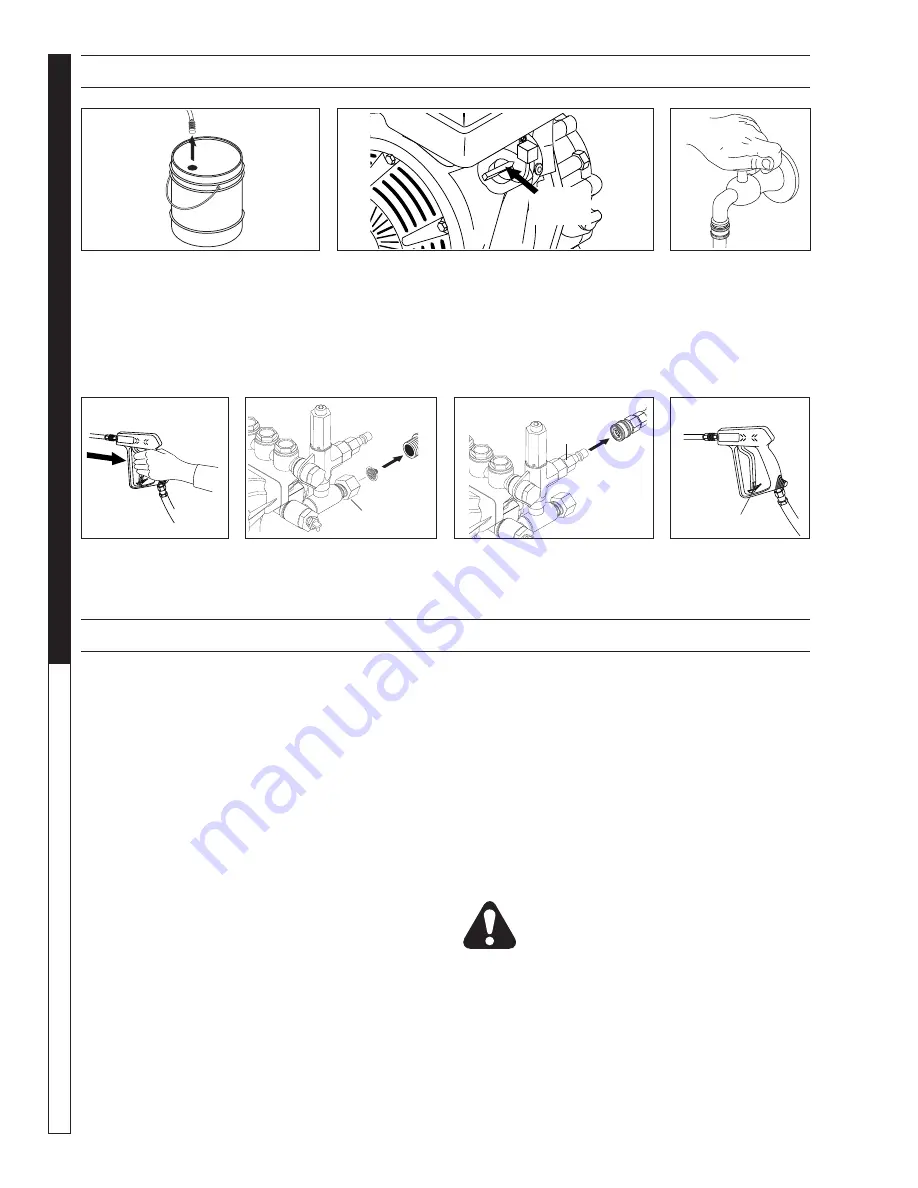
9.807-623.0 • Rev. 10/15
OPERA
T
OR’S MANU
AL
PRESSURE W
ASHER
10
SHUTTING DOWN AND CLEAN-UP
STEP 1:
Remove detergent suc-
tion tube from container and insert
into one gallon of fresh water. Slide
nozzle forward for low pressure or to
connect black detergent nozzle into
wand quick coupler. Pull trigger on
spray gun and siphon water for one
minute.
STEP 2:
Turn off the engine.
STEP 3:
Turn off wa-
ter supply.
STEP 5:
Disconnect the gar-
den hose from the water inlet
on the machine.
STEP 6:
Disconnect the high
pressure hose from high pres-
sure outlet.
S T E P 7 :
E n g a g e
the spray gun safety
lock.
STEP 4:
Press trigger
to release water pres-
sure.
CAUTION: Always store your pressure washer in a
location where the temperature will not fall below
32°F (0°C). The pump in this machine is susceptible
to permanent damage if frozen. FREEZE DAMAGE
IS NOT COVERED BY WARRANTY.
1. Stop the pressure washer, squeeze spray gun trig-
ger to release pressure.
2. Detach water supply hose and high pressure hose.
3. Turn on the machine for a few seconds, until re-
maining water exits. Turn engine off immediately.
4. Drain the gas and oil from the engine.
5. Do not allow high pressure hose to become
kinked.
6. Store the machine and accessories in a room which
does not reach freezing temperatures.
CAUTION: Failure to follow the above directions will
result in damage to your pressure washer.
When the pressure washer is not being operated or is
being stored for more than one month, follow these
instructions:
1. Replenish engine oil to upper level.
2. Drain gasoline from fuel tank, fuel line, fuel valve
and carburetor.
3. Pour about one teaspoon of engine oil through the
spark plug hole, pull the starter grip several times
and replace the plug. Then pull the starter grip
slowly until you feel increased pressure which in-
dicates the piston is on its compression stroke and
leave it in that position. This closes both the intake
and exhaust valves to prevent rusting of cylinder.
4. Cover the pressure washer and store in a clean,
dry place that is well ventilated away from open
fl ame or sparks.
NOTE:
The use of a fuel additive,
such as STA-BIL
®
, or an equivalent, will minimize
the formulation of fuel deposits during shortage.
Such additives may be added to the gasoline in
the fuel tank of the engine, or to the gasoline in a
storage container.
After Extended Storage
CAUTION: Prior to restarting, thaw out any
possible ice from pressure washer hoses,
spray gun or wand.
Engine Maintenance
During the winter months, rare atmospheric conditions
may develop which will cause an icing condition in the
carburetor. If this develops, the engine may run rough,
lose power and may stall. This temporary condition can
be overcome by defl ecting some of the hot air from the
engine over the carburetor area.
NOTE:
Refer to the
engine manufacturer's manual for service and main-
tenance of the engine.
STORAGE
Pump Water
Inlet
High Pressure
Outlet
Safety Latch
On-Off
Switch