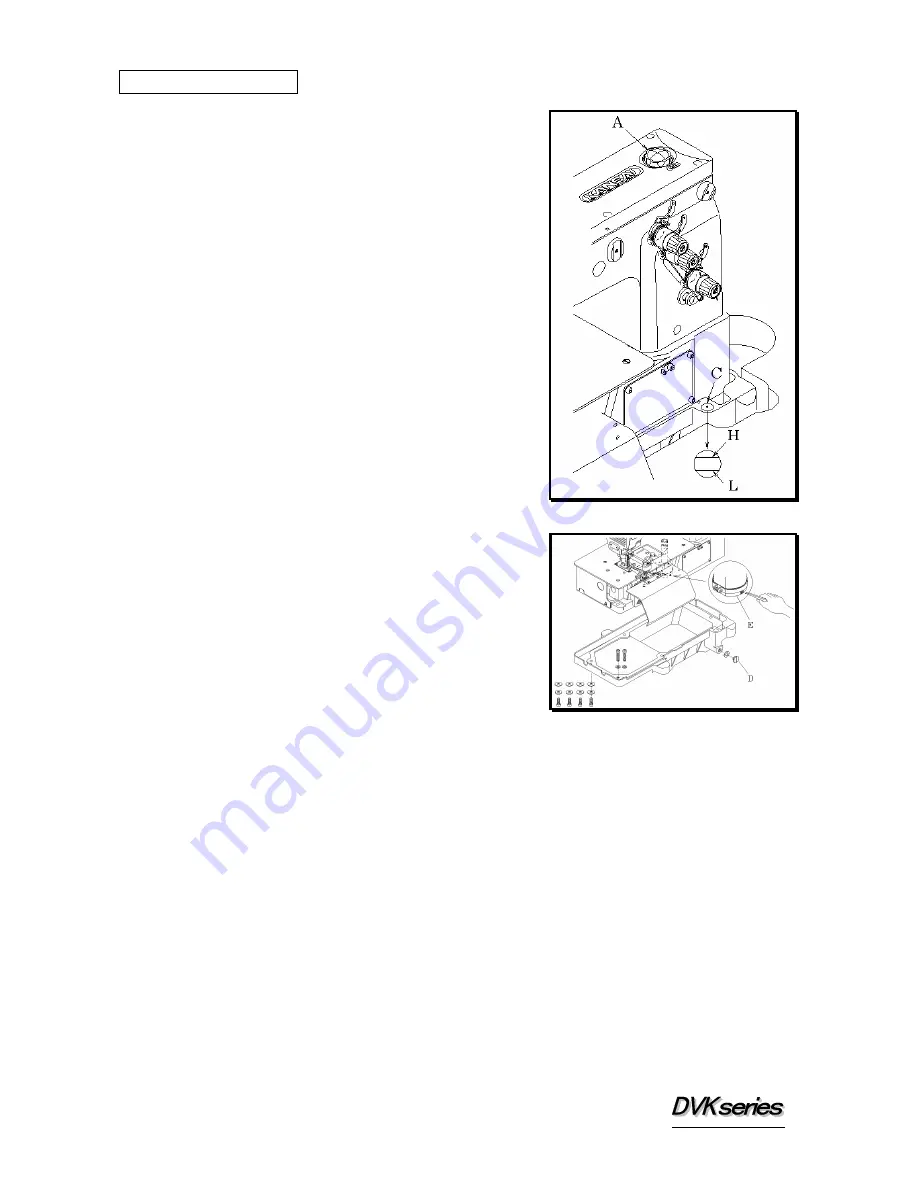
【
3
】
LUBRICATION
3-1 Oil
Use Kansai Special’s genuine oil.
(Part No. 28-611)
3-2 Oiling
■
To fill the machine with oil
Remove oil plug A from the oil hole.
Fill the machine with oil until the oil level is at the
top line (see H in the illustration) on oil gauge C.
After the first lubrication, add oil so that the oil
level will be between H and L.
■
To check for proper oil flow
After filling the machine with oil, run the machine
to check the oil is splashing from oil pipe outlet B.
3-3 Replacing the oil and the filter element
To extend machine life, be sure to replace the oil
after the first 250 hours of operation.
To replace the oil, follow the procedures below.
1.
Remove the V belt from the motor pulley and
then remove the machine from the table.
2.
Remove screw D and then drain the oil.
Be careful not to stain V belt with the oil.
3.
After draining the oil, be sure to tighten screw
D.
4.
Fill the machine with oil by referring to 3-2
shown above.
If filter element E is contaminated, proper oiling may not be performed.
Clean the filter element every six months. If just a little or no oil flows out from the
nozzle with the proper amount of oil in the machine, check the filter element.
To clean the filter element, remove oil reservoir.
3