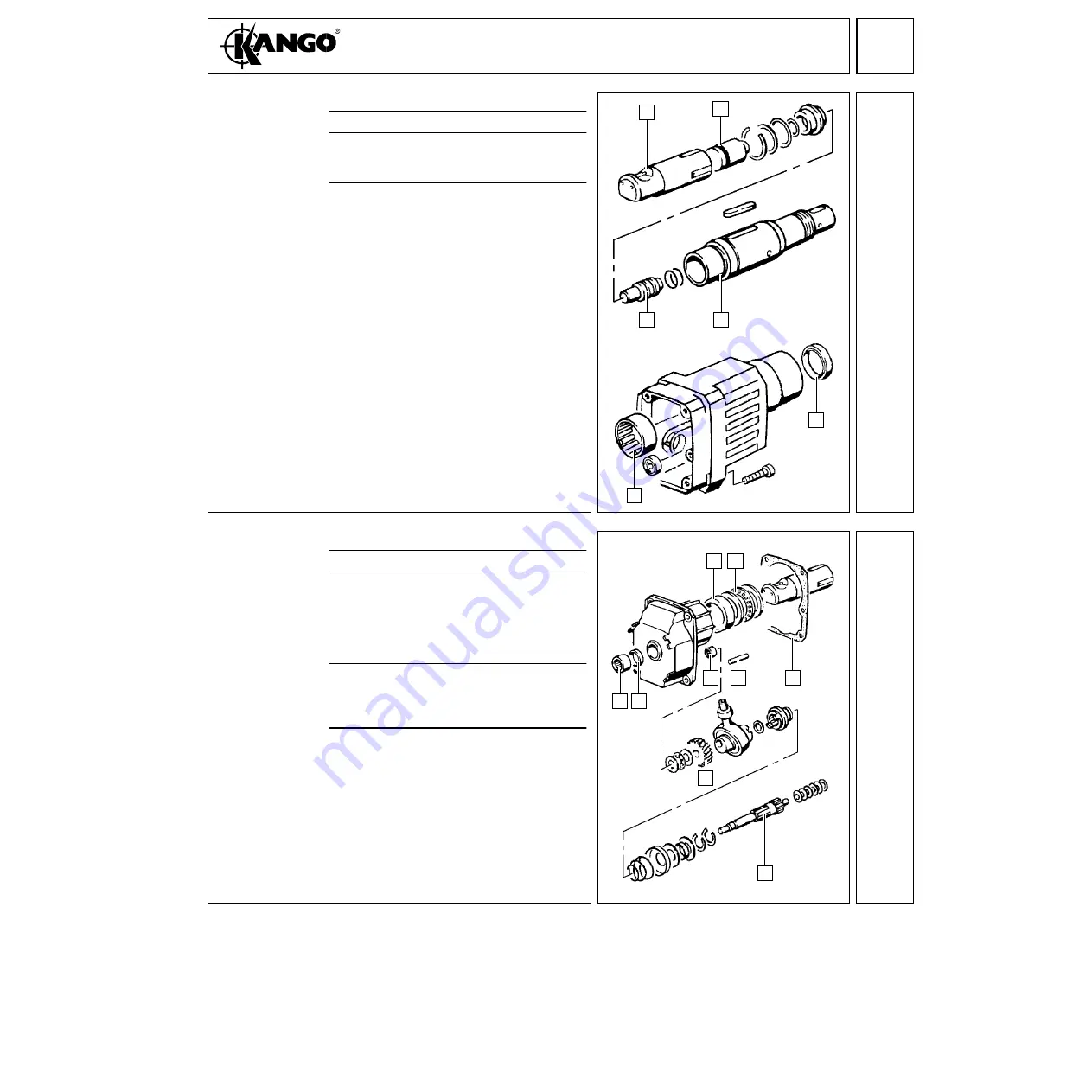
6
PAGE
Repair Instructions
K 200
Mounting the
cylinder
1
Mount the needle bearing (1).
2
Insert the sealing ring (6).
3
Insert the snap die (2), the rubber ring, the
washer,the spring ring, and the drill spin-
dle (5).
4
Insert the cylinder (3) as shown in illustra-
tion. Insert the percussion body (4) into
the cylinder (3).
Assembling the
reduction gear
1
Mount the bearing (3) and the gasket (5).
2
Insert the pin (6) and the sleeve (7).
3
Mount the sealing ring (1) and the needle
bearing (2).
☞
Press the reduction gear wheel (9)
onto the wobble gear drive. The end
play must be 0.05 + 0.03 mm.
4
Mount the reduction gear complete with
the reduction gear shaft (8). Insert the disc
springs opposite each other (see illustra-
tion).
5
Mount the axial needle bearing (4).
3
6
1
2
5
4
3
1
3 4
5
6
9
7
8
2
4
Summary of Contents for K 200
Page 1: ......