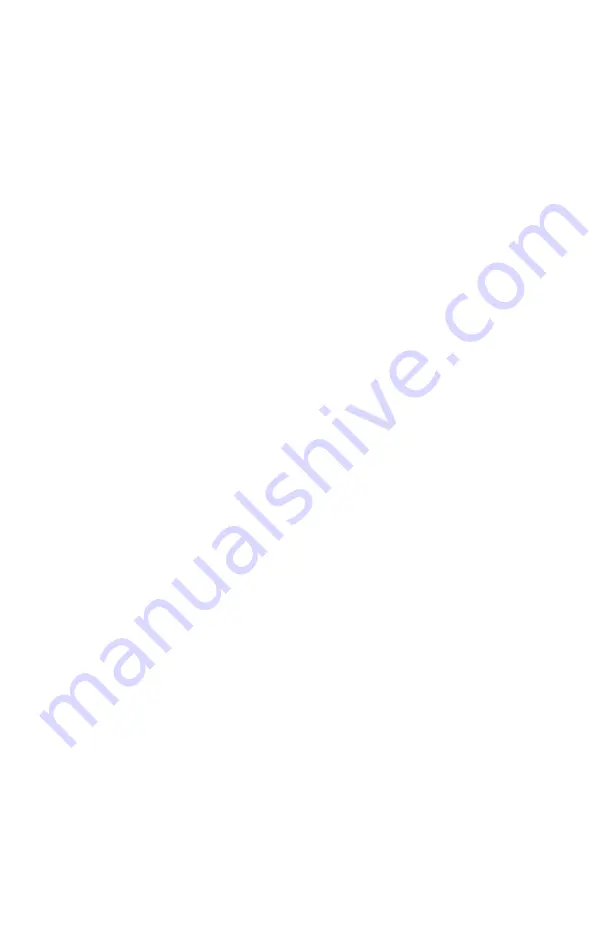
Instruction Manual Glossary of Terms
centers. A principal part of the engine lathe used for supporting the ends of work-
pieces by means of a center point held in the spindle. May be moved along the
ways and clamped in different positions and offset from the true axis of the lathe
for turning tapers.
Tangent:
A line that touches the circumference of a circle at one point only.
Tap:
A hardened and tempered steel tool for cutting internal threads which has
flutes lengthwise to provide cutting edges for the threads and a square at the end
of the shank for turning the tap with a wrench.
Taper:
A piece of work which increases or decreases uniformly in diameter or size
and assumes a conical or wedge shape.
Tapered
Wheel: A grinding wheel shaped similarly to a straight wheel but having
a taper from the hub of the wheel to the face and thus being thicker at the hub
than at the face.
Taper Per Foot:
A means of specifying the amount or rate that a taper increases
or decreases for each foot of length, usually stated in inches per foot.
Taper Reamer:
A fluted reamer which has the cutting ends made to the standard
taper it is designed to cut. The taper reamer is used either for roughing or finish
ing taper holes to size by hand or power according to the design of the reamer.
Roughing reamers have notched teeth to relieve the load on the teeth.
Taper Taps:
One of the three taps in a set of hand taps. The end threads are
tapered or chamfered back for a length of 8 to 10 threads for easy starting.
T-Bolt:
A threaded bolt having a square or rectangular end which fits into the T-slot
of a machine table for clamping workpieces.
Teeth:
Molded organic bonded abrasive segment for insertion in the periphery of a
steel disc. Also, cutting segments or flutes of a milling cutter.
Temper:
The heat treatment of a material to develop required qualities.
Tensile Strength:
The strength of a material when tested in tension usually given
in pounds per square inch.
Tolerance:
The permissible deviation from a basic dimension.
Tool Bit:
A piece of high-speed steel, usually square in shape and of suitable length,
which may be ground to various shapes and forms for single-point cutting tools
that are used in lathes, shapers, and planers for cutting metal.
Toolroom: Area or department where tools, jigs, fixtures and dies are manufactured.
Truing:
A grinding wheel is trued in order to restore its cutting face to running
truth so that it will produce perfectly round (or flat) and smooth work; or to
alter the cutting face for grinding special contours.
Universal Chuck:
A chuck on which all jaws move simultaneously at a uniform
rate to center round or hexagonal stock automatically.
Universal Grinding Machine:
A machine such as the K. 0. Lee Universal Tool and
Cutter Grinder on which cylindrical, internal and surface grinding can be done —
usually used for tool room work. It consists of a swivel table, headstock, tailstock,
and a Wheelhead that can be rotated 360 degrees on its base and raised or lowered.
It is also used for tool and cutter grinding with the addition of various fixtures.
- 1 2 6 -