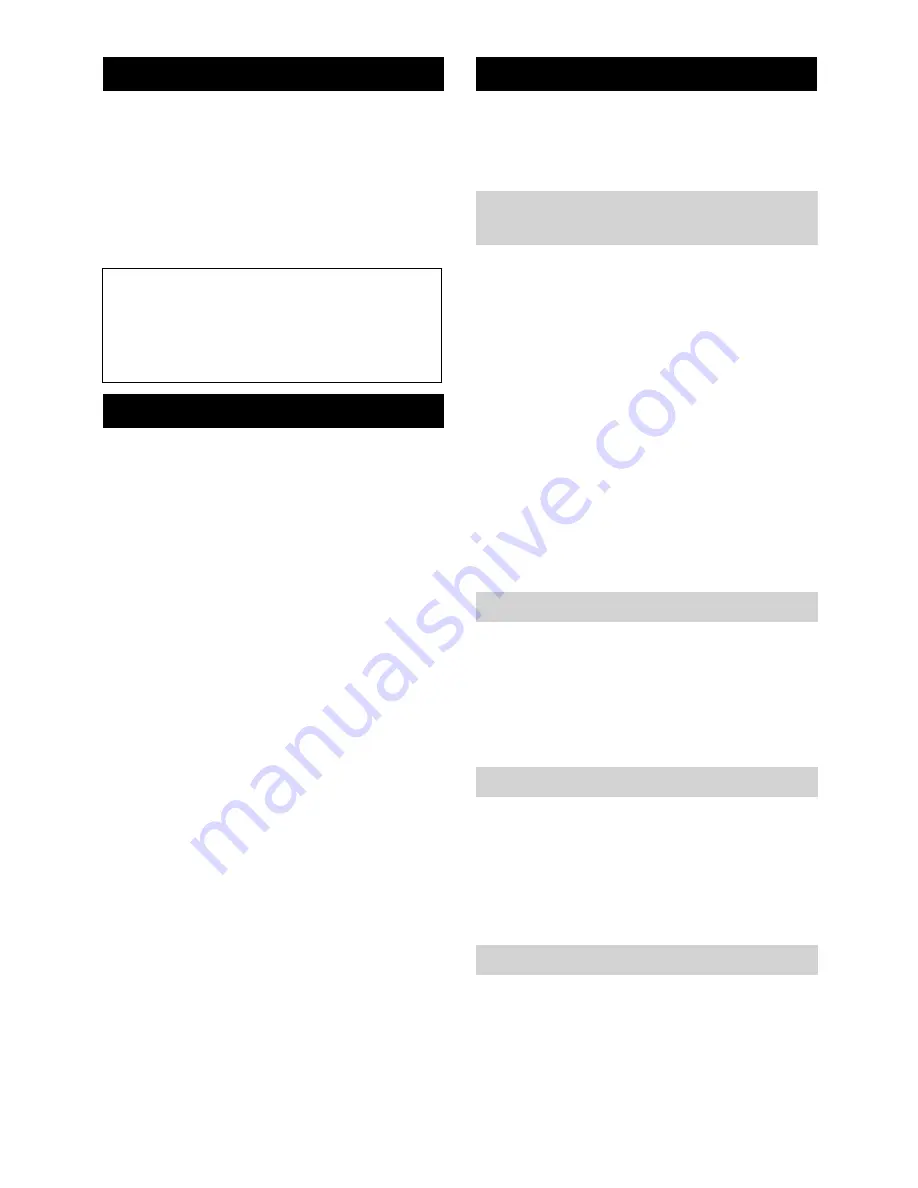
– 3
Cleaning of: Machines, Vehicles, Struc-
tures, Tools, Facades, Terraces, Garden-
ing tools, etc.
Danger
Risk of injury! Follow the respective safety
regulations when operating at gas stations
or other dangerous areas.
–
Please follow the national rules and
regulations for fuel spray jets of the re-
spective country.
–
Please follow the national rules and
regulations for accident prevention of
the respective country. Fuel spray jets
must be tested regularly and the results
of these tests must be documented in
writing.
–
The heating appliance of the machine is
an ignition plant. All national laws and
regulations about heating systems must
also be followed.
–
As per the applicable national guide-
lines, the first time this high-pressure
cleaner must be taken into operation by
a skilled person. KÄRCHER has al-
ready performed this initial start-up for
you and has documented it accordingly.
The documentation can be requested at
your KÄRCHER partner. Please have
the part and plant number of the appli-
ance available when enquiring about
the documentation.
–
We would like to point out that the appli-
ance must be repeatedly checked by a
skilled person as prescribed by the ap-
plicable national regulations. Please
contact your KÄRCHER partner.
Safety devices serve for the protection of
the user and must not be put out of opera-
tion or bypassed with respect to their func-
tion.
–
While reducing the water supply at the
pump head or with the Servopress -
regulation the overflow valve opens and
part of the water flows back to the pump
suck side.
–
If the hand-spray gun is closed, so that
the whole water flows back to the pump
suck side, the pressure switch at the
overflow valve shuts down the pump.
–
If the hand spray gun is opened, the
pressure switch on the cylinder head
turns the pump back on.
The overflow valve is set by the manufac-
turer and sealed. Setting only by customer
service.
–
The safety valve opens, when the over-
flow valve resp. the pressure switch is
broken.
The safety valve is set by the manufacturer
and sealed. Setting only by customer ser-
vice.
–
The water shortage safeguard prevents
the burner to be turned on when there is
water shortage.
–
A sieve prevents the contamination of
the safeguard and must be cleaned reg-
ulary.
–
The temperature stop switches off the
machine when the waste gases have
reached very high temperatures.
Proper use
Please do not let mineral oil contaminated
waste water reach soil, water or the sew-
age system. Perform engine cleaning and
bottom cleaning therefore only on speci-
fied places with an oil trap.
Safety instructions
Safety Devices
Overflow valve with two pressure
switches
Safety valve
Water shortage safeguard
Temperature stop for exhaust gases
26
EN
Summary of Contents for HDS 7/11-4 M
Page 3: ...33 34 MIN MAX MAX MIN 35 36 37 38 39 40 41 42 43 4...
Page 4: ...2 3 4 5 6 1 2 5...
Page 5: ...7 8 9 10 11 12 6...
Page 23: ......
Page 24: ......