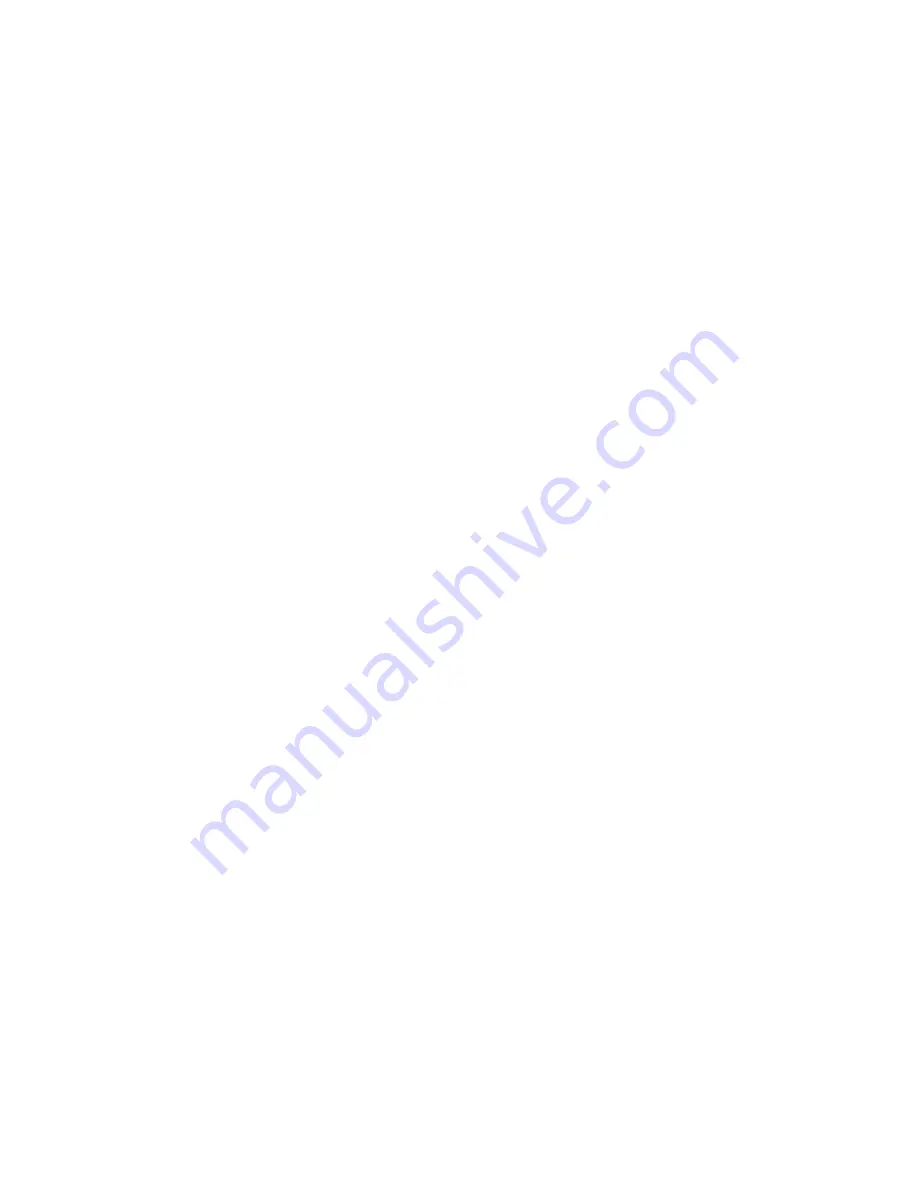
KTI63619
3
rev. 09/04/14
ASSEMBLY INSTRUCTIONS
PLEASE REFER TO THE EXPLODED VIEW DRAWING IN THIS MANUAL IN ORDER TO IDENTIFY PARTS.
1) Loosely assemble the upper beams #10 to the post #20 at one end with the bolts #9, washers #11, spring washers #12 and nuts #13 as
shown in the exploded view drawing. Slide the ram plate #7 on the beams #10. Loosely assemble the other ends of the upper beams #10
to the other post #20. All hardware will be tightened at a later time.
2) Place the lower cross member #26 between the two posts #20 so the holes at either end of the cross member line up with the holes in
the bottom of the posts. Align the holes in the feet #21 with the same holes in the bottom of the posts #20 as shown in the exploded view
drawing. Secure the feet, posts and lower cross member together using the bolts #25, washers #22, spring washers #23 and nuts #24.
3) The four supports #37 are used to keep the posts #20 perpendicular to the feet #21 when installed.
Install one end of the supports #37 to the holes in the posts #20 with the bolts #36, washers #14, spring washers #15 and nuts #16. Do
not tighten until later. Install the other ends of the supports #37 to the feet #21 with the same hardware #36, #14, #15 and #16.
4) Tighten all hardware mentioned in steps 1 through 3 making sure the feet #21 are flat on the floor and posts #20 are perpendicular to the
floor.
5) Secure the pump assembly plate #31 to the post #20 with the bolts #39, washers #22, and nuts #24 as shown in the exploded view
drawing. The oval hole in the pump assembly plate #31 should face towards the operating side of the press.
6) The pump #32 must be secured to the pump assembly plate #31 with the washers #30 and bolts #29.
7) Screw the upper round nut #6 all the way on the threads of the ram assembly #3. Insert the end of the ram #3 through the hole in the ram
plate #7 until the upper round nut #6 rests on top of the ram plate #7.
8) The threads of the ram assembly #3 should be exposed below the ram plate #7. Screw on the lower round nut #8 on the ram threads just
until the nut engages all the threads. Raise the ram up until the top of the lower round nut #8 is up against the bottom of the ram plate #7
and then screw down the upper round nut #6 until plate #7 is sandwiched between the upper and lower round nuts. Tighten set screws in
the upper and lower round nuts.
9) Insert the nylon ring #2 in the fitting on top of the ram assembly #3 and install the gauge #1 in the fitting. Tighten the gauge in the fitting so
the face of the gauge is pointing towards the operating side of the press.
10) Install the coupler at the end of the oil hose #35 in the coupler of the ram assembly #3 and tighten by hand only.
11) Install the adaptor #5 in the bottom of the ram assembly #3 and tighten the screw #4.
12) Tilt the work bed #18 so that each end will straddle the posts #20. Raise the work bed to the desired height and closest to the holes in
the posts #20. Insert the pins #19 through the holes in the posts #20 and secure the pins in the holes by inserting the rings #38 in the ring
grooves of the pins #19. The work bed #18 can now rest on the pins #19.
13) If the back end of the pump #32 is equipped with a fill screw that also serves as a breather for the pump’s reservoir, turn the screw
counterclockwise until it stops.
14) Sometimes during shipping and handling, air may become trapped in the hydraulic system and cause the pump to malfunction or not
achieve a full pump stroke. Purging air out of the system can be accomplished by following these steps:
a. On the side of the pump #32 is a knob that must be turned clockwise all the way until it stops in order to extend the ram #3 during the
pumping operation. Turn the knob counterclockwise two full rotations from its stop position. Install the pump handle #33 in the pump’s
handle receiver and operate the pump 10 full incremental pump strokes.
b. Repeat step 'a' until all the air is purged out of the system.
INSPECTION
Visual inspection of the shop press should be made before each use of the press, checking for damaged, loose or missing parts.
Each press must be inspected by an authorized service center immediately if subjected to an abnormal load or shock. Any press
which appears to be damaged in any way, is found to be badly worn, or operates abnormally must be prevented from being used until
necessary repairs are made by an authorized service center. It is recommended that an annual inspection of the press be made by an
authorized service center and that any defective parts, missing or damaged warning labels be replaced with K-Tool International parts
and labels.