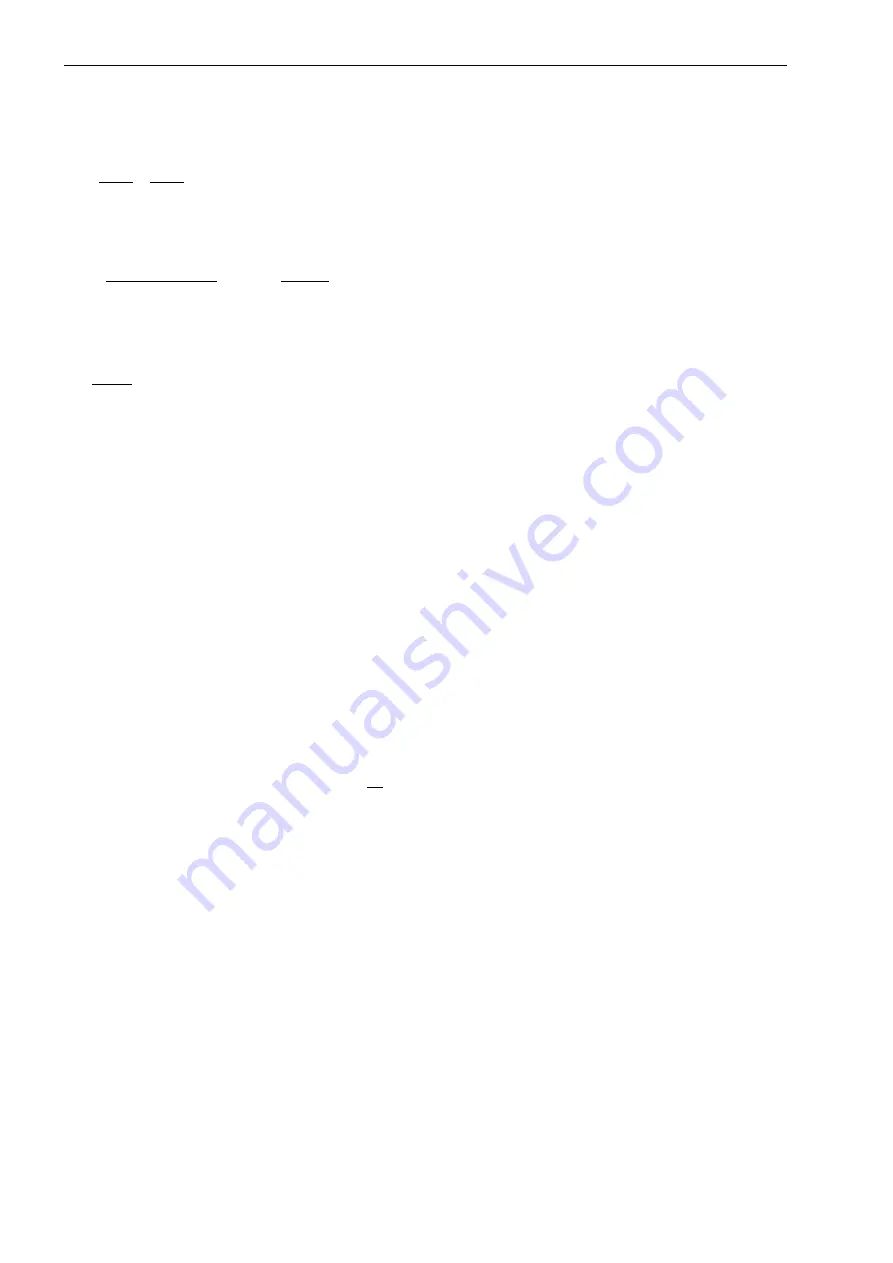
TECHNICAL DESCRIPTION
ULTRAFLOW® 54 DN150-300
Kamstrup A/S
·
Technical description
·
5512-876_M1_GB_12.2020
34
The transit time difference can be expressed as the difference between the absolute time of the signal sent against the
flow (-) and the signal sent with the flow (+).
∆𝑡 =
𝑙
𝑐 − 𝑣
−
𝑙
𝑐 + 𝑣
which can also be written as:
∆𝑡 = 𝑙
(𝑐 + 𝑣) − (𝑐 − 𝑣)
(𝑐 − 𝑣) ∙ (𝑐 + 𝑣)
⇒ ∆𝑡 = 𝑙
2𝑣
𝑐
2
− 𝑣
2
As
𝑐
2
≫ 𝑣
2
,
𝑣
2
can be omitted and the formula reduced as follows:
𝑣 =
∆𝑡 ∙ 𝑐
2
2𝑙
Thus, we know the basic connection between the average flow velocity and the transit time difference.
The transit time difference in a flow sensor is very small (nanoseconds). Therefore, the time difference is measured as a
phase difference between the two 1 MHz sound signals in order to obtain the necessary accuracy.
Furthermore, the influence of the temperature of the sound velocity of water must be taken into account. In
ULTRAFLOW®, the velocity of ultrasound
𝑐
is measured by means of a number of absolute time measurements between
the two transducers. As the geometry of the flow sensor is known, the measured speed of the ultrasound is thus a scale
for the water temperature, which is further used in the built-in ASIC in connection with the flow calculations.
The flow (volume flow rate) is then determined by measuring the transit time difference, calculate the average flow
velocity and multiply it by the area of the measuring tube:
𝑞 = 𝑣 ∙ 𝐴
where:
𝑞
is the flow (volume flow rate).
[
𝑚
3
ℎ
]
𝐴
is the area of the measuring pipe.
[𝑚
2
]
The volume
𝑉
passing through is finally calculated as a time integration over the flow (multiplication of (cross section
constant) flow by time).
The calculation above is simplified since it does not take into account the flow profiles. In general, flow profiles influence
the measurement, which in our case is the transit time difference. Flow sensors are thus adjusted properly according to
the different Reynolds numbers that characterize the flow, i.e. in practice for different flows (volume flow) and
temperatures. To cover the various flow profiles in the best possible way with the ultrasound signal, Kamstrup uses a
triangle sound path, as illustrated in
from two perspectives, for large ULTRAFLOW® 54 flow sensor (q
p
3.5…100
m
3
/h) and ULTRAFLOW® 34 (q
p
2.5…100 m
3
/h).