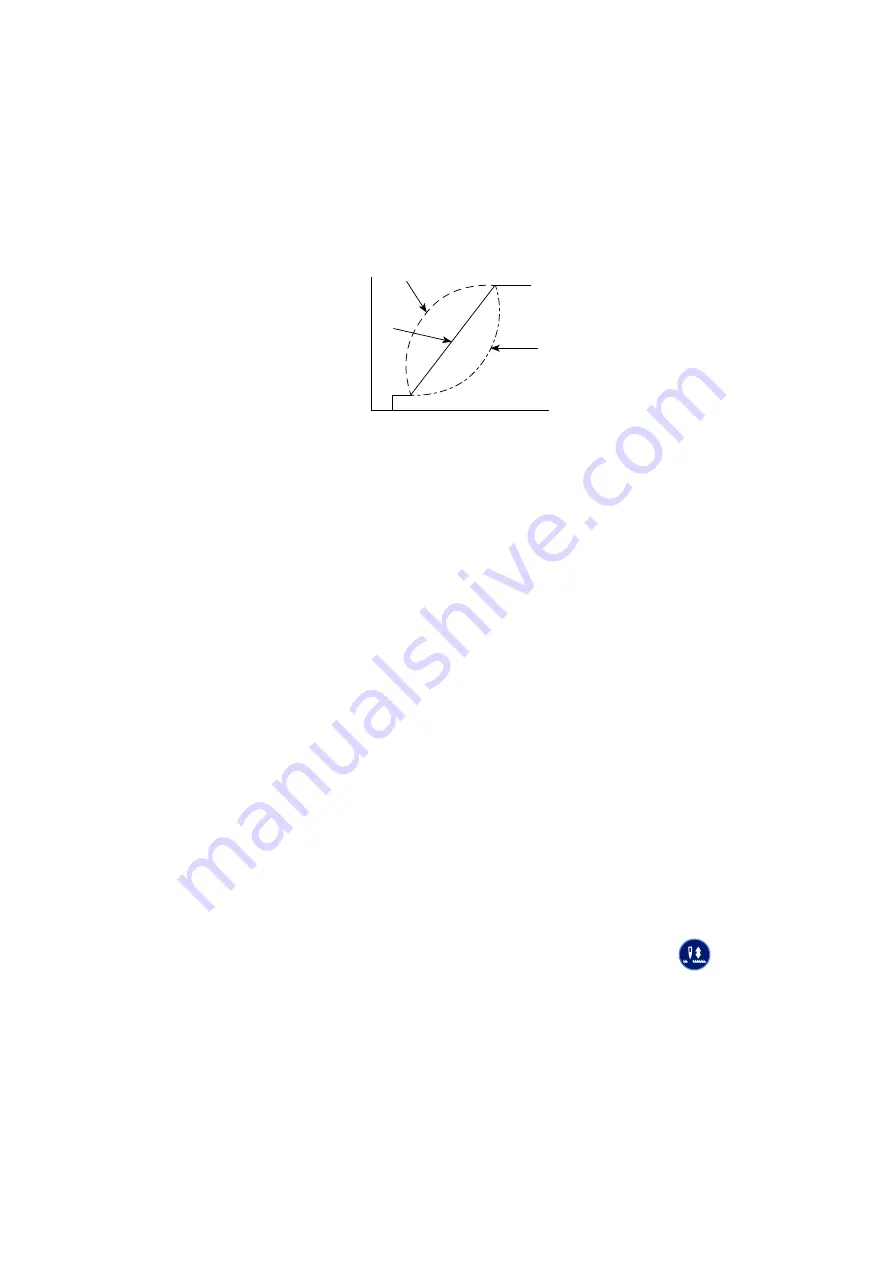
– 37 –
⑨
Function of pedal curve selection (Function setting No. P138)
This function can perform the selection of the curve of sewing speed of the sewing machine against the
depressing amount of the pedal.
Change to this function when you feel that inching operation is hard or that pedal response is slow.
8
1 3
0 : Sewing speed in terms of the depressing amount of the pedal increases linearly.
1 : Reaction to intermediate speed in terms of the depressing amount of the pedal is de-
layed.
2 : Reaction to intermediate speed in terms of the depressing amount of the pedal is ad-
vanced.
Sewing speed (sti/min)
Pedal stroke (mm)
0
1
2
⑩
Selection of the presser foot operation when the power is turned ON (Function setting No. P136)
The needle bar goes up to its upper position and the presser motor carries out origin retrieval operation
immediately after the power is turned ON.
6
1 3
0: Neither the needle bar nor the presser motor (Operates when the back part of pedal is
depressed)
1: Needle bar goes up to its upper position and the presser motor automatically goes up
after automatic origin retrieval.
2: Needle bar automatically goes up to its upper position and the presser motor comes
down after automatic origin retrieval.
⑪
Setting of the operation of needle up/down switch after thread trimming (Function setting No. P118)
One stitch operation can be performed only when the needle up / down compensating switch is pressed
at the time of upper stop immediately after turning ON the power switch or upper stop immediately after
thread trimming.
8
1 1
0 : Normal (Only needle up / down compensating stitching operation)
1 : One stitch compensating stitching operation (upper stop / upper stop) is performed only
when aforementioned changeover is made.
⑫
Thread trimming counter (Function setting No. P41)
1
P 4
This parameter is used to display the current value of the thread trimming counter.
The sewing machine is able to perform sewing while displaying the counter value.
To reset the counter to 0 (zero), press needle up / down correction key
.