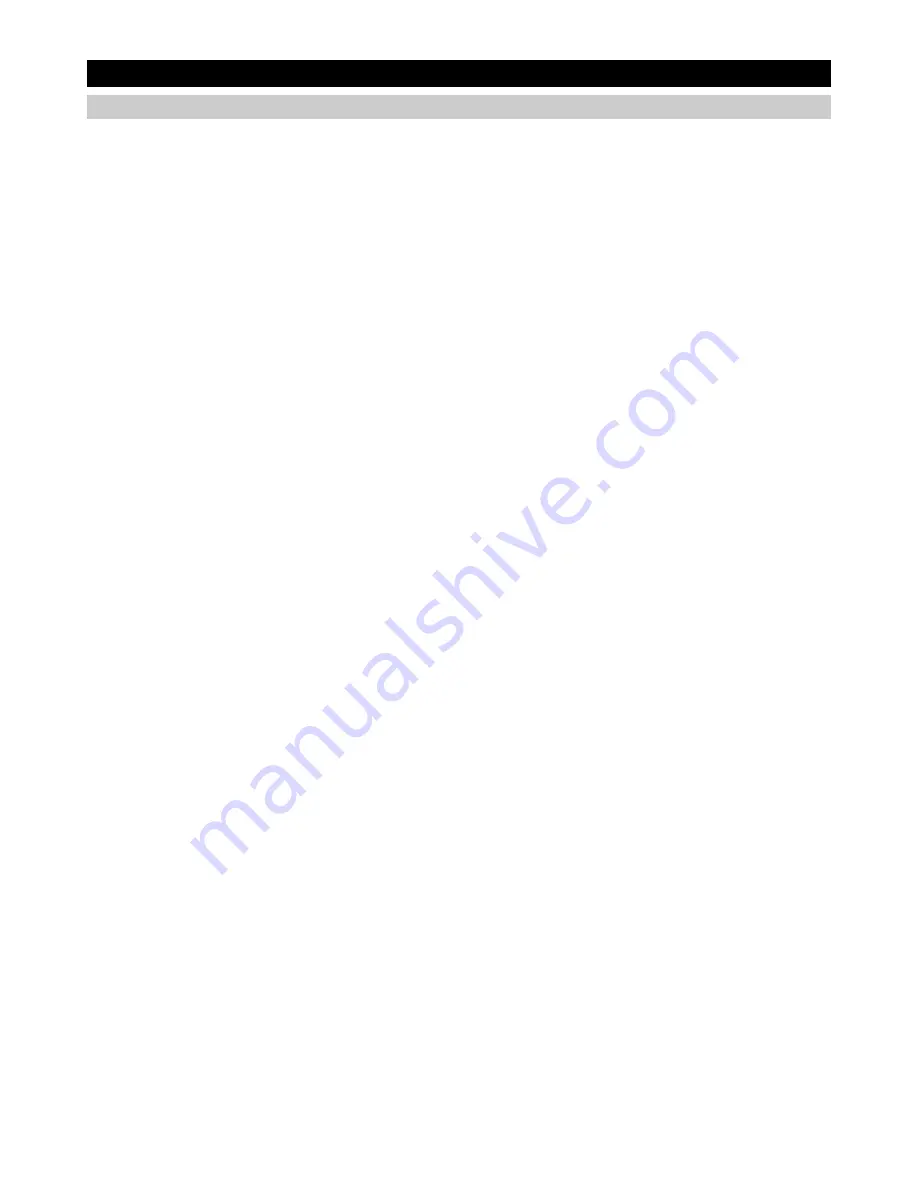
English
5.906-487.0 Rev. 00 (04/10)
39
The entire top part must be removed to perform the
following work:
–
Working on the pump
–
Working on the motor
–
Working on the electric box of the motor
–
Working on the blower
–
Working on the fuel pump
The exact explanation of the work steps is detailed in
Chapters 5.9 to 5.11.
Work steps for dismantling:
Completely remove the high pressure hose and
put it to the side.
Lay the appliance on its rear.
Reconnect the fuel hoses on the fuel tank and the
fuel pump.
Open the screw connection on the fuel line.
Set up the appliance.
Remove the exhaust temperature sensor (holding
clip).
Unplug the protective conductor cable on the
burner cover.
Unplug the ignition transformer.
Pull the detergent hose off of the pump head.
Loosen the screws on the base plate of the on-de-
mand heater (2 screws in front, 1 screw on the
right).
Remove the safety block (2 screws).
Remove the high pressure on the safety block
(holding clip).
Remove the electric box and rest it toward the
front.
Disconnect the connector of the temperature con-
trol 95°C.
Place it behind the appliance and pull the top part
a little out of the bottom part.
Lay the appliance on its rear.
Completely remove the bottom part from the top
part.
The electric box on the motor is now accessible.
Further to the removal of the pump kit, blower, fuel
pump.
Remove the motor cover (6 screws).
Remove the fuel pump.
Remove the pump kit.
Perform repairs on pump, motor, electrical sys-
tem.
Carry out a brief test run before the assembly!
Work steps for assembly:
Place the pump kit into the bottom part with all rub-
ber buffers.
Install the safety block (2 screws).
Position the motor cover with rubber buffers and
fasten it tentatively (2 screws).
Perform a brief test run (without fuel pump).
Attach the high pressure hose to the safety block
(clip), with a swivel for the U version.
After successful test run:
Remove the motor cover and the safety block (2
screws each).
Install the fuel pump with coupling.
Replace all rubber bearings.
Install the motor cover (6 screws).
Insert the bottom part onto the aluminium pipes of
the horizontally placed top part.
Position all hoses and cables properly.
Set up the appliance and let the top part slide
down into the bottom part.
Install the safety block onto the high pressure line
(2 screws).
Secure the high pressure on the safety block
(holding clip).
Make sure that the mains cables, other cables and
hoses are routed properly!
Attach the base plate of the on-demand heater (2
screws in front, 1 screw on the right).
Lay the appliance on its rear.
Connect the fuel hoses with the fuel pump and the
fuel tank.
Set up the appliance.
Insert the temperature controller 95°C.
Install the temperature sensor, protective conduc-
tor and the power supply of the ignition transform-
er.
Guide the detergent hose through the back wall
and connect it to the injector.
Insert the electric box.
UX version: Guide the high pressure hose through
the appliance, place it on the hose drum and se-
cure it (holding clip).
6
Basic settings and service procedures
6.1
Brief overview, dismantling / assembly
6.1.1 Upper section