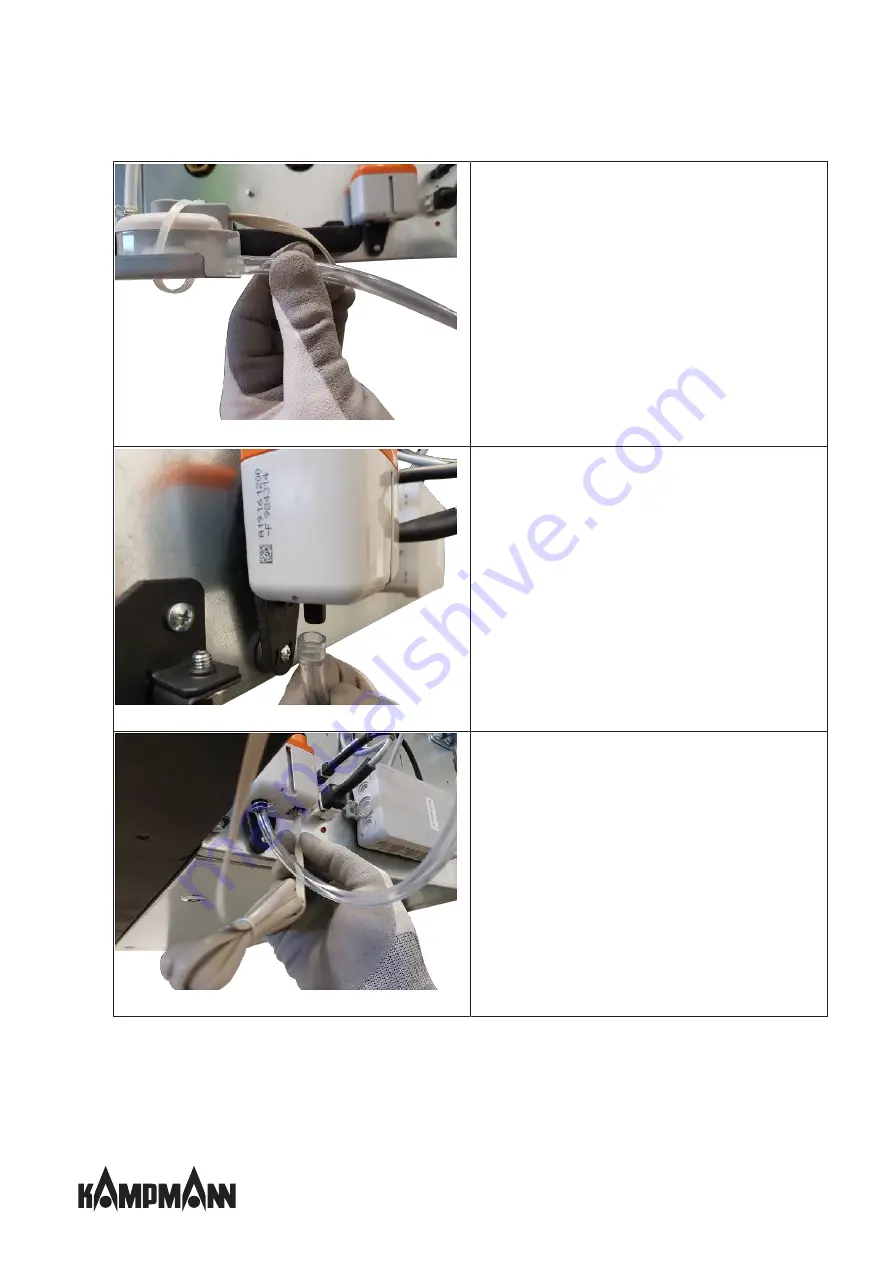
Venkon XL
Beschreibung
Assembly, installation and operating instructions
30
Fig. 27: Connecting the suction hose
Attach 2 no. 10.1 mm wire clamps to a 6x1.5 mm PVC hose
(length = 400 mm) and attach the hose to the float switch.
Fig. 28: Attaching the suction hose
Attach the suction hose to the pump.
Fig. 29: Inserting the signal cable into the float switch
Insert the signal cable from the float switch into the condens-
ation pump.
Summary of Contents for Venkon XL
Page 2: ......
Page 5: ...5 13 2 ERP Datenblatt Venkon XL 70...
Page 67: ...Venkon XL Beschreibung Assembly installation and operating instructions 67 13 Certificates...
Page 73: ......
Page 74: ......
Page 75: ......
Page 76: ...www kampmanngroup com hvac products fan coils venkon xl 02 20 ENSAP Nr 1374732...