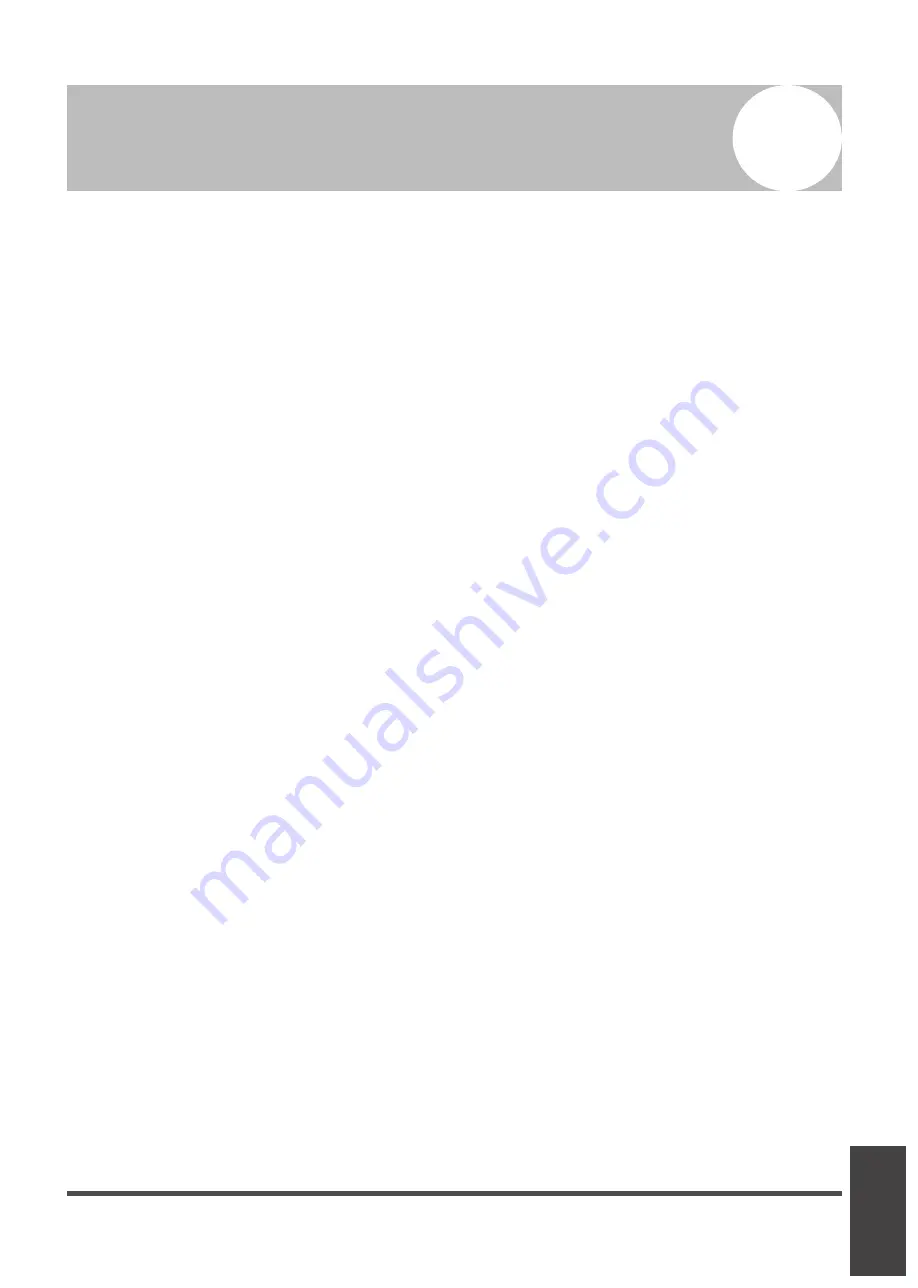
Page 31
12
1. Checks to the area
3. General work area
4. Checking for presence of refrigerant
5. Presence of fire extinguisher
If any hot work is to be conducted on the refrigeration equipment or any associated parts, appropriate
fire extinguishing equipment shall be available to hand. Have a dry power or CO2 fire extinguisher
adjacent to the charging area.
7. Ventilated area
Ensure that the area is in the open or that it it adequately ventilated before breaking into the system
or conducting any hot work. A degree of ventilation shall continue during the period that the work is
carried out. The ventilation should safely disperse any released refrigerant and preferably expel it
externally into the atmosphere.
8. Checks to the refrigeration equipment
Where electrical components are being changed, they shall be fit for the purpose and to the correct
specification. At all times the manufacturer s maintenance and service guidelines shall be followed.
If in doubt consult the manufacturer s technical department for assistance. The following checks shall
be applied to installations using flammable refrigerants:
6. No ignition sources
No person carrying out work in relation to a refrigeration system which involves exposing any pipe
work that contains or has contained flammable refrigerant shall use any sources of ignition in such a
manner that it may lead to the risk of fire or explosion. All possible ignition sources, including cigarette
smoking, should be kept sufficiently far away from the site of installation, repairing, removing and
disposal, during which flammable refrigerant can possibly be released to the surrounding space. Prior
to work taking place, the area around the equipment is to be surveyed to make sure that there are
no flammable hazards or ignition risks. NO SMOKING signs shall be displayed.
2. Work procedure
All mintenance staff and others working in the local area shall be instructed on the nature of work
being carried out. work in confined sapces shall be avoided. The area around the work space shall
be sectioned off. Ensure that the conditions within the area have been made safe by control of
flammable material.
Prior to beginning work on systems containing flammable refrigerants, safety checks are necessary
to ensure that the risk of ignition is minimised. For repair to the refrigerating system, the following
precautions shall be complied with prior to conducting work on the system.
Works shall be undertaken under a controlled procedure so as to minimise the risk of a
flammable gas or vapour being present while the work is being performed.
The area shall be checked with an appropriate refrigerant detector prior to and during work,
to ensure the technician is aware of potentially flammable atmospheres. Ensure that the leak
detection equipment being used is suitable for use with flammable refrigerants, i.e. no sparking,
adequately sealed or intrinsically safe.
,,
,,
,
,
Information
Servicing
Information Servicing
(Required for the units adopt R32/R290 Refrigerant only)