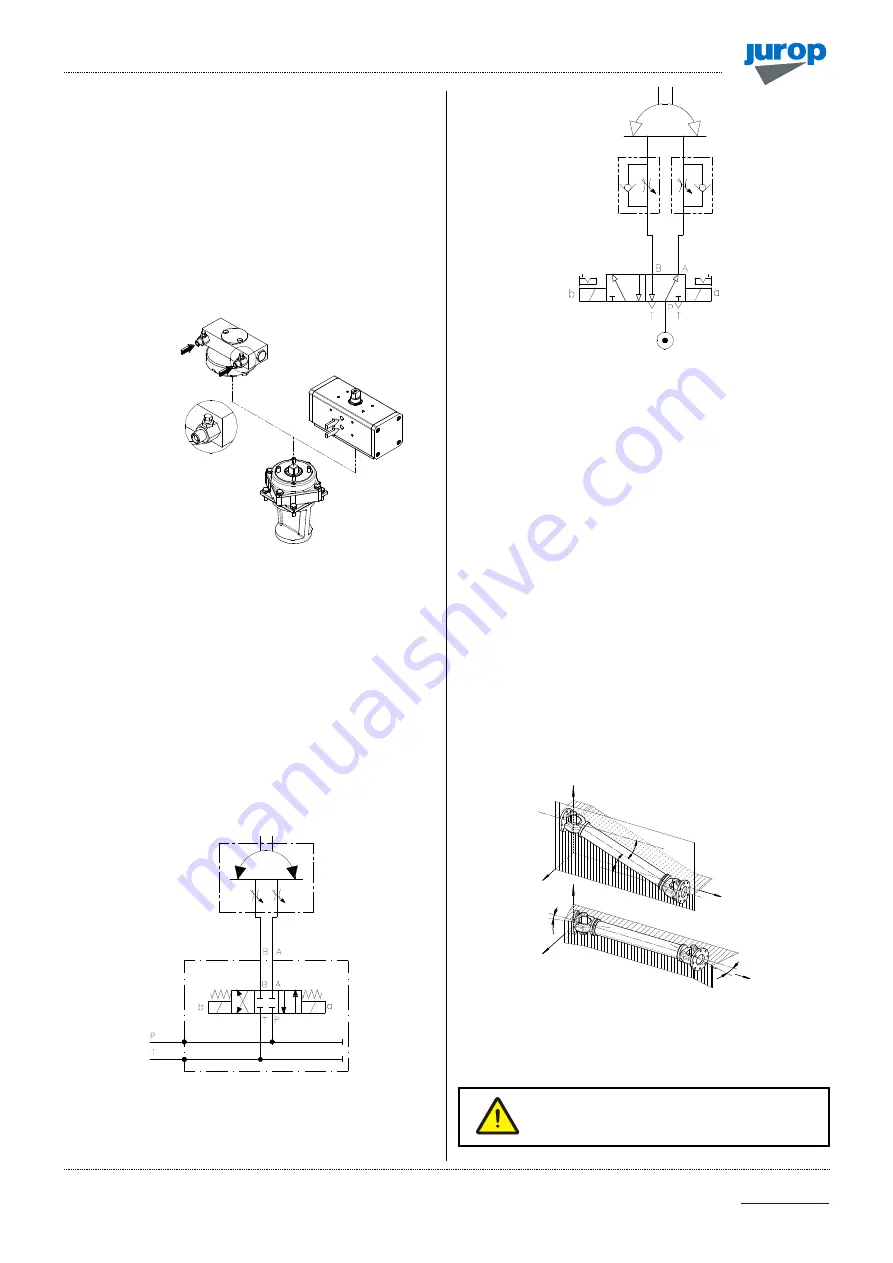
REV
.
04
02-12-2019
INSTALLATION
,
USE AND MAINTENANCE MANUAL
–
PNR/E 73-83-104-124
–
PNR 142
13 / 44
Jurop
SpA
Via Crosera n° 50
33082 Azzano Decimo, PN (Italia)
T
EL
.
+39
0434
636811
F
AX
.
+39
0434
636812
http://www.jurop.it
e-mail: [email protected]
α
α
1
α
α
1
Pneumatic actuator installation
• Adjust movement speed by applying two unidirectional flow control
valves.
For both actuators
• Adjust speed: full rotation should not take less than 1 second.
• Fluid filtration: ensure a level equal to or greater than the
recommended value.
• In the event of a (hydraulic or pneumatic) supply failure, the
suction unit inverter will remain in the same position it was when the
failure occurred.
Pic. 4.5
Maintenance
• The diverter is adjusted before shipment and does not usually
require further adjustments.
•
Diverter lubrication:
-
Use Lithium grease NLGI 2. Quantity: 50 g every 1000 work
cycles.
-
Do not grease using excessive amounts of grease.
•
Hydraulic actuator: the control valves are equipped with an internal
metal filter. Disassemble and clean if movement stops.
• Pneumatic actuator: for non-dried air, use temperature 0 ÷ +80°C.
• The following figure shows a possible schematic view of a correct
hydraulic connection.
•
The following figure shows a possible schematic view of a
pneumatic connection.
• In case of interruption of the pneumatic or hydraulic supply, the
inverter of the suction unit remains in the same position it was when the
failure occurred.
4.9.
Pump mounting - drive connection
• For the machines of this series, the allowed power transmissions
are
-
Direct transmission (e.g.: from agricultural cardan shaft)
-
Oil hydraulic transmission (HDR)
• Protect with a fixed or interlocked guard and signal with
pictograms the power transmission chosen and applied by the final
installer, if there is the possibility that the operator will come into
contact during handling.
A) Cardan shaft drive
• Use telescopic cardan shafts.
• In order to achieve a uniform motion of the driven shaft, the
following requirements must be met (see Pic. 4.6):
- Equal working angle α and α1 of both couplings;
- The internal fork joints must be coplanar;
- Both driven and driving shafts must be coplanar.
Pic. 4.7
• It is also recommended working with limited articulated joint angles
(max 15°) and disengaging the transmission for those operations
requiring great angles (steering or lifting).
Follow the rotation direction as indicated on the
pump front conveyor protection. Follow the
instructions of the cardan shaft’s manufacture.
HYDRAULIC
ACTUATOR
SPEED ADJUSTMENT