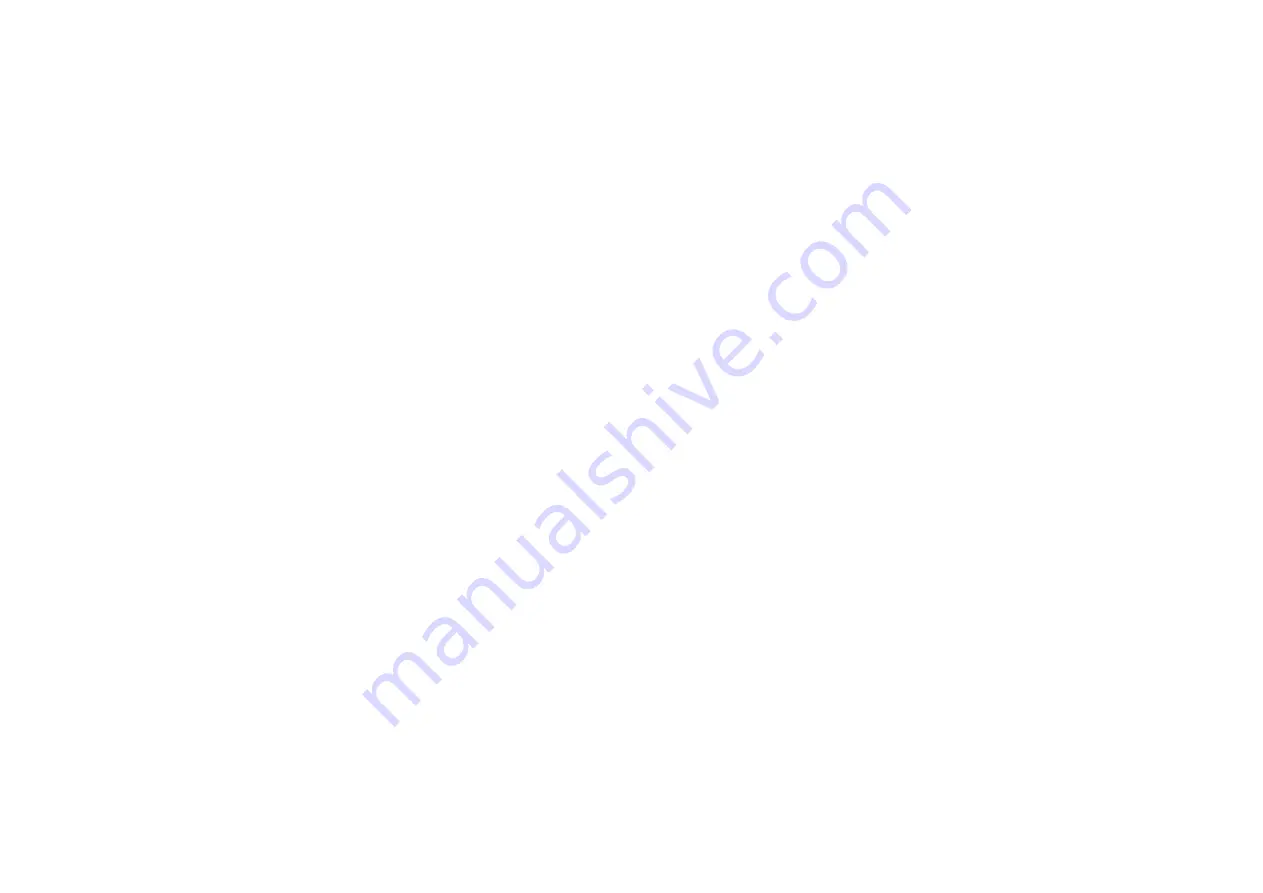
F 3
0708
.GB
3
Servicing and Inspection
Thorough and expert servicing is one of the most important requirements for the safe
operation of the industrial truck. Failure to perform regular servicing can lead to truck
failure and poses a potential hazard to personnel and equipment.
M
The application conditions of an industrial truck have a considerable impact on the
wear of the service components.
We recommend that a Jungheinrich customer service adviser carries out an
application analysis on site to work out specific service intervals to prevent damage
due to wear.
The service intervals stated are based on single shift operation under normal
operating conditions. They must be reduced accordingly if the truck is to be used in
conditions of extreme dust, temperature fluctuations or multiple shifts.
The following servicing checklist indicates the operations to be performed and the
respective intervals to be observed. Maintenance intervals are defined as:
W
= Every
50
service hours, at least weekly
A
= Every 500
service
hours, or at least annually.
B
= Every 1000
service
hours, or at least annually.
C
= Every 2000
service
hours, or at least annually.
Z
W service intervals are to be performed by the customer.
During the run-in period – after approx. 100 service hours – the owner must check
the wheel nuts/bolts and re-tighten if necessary.
F 3
0708
.GB
3
Servicing and Inspection
Thorough and expert servicing is one of the most important requirements for the safe
operation of the industrial truck. Failure to perform regular servicing can lead to truck
failure and poses a potential hazard to personnel and equipment.
M
The application conditions of an industrial truck have a considerable impact on the
wear of the service components.
We recommend that a Jungheinrich customer service adviser carries out an
application analysis on site to work out specific service intervals to prevent damage
due to wear.
The service intervals stated are based on single shift operation under normal
operating conditions. They must be reduced accordingly if the truck is to be used in
conditions of extreme dust, temperature fluctuations or multiple shifts.
The following servicing checklist indicates the operations to be performed and the
respective intervals to be observed. Maintenance intervals are defined as:
W
= Every
50
service hours, at least weekly
A
= Every 500
service
hours, or at least annually.
B
= Every 1000
service
hours, or at least annually.
C
= Every 2000
service
hours, or at least annually.
Z
W service intervals are to be performed by the customer.
During the run-in period – after approx. 100 service hours – the owner must check
the wheel nuts/bolts and re-tighten if necessary.
Summary of Contents for ECE 220
Page 1: ...Operating Instructions 51051908 G 12 06 07 08 ECE 220 225 ECE 220XL 225XL...
Page 3: ...0108 GB 0108 GB...
Page 7: ...0708 GB I 4 0708 GB I 4...
Page 9: ...0506 GB 2 0506 GB 2...
Page 11: ......
Page 91: ...0506 GB 18 0506 GB 18...