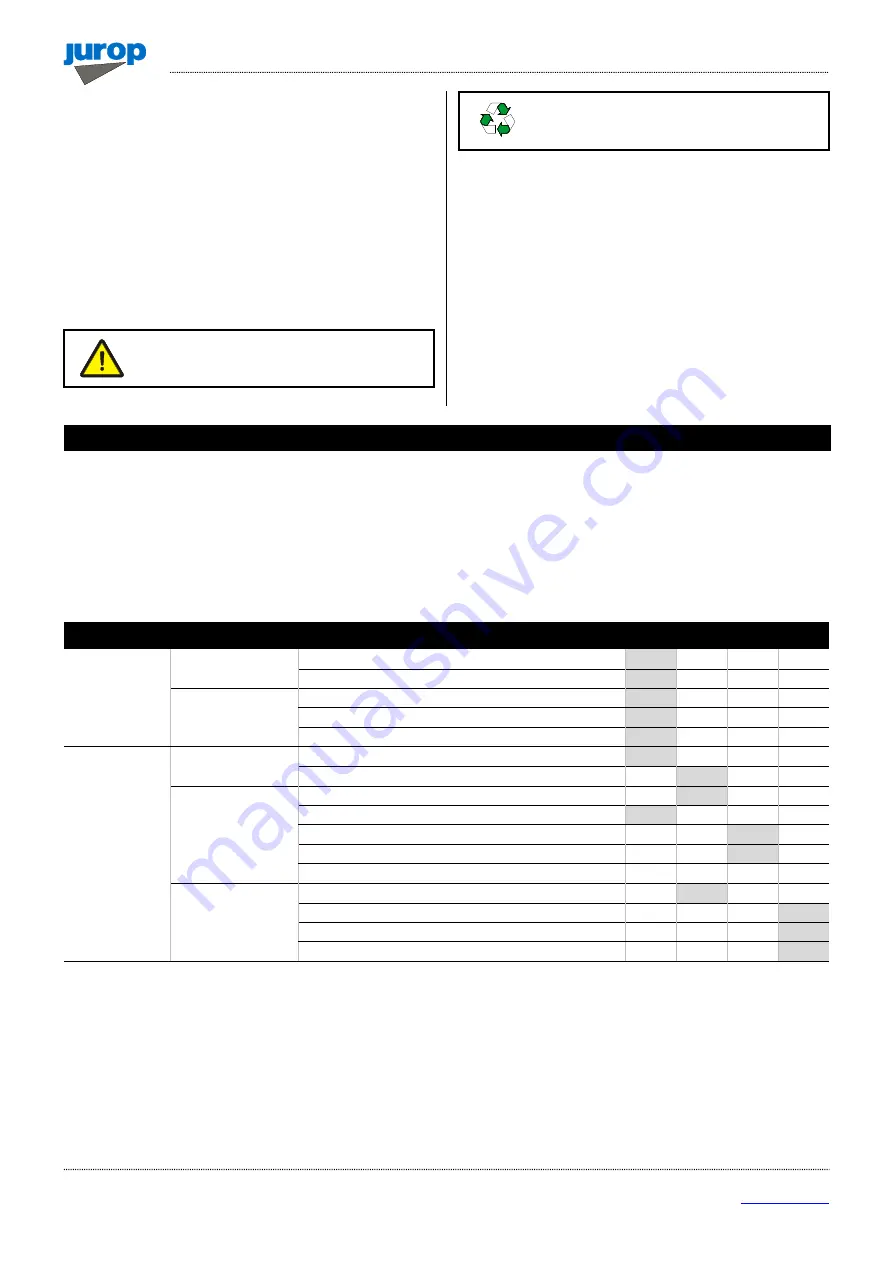
REV
. 10
22-04-2020
INSTALLATION
,
USE AND MAINTENANCE MANUAL
–
PN
16 / 40
Jurop
SpA
Via Crosera n° 50
33082 Azzano Decimo, PN (Italia)
T
EL
. +39 0434 636811 F
AX
. +39 0434 636812
http://www.jurop.it
e-mail: [email protected]
preventing oxidation. When the detergent mix is finished, continue
running the pump at the lo west possible vacuum rate for a few
minutes, then close venting and suction valves up to 50-60%
maximum, for a couple of minutes. With this operation the pump will
dry from the heated air and protected from the chemical attack of
the detergent.
7.
Washing the pump with this detergent guarantees a protection after
some days of inoperativity. If the pump is not used for more than
two weeks, after having washed and dried the inner parts as
described above, it is recommended to suck slowly 200 cc anti-rust
and water-repellent protective oil (or, if not available, a very fluid
gear oil).
Attention: do not carry out also this operation on
very hot pumps (for example after a working day)
until they have cooled down.
In case the exhaust line cannot be disconnected,
drain the liquids accumulated in the separator of
the exhaust silencer.
• Do not convey the exceeding flow outlet towards the suction port.
• Control the air flow by adjusting the rotation speed: do not use the
safety relief valve to discharge the exceeding flow.
• Do not squeeze the hoses/pipes.
• If the decompressor operates in vacuum or under pressure with a
capacity environment (such as a cistern) and is configured in the “FL”
flanged version (without manifold with 4-way valve and non-return vale),
it is advisable to intercept the working line of the machine when it is
stopped, to prevent contrary rotations until the rebalancing of the
pressures. The interception can take place through a controlled valve or
an automatic unidirectional valve (swing valve).
• Avoid starting the pump under load: motor and drive system can be
excessively stressed.
6.1.
Ordinary maintenance
• Any interventions must be performed when the machine is cold, stopped and switched off.
• Installation and maintenance must be operated only by qualified personnel wearing the proper clothes and the necessary tools as well as
protection devices.
• Use suitable protection equipment (gloves, protection glasses, boots...)
• In the following table summarizes the main controls to be performed and the frequency of intervention.
Operating
Condition
Maintenance Area
Check
8
H
50
H
500
H
1000H
OPERATING
Vacuum line
Check safety valve (non-return valve)
Operating pressure
Transmission / Pump
Lubrication: dripping into oilers
Rotation speed
Sound pressure level (also HDR motor)
STANDSTILL
Vacuum line
Suctions filters
4-way changeover valve: check and lubricate
Pump
Clean oilers glasses
Check oil level
Check vanes wear
Change oil (*)
Pump’s inner washing (**)
Overall
Greasing
Check cardan shaft drive
Chack transmission pulley
Swing valve wear check
(*) The first oil change must be done inside 500 hours operation. Following changes every 5000 hours or 12 months. In order to choose the most
suitable oil, see paragraph 2.5.
(**) After operation in dusty environments, after accidental sucking of liquids inside the pump or before a long inoperativity period it is
recommended to wash the pump inside according to the procedure described at paragraph 5.2.
6. Maintenance