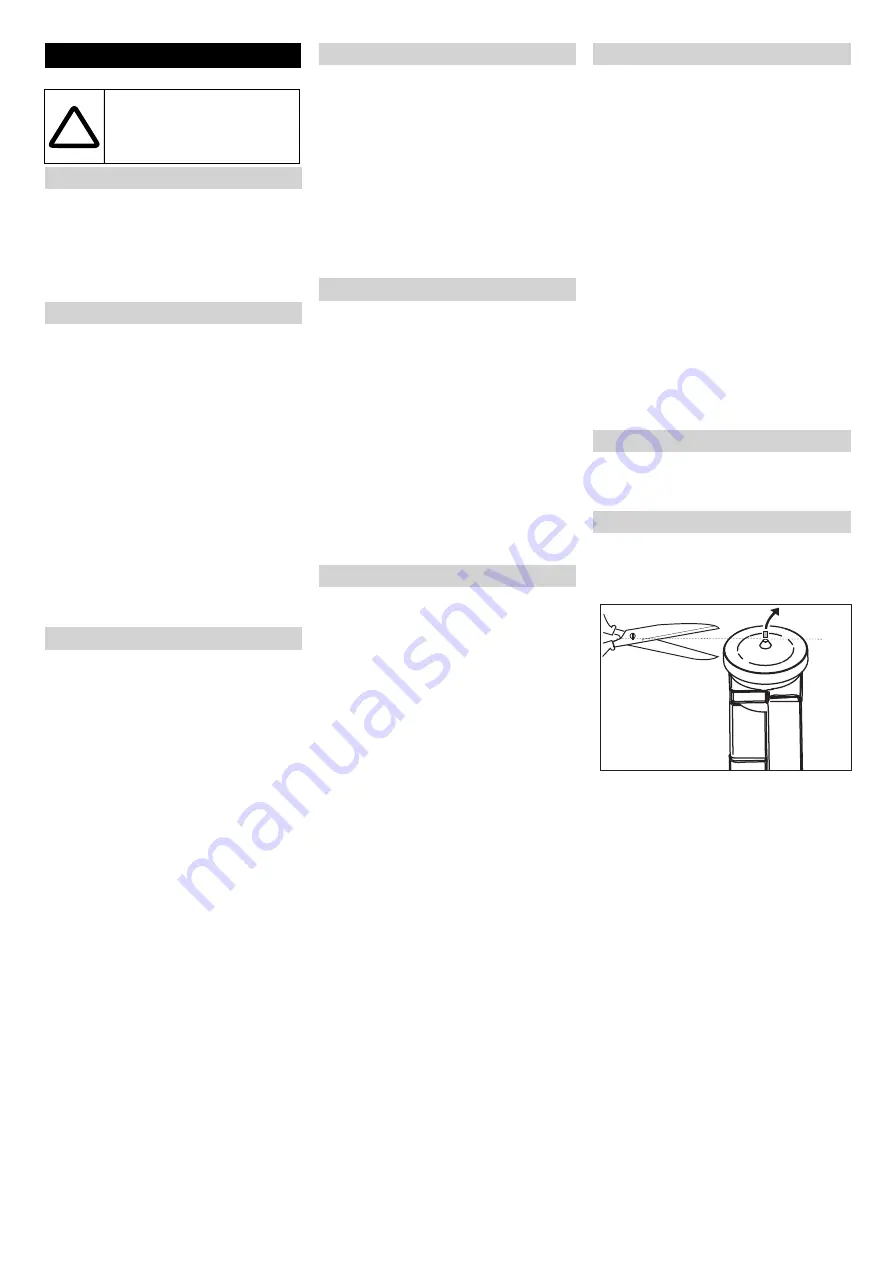
-
13
–
Check the contents of the pack before
unpacking.
–
In case of transport damage inform ven-
dor immediately
–
Store the drilling template on the carton
to assemble the device.
Note
The water connection, the high pressure
network as well as the electrical connection
can only be carried out by authorised ex-
perts in accordance with local regulations.
–
The installion should be set-up in a dry,
non-explosive environment.
–
The installion should be installed on
firm and even ground.
–
The installion should be easily accessi-
ble for maintenance work.
–
Room temperature should not exceed
40 °C.
The following are required for installation:
–
Wall mount
–
Installation with the mounting kit floor
rack (optional)
Caution
Risk of injury and damage! Note the weight
of the appliance during installation.
Risk of damage! Freezing water in the ap-
pliance can destroy parts of the appliance.
The machine should be stored in frost-free
rooms. In case there is frosting risk, for e.g.
if the machine is installed in open areas,
then the machine must first be emptied and
flushed using an anti-freezing agent.v
Check the wall's support capacity.
Mark the wall using the drill template on
the packaging.
Drill the bores into the wall.
Attach the installation materials to the
wall.
Remove the appliance cover.
Hang up the appliance and secure it
against falling down.
Replace the appliance hood and fasten
it with screws.
–
For connection values, see technical
data and type plate.
–
The power supply designed for operat-
ing the plant must be suitable for contin-
uous operations.
–
The electrical connections must be
done by an electrician according to IEC
60364-1.
–
Current-carrying parts, cables and ap-
pliances in the working area must be in-
stalled in a defectless state and must be
protected against water sprays.
–
Design the water supply for continuous
operations.
–
The water feed line is provided with a
stop valve and can be moved over a
pressure hose and attached to the high
pressure system.
–
If the cross section of the line is too
small or if the advance pressure is too
low, there will be a lack of water.
–
When the advance pressure or the
rinse pressure is too high, it is absolute-
ly necesary to install a pressure reduc-
er.
–
A water drain must be present at instal-
lation site.
For installation, please follow the specifica-
tions of the VDMA sheet 24416 "High pres-
sure cleaners; fixed high pressure cleaning
systems; concepts, requirements, installa-
tion, testing" (the German version can be
procured from Beuth Verlag, Cologne,
www.beuth.de).
–
The fixed pipe network and the install-
ion should be connected with a high
pressure line.
–
The fixed pipe network should be
placed as straight as possible. High
pressure piping systems should be in-
stalled correctly with removable and
fixed clips, taking into consideration the
variation in length caused by the effects
of heat and pressure.
–
In order to keep pressure losses in the
high pressure piping as small as possi-
ble, we recommend the following:
Pipelines: Nominal width DN 15 (1/2“).
Hose lines: Nominal width DN 8.
In regards to the above mentioned stand-
ard values, the length of the pipes and the
number of direction changes and fittings
must be taken into account.
Illustration, see "Operating components".
Mount the nozzle on the spray pipe
(markings on the adjustment ring at the
top).
Connect ray tube to hand spray gun
Lever out the safety clip of the hand
spray gun using a screw-driver (Picture
A).
Place the hand-spray gun upside down
and insert the end of the high pressure
hose till the end. Ensure that the lose
disc falls right below on the hose end
(Picture B).
Press the safety clip back into the hand-
spray gun. The hose can be pulled out
max. 1 mm if it has been installed cor-
rectly. Otherwise, it means the disc has
been installed wrongly (picture C).
Connect the high pressure hose to the
high pressure outlet of the appliance or
the high pressure pipe network.
The detergent tank is set up in such a way,
that the bottom of the tank is located not
more than 1.5 m unter the unit.
Check that water inlet has the required
flow and the permissible temperature.
Check oil level of the pump.
Cut off tip of oil container.
Installing the plant
Only for authorised techni-
cians!
Unpacking
Installation
Fasten the device to the wall
!
Electrical connection
Water supply
High pressure installation
Attaching the Accessories
Install the detergent tank
Initial startup
30
EN
Summary of Contents for HD 7/16-4 ST
Page 2: ...2...
Page 37: ...5 o K rcher Karcher CHEM 5 120 0 0 0 1 0 0 CHEM 25 37 EL...
Page 38: ...6 40 10 6 288 016 200 3 MPa 28 mm 2 Nm 29 mm 6 Nm 1000 38 EL...
Page 40: ...8 CHEM CHEM 3 40 EL...
Page 42: ...10 A 3 4 B M 22x1 5 C D E 42 EL...
Page 45: ...13 40 C IEC 60364 1 VDMA 24416 Beuth Verlag K ln www beuth de DN 15 1 2 DN 8 1 mm 1 5 m 45 EL...
Page 47: ...15 47 EL...
Page 67: ...5 I K rcher K rcher CHEM 5 120 0 1 0 I 0 1 0 0 CHEM 25 67 RU...
Page 68: ...6 40 10 6 288 016 68 RU...
Page 70: ...8 RM 81 K rcher CHEM CHEM 70 RU...
Page 71: ...9 3 71 RU...
Page 73: ...11 A 3 4 B M 22x1 5 C D E 73 RU...
Page 78: ...16 78 RU...
Page 143: ...5 I K rcher Karcher CHEM 5 120 0 1 0 I 0 1 0 0 CHEM 25 143 UK...
Page 144: ...6 40 10 6 288 016 144 UK...
Page 145: ...7 K rcher K rcher 15 1 2 MAX BGV A1 RM 100 6 287 008 200 3 28 2 29 6 1000 145 UK...
Page 146: ...8 RM 101 6 287 013 RM 100 RM 81 K rcher CHEM CHEM 146 UK...
Page 147: ...9 3 147 UK...
Page 149: ...11 A 3 4 B M 22x1 5 C D E 149 UK...
Page 154: ...16 154 UK...
Page 155: ......
Page 156: ...http www kaercher com dealersearch...