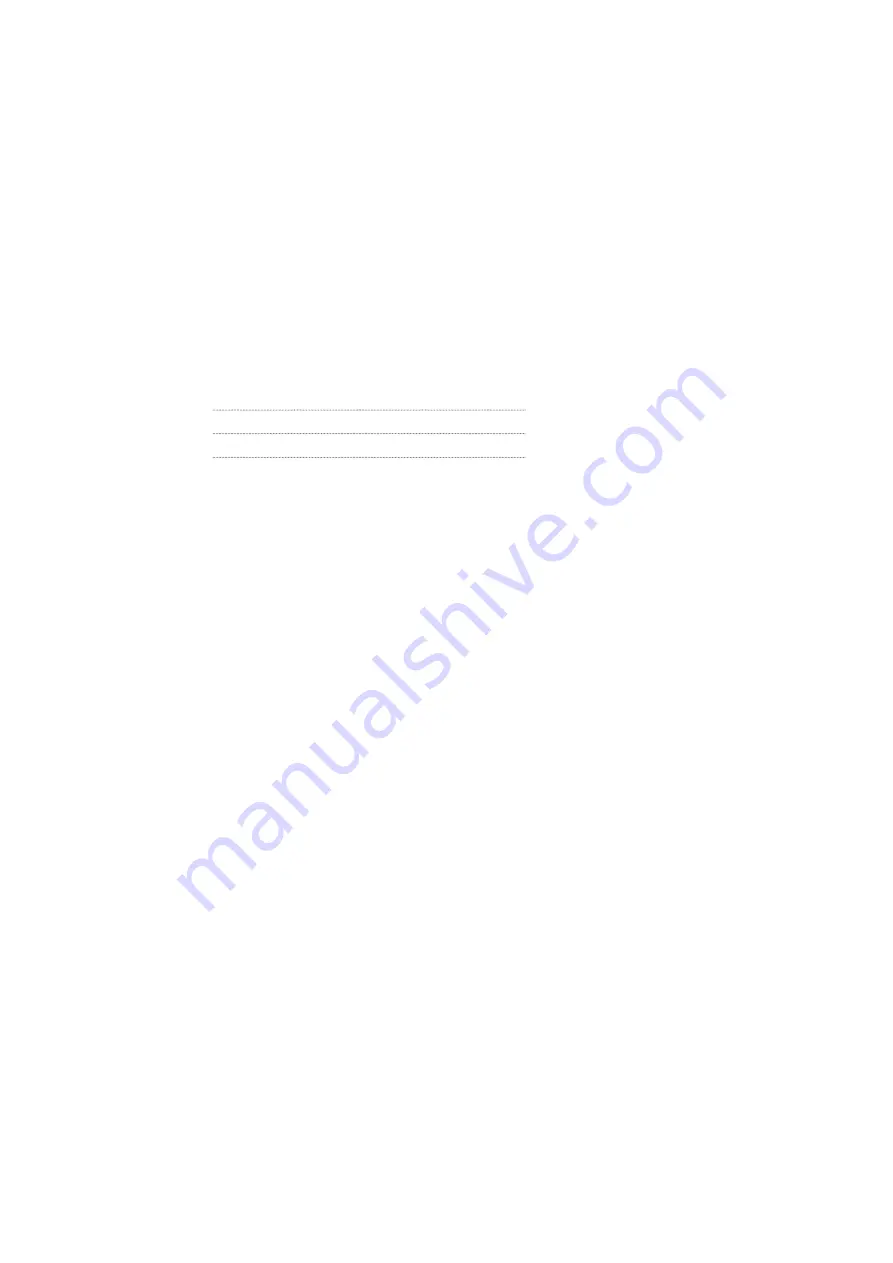
– 10 –
17. ADJUSTING THE HEIGHT OF THE FEED DOG
WARNING :
To protect against possible personal injury due to abrupt start of the machine, be sure to start the following
work after turning the power off and ascertaining that the motor is at rest.
16. ADJUSTING THE STITCH LENGTH
18. ON REVERSE SEWING
While pushing the feed adjusting button
❶
, rotate the handwheel and when the
end of the button has entered the groove of the cam, rotate the handwheel fore
and aft while the feed adjusting button
❶
is being pushed, until the desired
fi
g-
ure of the graduator plate is matched with the carved line
❷
of the feed adjuster.
When the desired
fi
gure and the carved line
❷
are matched, release the feed
adjusting button.
The
fi
gure indicates the length of the stitch in mm unit. (10
→
stitch length =
10
mm (25/64”)).
The
fi
gure on the graduation plate can be seen from the sight window even with
the top cover in closed condition.
The maximum height of the feed dog above the throat plate is 1.2 - 1.4 mm (3/64
- 1/16”).
Adjust to this position by loosening the screw
❶
.
* When the feed dog is exchanged, be sure to tighten the
❷
set screw of the
feed dog
fi
rmly. Further, loosen nut
❷
, tighten screw
❸
so that screw push
up the feed dog lightly and tighten the nut
❷
.
* In case the height of the feed dog does not become parallel, adjust by screw
❸
.
Hang the chain to the lifting crank link spring latch plate
❶
with a hook and catch
the other end of the chain to the pedal.
When reverse sewing is to be performed, step on this pedal until the variable
speed link hits the stopper
❷
.
❶
❷
❶
❸
❷
❶
❷
vi
DECLARATION OF INCORPORATION OF PARTLY COMPLETED MACHINERY
We hereby declare that the sewing machine (sewing head) described below ;
1. Must not be put into service until the machinery to which it is incorporated has been declared in
conformity with the provisions of the Directive 2006/42/EC, and
2. Conforms to the essential requirements of the Directive 2006/42/EC, described in the technical
documentation, and
3. To be prepared with the above technical documentation compiled in accordance with part B of
Annex VII, and
4. Also to conform to the RoHS Directive 2011/65/EU
5. Relevant information on which should be transmitted in response to a reasoned request by the
national authorities, by the electronic method or other according to the request.
Applied harmonized standards, in particular :
EN ISO12100, EN ISO10821, EN 50581
Manufacturer :
JUKI CORPORATION
2-11-1, Tsurumaki, Tama-shi, Tokyo, Japan
Model
Description
Industrial Sewing Machine
Function
make stitches and sew
LG-158 Series