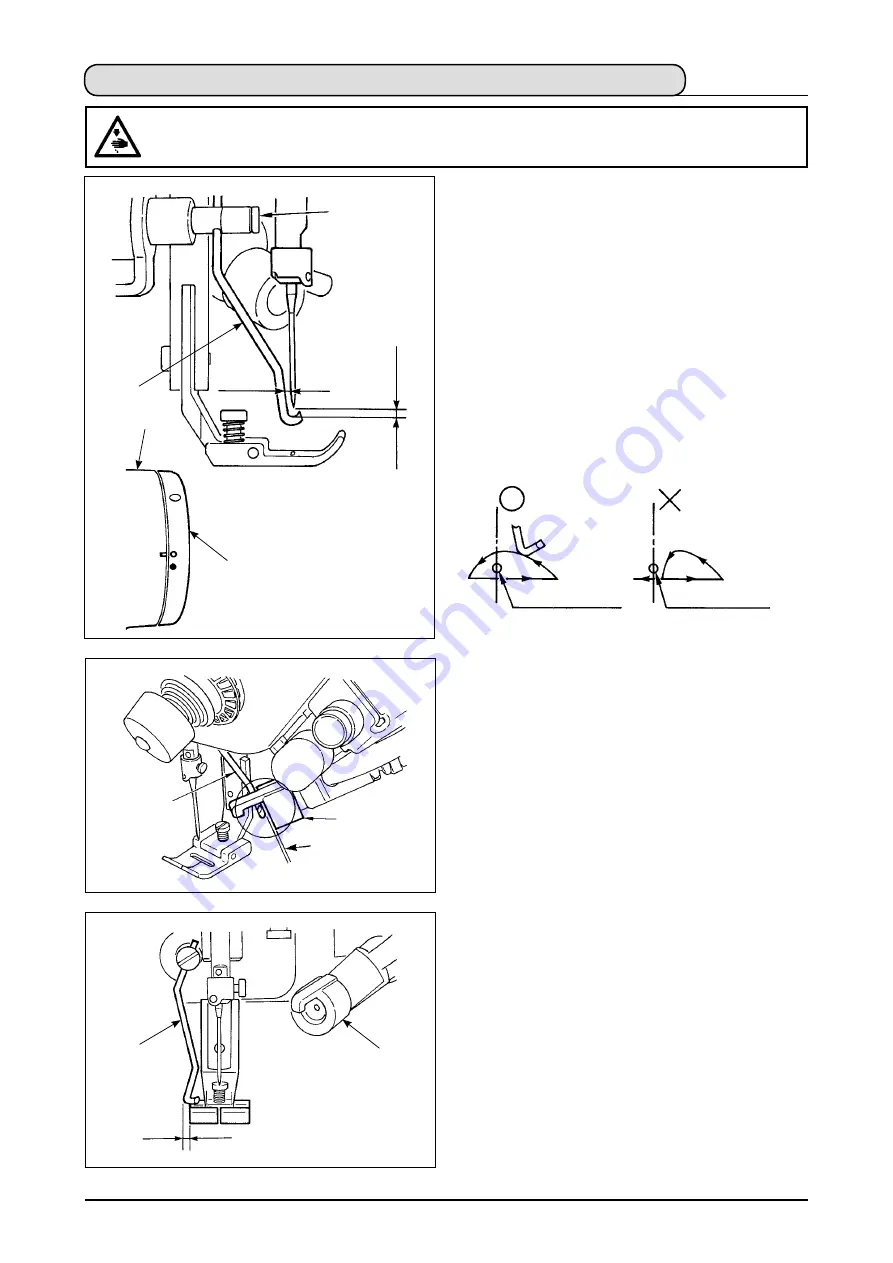
104
2) The top end plane of wper
3
should be pos-
toned to be almost parallel to the end plane of
clamp head
4
. Besdes, set the clamp head so
that the upper sde s the protrudng secton.
3) Adjust the maxmum stroke of the wper to the po-
ston of 1 to 3 mm from the left end plane of the
presser of standard delvery.
™
Presser (asm.) of standard delvery
(Part No. 40003542)
™
Optonal
Presser (asm.) for narrow wdth
(Part No. 40003549)
■
Position of the wiper
1) Adjust the whte marker dot on the handwheel
1
to
the poston where t s algned wth the marker dot
on the pulley cover
2
, quetly press wper lnk A to
move wper
3
. The wper recedes by the ratchet
when gong and the poston where the wper returns
to ts home poston s n the center of needle or the
poston exceedng the center of needle.
Besdes, adjust wth wper setscrew
5
so that when
wper
3
comes to the poston of the center of nee-
dle when returnng, the clearance between the wper
and the needle tp should be approxmately 2 mm
and that between the wper and the sde of needle
should be approxmately 1 mm.
2 mm
0.5 to 1 mm
Needle
(8 mm zgzag
extreme left)
Needle
(8 mm zgzag
extreme left)
WArNING :
To protect against possible personal injury due to abrupt start of the machine, be sure to start the
following work after turning the power off and ascertaining that the motor is at rest.
To be convex by 1 to 3 mm
To be almost
parallel
8-13. Adjusting the bird's nest prevention (CB) type wiper
3
2
1
4
3
4
3
5