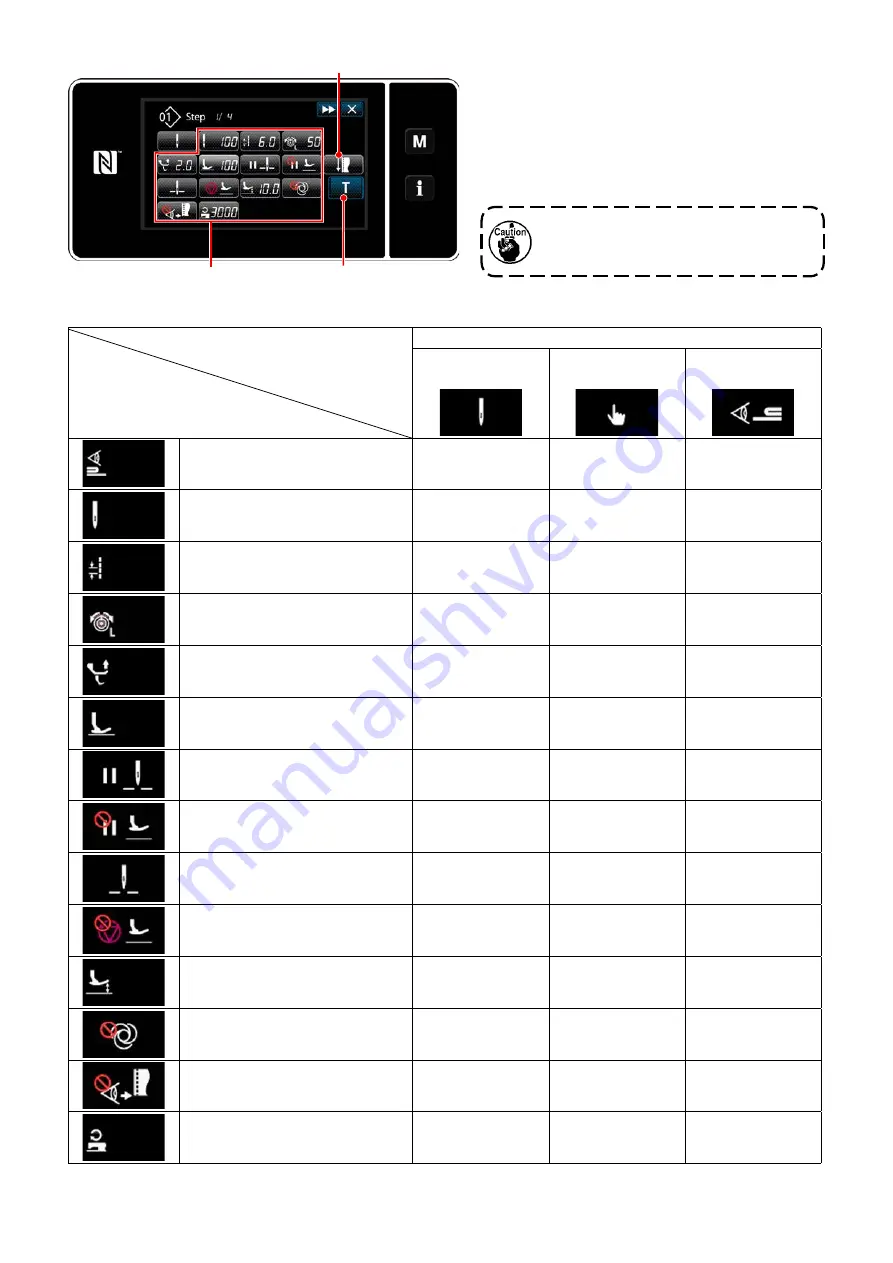
– 123 –
5) Setting other sewing data
❽
.
The type of sewing data displayed on the
"sewing data edit screen" changes according
to the step changeover reference selected in
the aforementioned item number 3. (See the
table shown below.)
<Sewing data edit screen>
❽
❾
The presser lifter operates after thread
trimming according to the setting of the
final step.
Step changeover reference
Number of stitches
Hand switch
Multi-layered part
detection
Step changeover sensor value
×
×
○
Number of stitches
○
×
×
Stitch length
○
○
○
Needle thread tension
○
○
○
Alternating vertical movement
amount
○
○
○
Presser foot pressure
○
○
○
Intermediate stop - Needle bar
stop position
○
○
○
Intermediate stop - Presser foot
lifting
○
○
○
Stop - Needle bar position
○
○
○
Stop - Presser foot lifting
○
○
○
Stop - Presser foot lifting height
○
○
○
One shot
○
○
○
Material edge sensor
○
○
○
Sewing speed limit
○
○
○