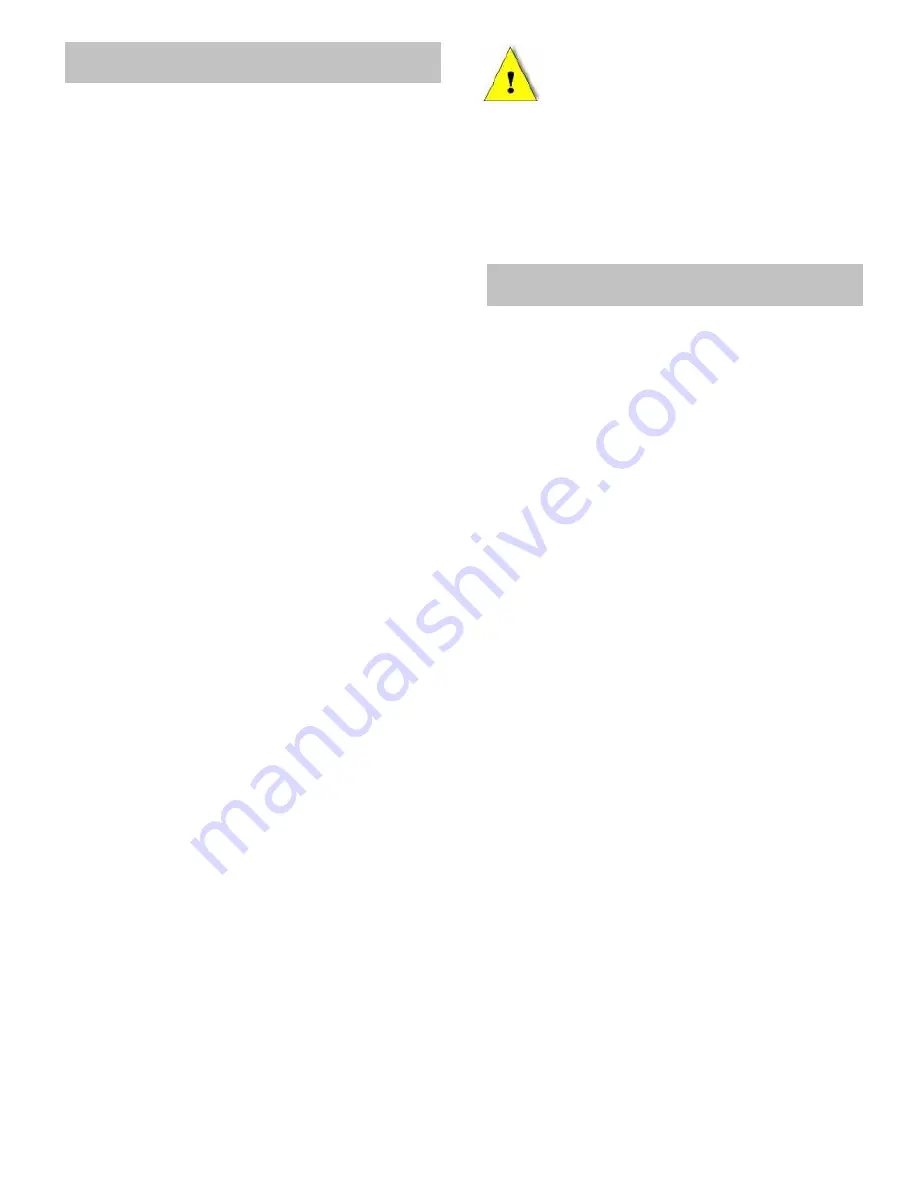
8. Maintenance
The cautionary assessment of the work space and its
arrangement establish an indispensable safety
relation between placement, operation, emergency
operations and surrounding environment. It is
recommended observing them from the preliminary
steps to the cutting step.
"
It is strictly forbidden
to place and/or use the
saw when environmental conditions constitute a
hazard of explosion or fire.
"
It is forbidden to use the machine for any
purpose other than that intended by the
manufacturer.
"
Make sure that operation of the saw does not
create hazardous a situation for people and/or
property.
"
Should you encounter a malfunction, stop the
machine immediately and check the reason for
and/or extent of the breakdown. Contact the
authorized Technical Service if necessary.
"
It is strictly forbidden
to exceed the cutting
capacity stated by the manufacturer.
"
Make sure that the operating unit head is aligned
with the graduate scale (F -fig. 1) according to
the selected cutting angulation.
"
Check that all the adjusting levers (grips) are
correctly locked.
IT IS ABSOLUTELY FORBIDDEN:
"
to lubricate the blade (saw) before/during/after
cutting;
"
work without the blade guide installed and
positioned properly;
"
work without the rear guard of the operating
head;
"
hold the piece to be cut by hand;
"
open, close or choke the cooling liquid (through
the two taps (6 - fig. 1) during the cutting
operation;
"
leave the machine with the electrical voltage
turned on.
IT IS STRICTLY NOT RECOMMENDED:
"
stopping the machine with the blade inserted in
the piece to be cut;
"
varying the cutting speed during sawing.
8.1 Ordinary Maintenance
Ordinary maintenance operations can be performed
by the normal maintenance personnel.
AT THE END OF EACH JOB:
"
Clean any machine part thoroughly, removing
chips and other processing waste, in particular in
the blade guide, in the clamp jaws and on the
metal net (filter) (4 - fig. 4) of the cooling liquid
tank cover (3).
"
Clean the working area thoroughly too (next to
the sawing machine).
For cleaning do not use compressed air jets, but use
the panel and industrial aspirator.
EVERY 40 WORKING HOURS:
"
Check that all screws which are important from a
mechanical viewpoint, are properly tightened.
7.2 Replacing the Cooling Liquid
The loss of the cooling liquid’s original properties,
is a condition which is difficult to assess. Thus, it is
recommended to replace it periodically at scheduled
intervals or when it is very “dirty” or saturated with
impurities.
Record any replacement on a maintenance schedule
card with date and signature.
To replace the cooling liquid, act as follows:
"
Remove the cover/filter (3 - fig. 4);
"
Take a container with appropriate capacity and
position it under the drain plug (5);
"
Remove the drain plug (5) and let all the liquid
in the container flow down;
"
Once the tank has been completely emptied, if
necessary, rinse it with water;
7. Caution
The manufacturer shall not be held
liable:
for damage of any type or entity caused
by irrational use of the machine, failure
to observe the safety rules indicated in this
manual or superficial observance thereof, as well
as changes or tampering with the machine,
however slight. These actions shall also
invalidate all warranty coverage.